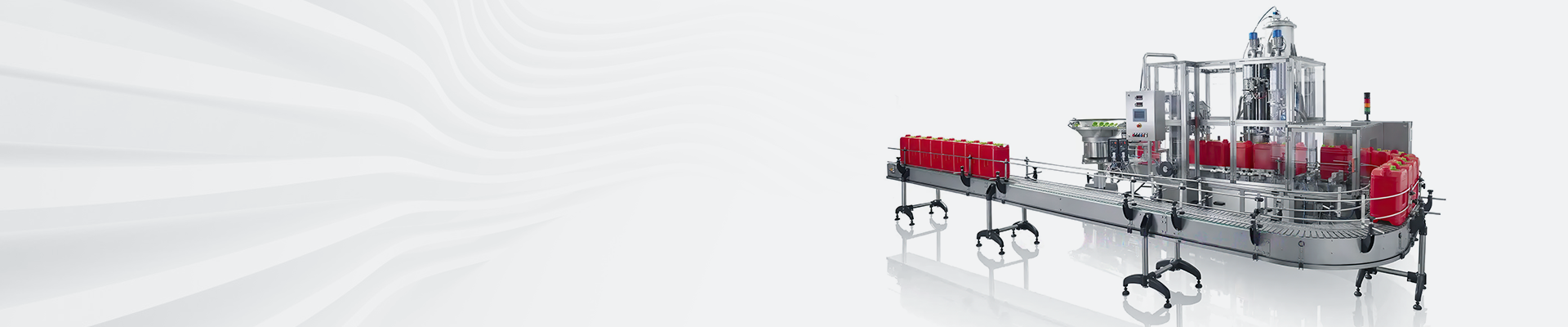
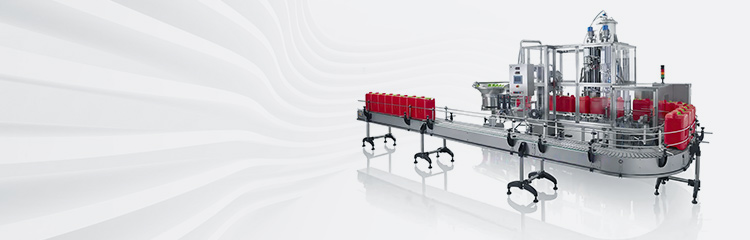

Summary:In order to improve the automation level of the automatic filling machine, avoid defective products from entering the market, and improve the efficiency of liquid filling detection.A machine vision automatic liquid filling machine detection method based on DSI and CCD cameras is proposed. The industrial CCD camera transmits the collected image signals to the DSP for image processing. Finally, the DSP transmits the detection results to the lower computer, PLC, and the PLC according to The test results control the elimination mechanism to eliminate defective products.A large number of experimental results prove that the detection line system can detect up to 20,000 bottles/hour and the accuracy is as high as 99.7%.This system can completely replace traditional manual inspection, greatly improve the inspection efficiency and accuracy, and effectively improve the automation level of the liquid filling production line.
At present, with the rapid development of liquid filling technology, the quality of liquid filling requirements are increasingly high. In the liquid filling process, there will usually be bottle mouth broken, unqualified level and the bottom of the bottle debris and other unqualified products into the market, on the brand and corporate image has caused a serious impact on the traditional liquid filling detection method is artificial light detection, but the detection method detection efficiency is low, labor intensity is high, the detection of the accuracy of the workers by the impact of the degree of visual fatigue, so the artificial light detection can not guarantee the detection of high efficiency and high accuracy. Machine vision inspection technology is an advanced inspection method developed in recent years, is a highly automated and intelligent inspection technology, through the industrial camera to capture the image, and through the computer image filtering, edge detection and other image processing, and finally through the programmable controller control actuators on the unqualified products to be rejected -. Machine vision detection has the advantages of high detection efficiency, high degree of automation, high detection accuracy, etc., and greatly reduces the labor force in the measurement process.4.3 Based on the above analysis this paper proposes a liquid filling production line inspection system based on the combination of DSP and CCD camera, which is triggered by photoelectric sensors to be captured by the camera, and then the captured information is transmitted to the image processing module, which passes through image denoising, Image processing module through the image denoising, image enhancement, image segmentation and other algorithms to process the collected image, and finally according to the judgment results will be transmitted to the PLC signal, PLC according to the information on the rejection mechanism for control.
1 Detection system three-dimensional structure
The filling system can be divided into two categories according to the transmission method: linear transmission and rotary transmission.
(1) empty bottle transmission and isometric bottle: this part in the detection system at the forefront, the part and the back end of the conveyor belt to connect, empty bottles through the washing machine clean, through the conveyor will be liquid bottles transferred to the bottle agencies, bottle agencies will be equidistant from the bottle to adjust to ensure that each bottle has a full detection time, by changing the speed of the bottle agencies can be adjusted to the spacing between the liquid bottle.
(2) Bottle detection: the liquid bottle to be detected is transmitted to the bottle detection module, the liquid bottle in the two reflectors through between, triggering the photoelectric sensor, the DSP will send the signal to the bottle CCD camera, the CCD camera after refraction through the reflector of the liquid bottle photographic cleaning to obtain accurate images.
(3) bottle mouth detection: bottle body detection is completed, is transported to the bottle mouth detection module, after the light source irradiation by the CCD camera for the bottle mouth to take pictures of the collected images will be transmitted to the DSP for further processing.
(4) Bottle Bottom Detection Module: Bottle Bottom Light Source selects backlight type illumination, the illumination can obtain a clearer edge profile.
(5) Bottle conveyor: the bottle is clamped by two parallel conveyor belts, and the conveyor belts utilize longitudinal gears with high resistance to ensure that the bottle is suspended during the transmission process, which facilitates smooth image acquisition of the bottle mouth, bottle bottom and bottle body.
(6) reject module: when the bottle mouth, bottle body, bottle bottom after the completion of the three detection process, the bottle through the tail positioning photoelectric switch and continue to run forward, the control system in the software to pass through the bottle to judge, if it is a defective PLC will be a high level signal sent to the solenoid valve, at this time, reject cylinder will be the action of defective bottles quickly rejected.
2 detection system hardware design
Machine vision detection system which mainly includes image acquisition module, image processing module, computer system intelligent processing module and control output of four major components. Analog-to-digital converter (ADC) will be the camera output image information into a digital image and by the CPLD will be stored in the image to the SRAM, SRAM and DSP links, the later image processing by the DSP; DSP processing image is completed, through the serial port, general-purpose input and output port output final results.
Image acquisition module: the selection of optical equipment needs to consider the transparent performance of the target, the vibration of the production line and the background environment changes and other issues, the selection of the image acquisition equipment should be able to adaptive adjustment according to the production environment of the light changes and the speed of the production line. Light source selection of long life, low power consumption, radiation-free LED light source image processing module: image processing module is the use of one or more digital signal processor DSP for high-speed computing, the collected images for denoising, edging, and a series of complex processing such as image enhancement, and its main feature is that it is running at a fast speed. In this paper, we chose the latest DSP chip TMS320C6201B of T company as the digital signal processing system, the core is able to reach 600MHzCIock, 4800MIPS processing speed. In addition the hardware is capable of repeated programming, according to the characteristics of the detected object as well as the detection of the purpose of the appropriate programming, and can be quickly through the JTAG interface to the program
Output control module: output control metering module controller core for Siemens S7-200PLC, mainly responsible for data reading and display, and give the relevant operating instructions and parameter settings. For example, when the detection unit found unqualified bottles will immediately set off the PLC for counting, in order to accurately calculate the position of the detection of the tail end of the machine sub-standard bottles, and send out the command to reject, so as to control the rejection mechanism will be sub-standard pushed into the bypass.
The memory unit is mainly composed of FASH and SDRAM, FLASH is mainly used for storing the system program code, the system reads the system program from FLASH every time when power is supplied, SDRAM is a synchronous dynamic randomized memory, adopting 3.3V operating voltage, with a bandwidth of 64 bits, SDRAM locks CPU and RAM together with the same clock, so that the clock cycle is shared between RAM and CPU at the same time, SDRAM can share the clock cycle at the same time. SDRAM is based on a dual memory structure, containing two interleaved storage arrays, when the CPU accesses data from one memory or array, the other is ready for data reading and writing, through the close switching of the two storage arrays, the reading efficiency has been doubled to improve the display unit mainly consists of LCD, LCD controller (S3C2400) touch screen. LCD is capable of real-time display of image processing structure. Can be real-time display of the image processing structure, the touch screen is mainly responsible for the control of the PLC system. I / 0 unit is mainly used for the system's input and out of the control, the system through the I / 0 digital output and input control of aliases in addition to the action of the mechanism.
3 detection system software design
Liquid filling machine machine vision detection system software consists of a number of modules to control and monitor the visual detection system, in the process of use, the user can flexibly select different modules according to actual needs, through a combination of different modules can be obtained through different functions of the detection system, the system software can complete the functions include:
(1) Online detection of liquid bottle body, bottle mouth and bottle bottom;
(2) Liquid bottle level height detection;
(3) Dirt detection inside the bottle;
(4) Rejection mechanism control of defective products and parameter settings such as rejection speed;
(5) Remote operation and fault code display;
(6) Historical alarm information storage and generation of fault data report;
Machine vision inspection system software mainly consists of image acquisition and detection module, output control module and monitoring module.
4 Experimental results analysis
In order to verify the reliability and stability of the machine vision filling system designed in this paper, the machine vision inspection system is compared with the artificial light detection, and 5 batches of 500mL of liquid on the production line are selected for detection of 300 bottles per batch. Detection speed is set at 20000 bottles / h, according to the actual working process of the liquid plant artificial light inspection speed of 1000 bottles / h. Detection of this set of machine vision inspection system misdetection rate and leakage rate, machine vision inspection system misdetection rate is significantly lower than the object rate of the artificial light inspection, machine vision inspection system leakage rate is also lower than the leakage rate of the artificial light inspection. Comprehensively, it can be seen that the set of intelligent automatic filling system has high detection accuracy and high detection efficiency.