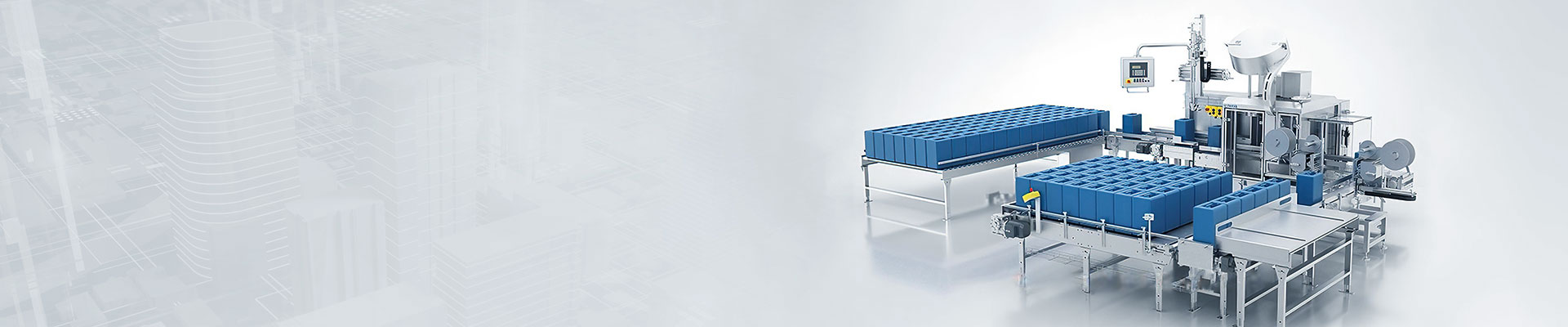
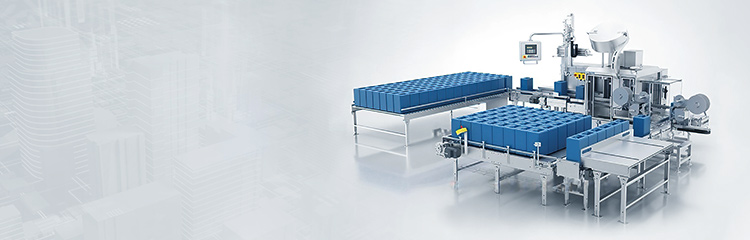
Industrial filling machines offer help to fill liquids or powders into containers from one side entry, with a linear filling and capping system mounted on the wall that fits neatly into any space. Provides a single solution using aseptic filling and capping requirements. Modular design is easy to configure - enables simple integration with isolators to ensure maximum sterility and operator safety.

Automatic Filling machine consists of industrial control computer, weighing instrument, frequency converter, Filling system, etc. In the control process of filling, using the upper computer to connect the command to monitor the operation status of the lower machine and the content of the data area, real-time reading of the internal state of the weighing instrument and quantitative filling of real-time data, and display the data in the upper computer, with reporting functions, can generate daily reports, real-time reports, monthly reports, annual reports and so on. Dynamically add and modify the report, the filling machine gives the technician or operator the right to modify and add the filling form by setting the permissions, and at the same time records the date of modification and the number of operators. Power failure recovery function:In case of sudden power failure, it can recover the measurement records before the power failure; LAN sharing function, the host can share the data in LAN, which is convenient for the workshop supervisor to know the progress of the project and so on.
Weighing and filling machine with capper and labeler in a production line that can optionally include filling solutions, can handle different types of liquid products, liquid or thick, foamed or non-foamed, and filled in different packaging formats, consisting of filling, capping, sealing, palletizing, weighing equipment and the corresponding conveyor belts, complemented by an automatic control and automatic adjustment system. Full recipe control via HMI, integrated into the machine's human-machine interface, enabling SMART remote support, real-time statistics and performance analysis, and feedback for manufacturer improvements.
Basic parameters:
Maximum weighing capacity: 30kg
Minimum Sensitivity: 0.01kg
Filling error: ±0.01-0.02kg
Filling speed: 20L about 150-180 barrels/hour
Control mode: 2-speed control
Filling method: Insertion, liquid level up
Gun head line: Teflon gun head, valve + Teflon hose
Structure material: host SUS304 stainless steel, conveying palletizing carbon steel anticorrosion paint.
Weighing platform size: 400 × 800mm (304 stainless steel power raceway)
Empty barrel raceway: 400mm × 2500mm (304 stainless steel power raceway) with another 1200mm slope without power roller
Heavy drum raceway: 400mm×2500mm (304 stainless steel power raceway, 2 sets)
Separate barrel device: for 20L barrels, carbon steel anticorrosive paint structure, 304 stainless steel raceway.
Palletizing equipment: pan-transfer type, suitable for pallets 1200×1200×140mm, including supplying pallets, palletizing, and lower pallet conveying.
Pipe pressure: 0.2-0.6MPa (related to material properties).
Material interface: DN40 flange connector 4, according to the user to provide interface standards
Air Connection: User supplied 12mm air hose connector for quick coupling connection
Power supply: AC220/50Hz (user-supplied to one side of the machine)
Using air source: 0.4-0.8Mpa (provided by the user to the side of the machine)
Use temperature: -10℃-50℃
Base conditions: solid concrete floor of the assistant suspension agent flat, concrete thickness should be more than 10cm.
Optional models: standard, explosion-proof filling