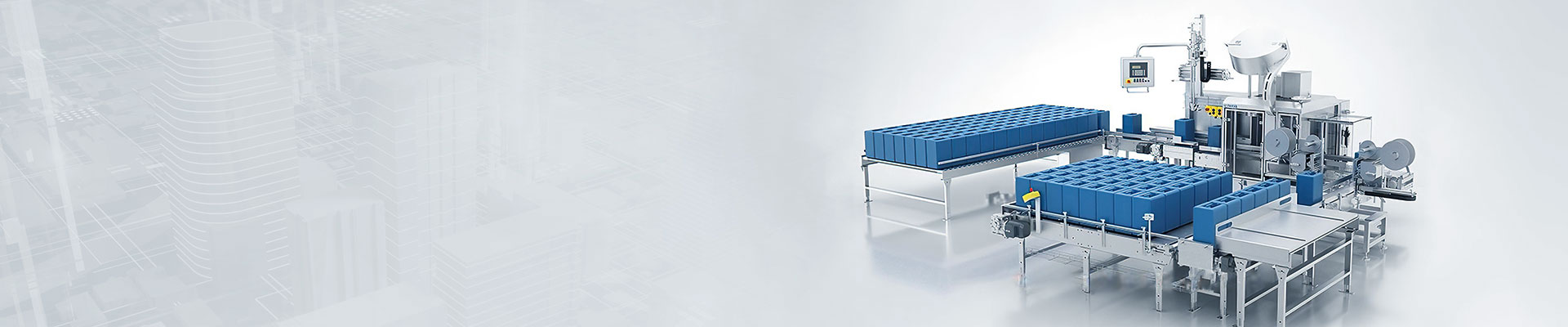
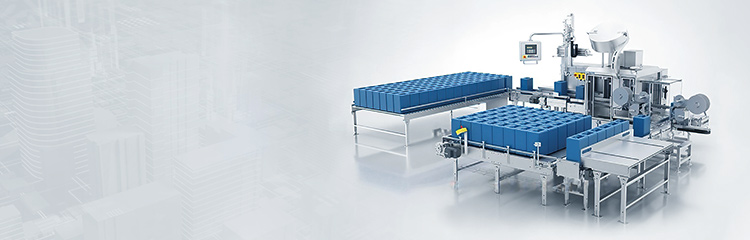
The pneumatic feeding system uses the high speed air flow of nitrogen or air to suspend the powder in the pipeline through the injector, and the powder in the suspended state is transported to the end user along the closed pipeline under the high speed air flow.

The pneumatic feeding system uses the high speed air flow of nitrogen or air to suspend the powder in the pipeline through the injector, and the powder in the suspended state is transported to the end user along the closed pipeline under the high speed air flow. Process operation process:
1) First start the roots blower, Roots blower control can be completed by a complete set of controllers;
2) Open the bag filter, and the bag filter blows compressed air to the bag in pulse form according to the set program to remove the dust on the bag surface;
3) Open the shaft seal valve XV24101 of the rotating feed valve (air closing valve). After completing the above steps, check whether the wind pressure meets the requirements. If the requirements are met, the feeding process can be started by starting the rotary feed valve 4X01, and the powder enters the injector from the feed bin through 4X01. At this time, the powder is suspended in the pipeline under the high-speed air flow, and the powder is transported forward along the closed pipeline into the 1# or 2# powder receiving bin. Specific access to the receiving bin 1# or 2# can be achieved through the reversing valve XV23101, which is equipped with a valve position switch. Each receiving bin is equipped with upper and lower limit capacitive level switches to determine whether the bin is allowed to be filled.
The whole feeding process can be completed in a fully automatic situation, as long as the PLC detects the feeding signal given by the subsequent process, the interlock control program automatically executes the feeding process. After the automatic/manual switching function is added to the interlock control program, manual operation can be realized.
The interlocking sequence control process is as follows.
Activate the loading button in the field or control room to begin the interlock control loading procedure:
1) First determine whether 1# warehouse can be filled, such as 1# warehouse can be filled, the PLC gives the sound and light prompt, and the loading begins.
2) Start the following devices in turn. Set the reversing valve XV23101 in S direction, start the bag filter 1Z01 control program, open XV24101, and then start the Roots blower 5A01 control program.
3) Determine whether the wind pressure is normal. If the wind pressure is normal, the PLC will give the sound and light prompt and start the rotating feed valve (air shut-off).
4) In the feeding state, continuously detect whether the wind pressure is normal until the 1# bin is full. If the wind pressure is abnormal during the feeding period, the feeding will be stopped. At the same time, the sound and light alarm will be carried out, the rotating feeding valve (air shut-off) will be stopped, and the blower will be stopped after a delay of 30 seconds.
5) If the 1# warehouse is full, the PLC gives the sound and light prompt, and then judge whether the 2# warehouse can be filled, if it can be filled, the PLC gives the sound and light prompt, the loading process is the same as above.
6) If the 1# and 2# bins are full, the audible and visual alarm displays, stop feeding, stop rotating the feed valve (air shut-off), and stop the blower with a delay of 30s.