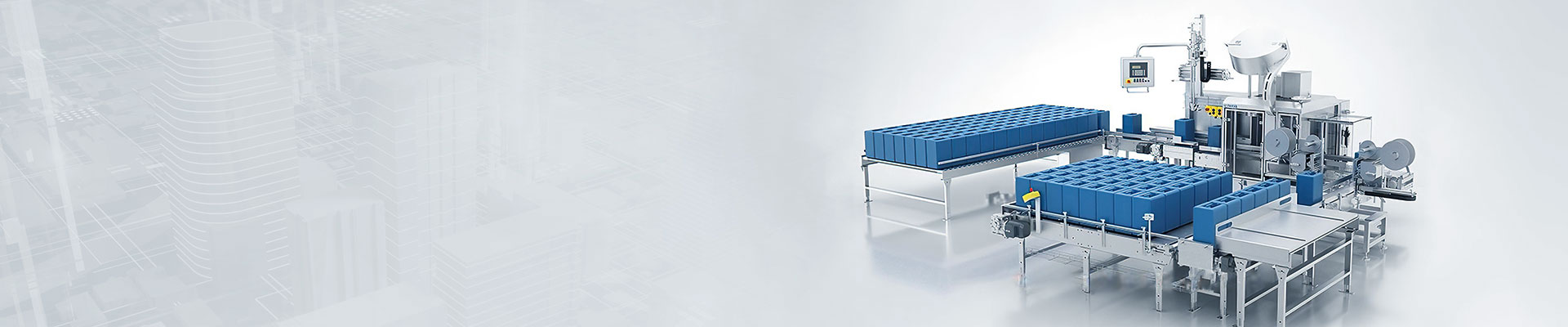
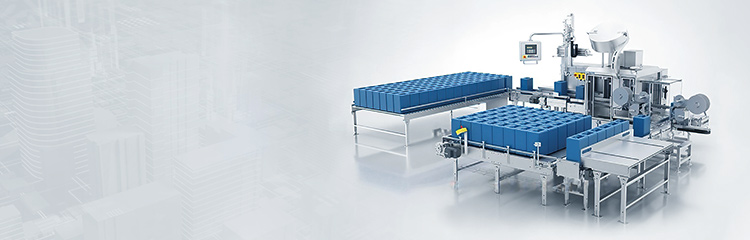
The new error-proofing mechanism and weighing system adopted in the feeding equipment greatly improves the product quality and efficiency of the production batching. The whole process control system makes the whole production process control, production plan management, material management, quality tracking management in one, and really realizes the control in one, which plays an important role in enhancing the management level, improving the product quality and maintaining the product stability, and it is more convenient for the customers to remotely monitor the inventory of the production factory and the production equipment and other related information across the regions, provinces and countries.

The dosing system is set and monitored by the industrial control machine, and the value of the pid regulator can also be modified manually, which is easy to operate and reliable in control, and the whole dosage realizes a high degree of automation, forming a closed-loop control system that is both relatively independent and interconnected.
The final control object of the batching machine is the reactor screw Feeder. The rotating speed of the reactor screw feeder is controlled by the frequency converter to control the size of its capacity, through the pid regulator will be sent to the upper computer to compare the flow signal with the given value, according to the size of the deviation, the output of 4 ~ 20ma signal to adjust the frequency converter, so as to achieve a constant flow rate, to achieve the desired results.
The dosage process of the feeding system is divided into two stages: feeding and unloading. After the dosage starts, the feeding feeder is started firstly, and the controller detects and samples the material weight of the hopper scale, and stops feeding when the material weight of the hopper scale reaches the upper limit value set for dosage. At the same time, the controller detects and samples the material weight of the hopper scale, and stops feeding when the material weight of the hopper scale (feeding quantity) reaches the upper limit value set by the dosage. In the unloading stage, the controller starts the unloading feeder to unload the materials in the hopper scale to the next level of material transfer equipment to send away. When unloading, the controller detects and samples the weight of the material in the hopper scale, and when the weight of the material in the hopper scale reaches the lower limit value set by the dosage, it will re-feed the material to the hopper scale. However, after the second feeding phase begins, the unloading feeder continues to unload without stopping.
Functional operating instructions
Manual/Automatic control
The screen is equipped with a display of the working status. In the absence of dosage or in the state of dosage pause, the dosage winches can be switched on manually at will, but only one winches can be switched on at a time. You only need to click on the corresponding winch motor on the screen, a dialog box will pop up, and the motor can be turned on/off. Manual operation is not valid during the dosage process.
Material Definition
Click the [Material Definition] button to open the Material Definition screen, and fill in the names of the ingredients according to all the recipes, which is convenient for the statistics of material consumption.
Recipe Setting
Before dosage, you must set the recipe, click [Recipe Setting] button to pop up the recipe setting screen. The recipe setting screen has the following parameters to fill in.
Bin No.: the bin number of the raw material to be dosed; in the dosage control, the digital system automatically opens the motor winch for dosage according to the selected bin number.
Material Name: Fill in the name of the raw material corresponding to the bin number, it can be Chinese, English or numeric, etc., but it must be the same as the name in the [Material Definition] table.
Target weight value: the weight value (Kg) to be reached by various raw materials in the formula, also can be said to be the theoretical value.
Fast add advance: also known as the amount of frequency conversion, when starting, the frequency converter quickly add material, when the actual weight of the bin is still left from the target set weight this value, the frequency converter is changed from high frequency to low frequency, and enter into the slow dosing state. The size of this value is adjusted according to the actual situation. If it is too big, it will reduce the dosage speed; if it is too small, it is easy to overshoot, thus reducing the dosage precision.
Slowly add the amount of advance: that is, the drop value, the value of the material falling into the weighing hopper when the dosage winch stops. The size of this value is adjusted according to the actual situation. If it is too big, the actual weight value of the dosage will be less; if it is too small, the actual weight value of the dosage will be more.
Selection of the recipe
Click [Select Recipe] button, the pre-set recipe name will pop up, select the recipe name of the required dosage and press [Confirm].
Load Recipe
Click [Recipe Input] button, the dialog box of input recipe name will be popped up, manually input the recipe name of the required ingredient, and then press [Confirm].
Save Recipe
When the formula is modified in the digital system, you need to save it to the current formula name or save it as other formula name, click [Save Formula] button, the dialog box of inputting formula name will pop up, the initial value is the current formula name, press [Confirm] to save it to the current formula name; if you save it as other formula, manually input the formula name, press [Confirm] to save it as other formula name.
Delete Recipe
Click the [Delete Recipe] button, a confirmation prompt dialog box will pop up, press [Confirm] to delete the currently displayed recipe number.
Download Recipe
Click [Download Recipe] button, you can download the currently selected recipe parameters to PLC, the prompt shows "Recipe has been downloaded ......". Before dosage production, all the parameters of the selected recipe name should be downloaded, otherwise the system will dosage according to the previous recipe.
Parameter Setting
After setting the recipe, you need to set the dosage control parameters. Click [Parameter Setting] button to open the control parameter setting screen, and set the parameters according to the production requirements.
Production Batch: Set the current number of times for automatic dosage.
Mixing time: set the mixing time for the dosage, when there is additive, the timing will start from receiving the answer signal of the end of adding, when there is no additive, the timing will start from closing the door of the discharging scale in place.
Mixer discharge time: the time to open the door for discharging, i.e. from the receipt of the signal to open the door in place to start timing, at the end of the time, the door will be closed automatically.
Weight value when adding signal is sent: i.e. when the weight value after unloading is less than or equal to the set value, a signal is sent to add small materials. When the set value is zero, it means no additive is added; when the set value is not zero, it will notify the site to add additives.
Door open alarm time: that is, from the unloading signal issued to start timing, when it reaches the set time, that is, issued unloading fault alarm.
Delay time for adding small materials: that is, from the start of the add signal timing, when the set time is reached, that is, the "small materials to add no answer!" Alarm prompt.
Near zero value: when the weight value after unloading is less than the set value, it is regarded as zero value, which indicates the end of unloading, and the unloading door will be closed. When the set value is too large, it will easily lead to the unloading is not complete to close the door; when the set value is too small, it is often because of the weighing hopper wall sticky material and can not automatically close the door, resulting in unloading fault alarm.
Dosing order: the automatic dosing system sets the order of the current production formula. The set value is "0", which means that the material of the bin number is not involved in the dosage.
Exit in the middle
When the set production batch is not yet completed, but need to terminate the dosage of the current recipe number, press the [Quit Midway] button, confirm according to the prompts, the system will automatically quit after the current batch is finished, and prompt that the dosage has been completed.
Out of material change
When the dosage process, the dosage tank number material has been dosed, the system automatically prompts the lack of material alarm. Press [change dosage tank for lack of material] button, a dialog box will pop up, enter the dosage tank number to be replaced, make sure, and then press [Clear Fault] button, then the dosage tank can be changed and enter the automatic dosage state. Note: After changing the dosage tank, the dosage sequence must be changed. Set the missing dosage tank to 0, and set the new dosage tank number to be the same as the original order, which is convenient for report statistics.
Real-time display of each batch of dosage process data, such as the target value, actual value, error value and total value of each material.
Query the list of production process by formula number, date, shift, etc., which is convenient to understand the production situation and analyze the faults.
Page setup, report preview and report printing are available.
Daily Statistical Report List
Queries by recipe number, date, shift, etc. The query result shows the total batch of the day's production, the theoretical value, the actual value and the error value of the required materials and the total production; at the same time, it displays the total batch of the current query formula number or shift and the list of consumed materials, etc. It is possible to set up the page, preview the report and print the report.
Daily report inquiry
You can query the raw material consumption and production of the day and the previous daily report, which is convenient for production statistics and management, and you can set the page, report preview and report printing.
Monthly Report Inquiry
You can query the raw material consumption and production monthly report of the month and before, which is convenient for production statistics and management, and you can set the page, report printing preview and report printing.