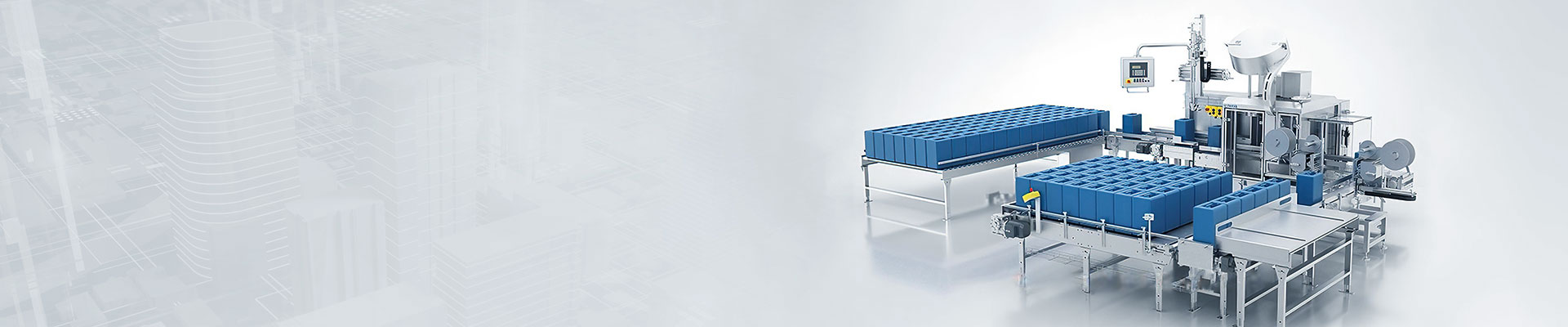
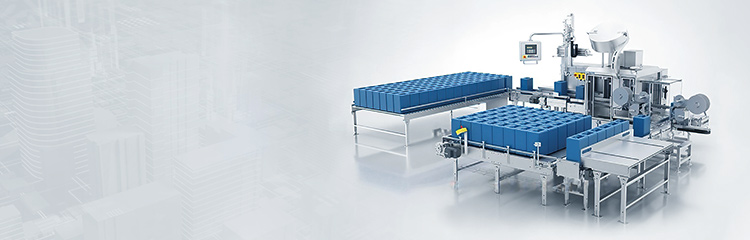
The automatic feeding machine can realize data acquisition, program control and information exchange with the management of the equipment layer. According to the structure of the IN_TERBUS system, in addition to the centralized diagnostic display on the bus control board, each module scattered in the system also has the corresponding system running status display, through the diagnostic display content, the operator can get the state of the INTERBUS system without the help of any other tools.

The feeding system uses the computer dosage as the control center and controls the other equipment to complete the dosage. The raw materials are driven by a screw which falls from the silo into the hopper scale and conveys the different materials separately. The speed of the spiral is regulated by a frequency converter according to the output voltage of the weighing instrument. The dosage recipe and batch are set through the keyboard of the weighing instrument and then the system is run, the weighing instrument automatically selects the required silo and drives the spiral motor so that the material falls into the hopper scale, and the speed of the spiral is adjusted by the weighing module that measures the weight of the hopper scale to control the amount of material to be fed, so that the end point value reaches When the batching is finished, the door will be opened automatically, and the materials will enter the mixer to mix, the weighing instrument will calculate the mixing time automatically, and when the mixing is finished, the finished products will be discharged.
When the dosage control system is working, two dosage scales feed the materials at the same time, and the computer monitors the two scales by time. The Feeder adopts spiral type, and the computer controls the starting and stopping of the feeder motor corresponding to each material through the corresponding control software according to the programmed feeding order. The size of the dosage is determined by the recipe calculation. The formula can be calculated by the optimization method, or manually calculated and input into the computer. The whole control system consists of controller (computer), weight detection device and actuator, etc. The controller is the core of the whole batching machine, including hardware and software. The hardware consists of a microcomputer, amplification circuit, interface circuit and other parts. The interface circuit includes switch input and output circuit and analog input and output circuit. The software of weighing terminal is to command the whole Dosage system to work orderly and accurately on the basis of hardware.
The software of automatic feeding system includes two parts: production process control software and production management software. The production process control can monitor the batching and mixing process of multi-bin and several scales. The control software compensates for temperature, non-linearity, hysteresis and other errors; the data acquisition adopts a filtering program to improve the dosage accuracy. The production management software consists of formula management, bin management, report management, system calibration, material and nutrition management, parameter setting, etc. It can work with the production process control program to design, modify, retrieve and print the formula, arrange bins, design the feeding order, set up multi-bin feeding, as well as retrieve and print the report, calibrate the dosage scales, and calculate the material and nutrient content. Through the production management program, flexible, convenient and reasonable forms of control can be realized.