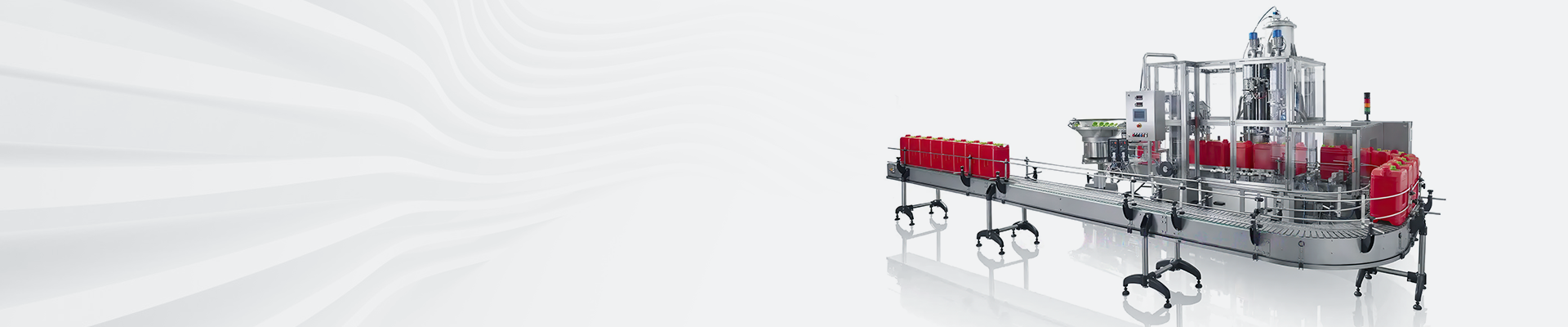
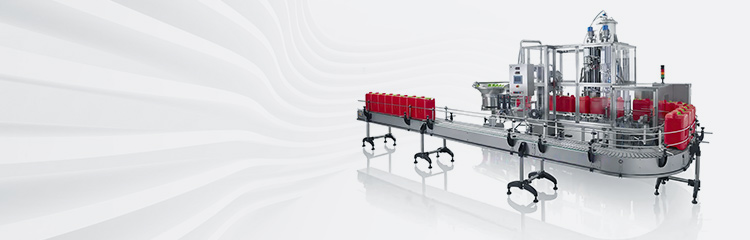

Summary:The fully automatic filling machine can complete the automated production line of weighing, mixing, transportation, storage and other links. The actual value of the weighing is fed back to the PLC, which is calculated by the PLC (replenishing amount = target weight - actual pre-filling weighing value). The amount needs to be refilled.
Automatic filling machine control requirements and control methods
1 control requirements
(1) the operation mode is set to automatic operation, open the switch to select "automatic", drive motor operation, drive conveyor belt operation, when the weighing sensor detects the bottle reaches the specified position is stopped, the conveyor belt stops running or stop switch start, the conveyor belt stops running. After the bottle is filled with liquid, the system automatically starts the motor, and the motor is driven again until it reaches another stop state and stops again, and this action is carried out cyclically.
(2) Positioning switch is set on the filling system, when the bottle reaches the specified position, the conveyor belt operation is suspended, and the weighing and filling machine then starts to carry out the filling work, and the filling is completed within 5S. If any abnormality or error occurs during this period, the system will send out an alarm signal in the mode of sound and light.
(3) There are two sensors and adders for detecting the state of bottles, and at the same time, the number of filled bottles and empty bottles are recorded respectively, and the counting starts from the operation of the system, generally 1 million bottles as a range.
(4) system reset and data zeroing take a manual approach to prevent data loss caused by automatic zeroing or system misoperation.
2 electrical control of each link
(1) counting: set the counter device, the number of bottles to be calculated and recorded, the counter will be connected to the PLC, through the touch screen control on the counting range to set and display.
(2) Filling: The production line is set up with front and back two bottle stop valves. When the front bottle stopper valve detects the empty bottle passing by, the automatic bottle stopper action will occur, and at the same time, the back bottle stopper valve will also start the bottle stopper action, and the filling equipment will start the filling operation. The filling port is controlled by a solenoid valve and a flow meter to ensure the accuracy of the filling volume and the consistency of the filling volume. Solenoid valve and flow meter are controlled by PLC.
(3) capping: capping machine is equipped with a specialized sensor to detect whether the bottle in place, when the bottle reaches the specified position, the PLC issued a command to control the capping machine capping action. After the capping is completed, the bottle stopper valve is put away, and the conveyor transfers the bottles to the next T-sequence point.
(4) Labeling: The production line is equipped with a specialized labeling machine, which automatically senses the bottles passed by the conveyor belt, and when the bottles arrive at the positioning point, the labeling machine starts the labeling action to complete the automatic labeling of the bottles.
(5) Coding: The automatic coding machine on the production line can sense the bottles for automatic coding operation.
In the whole filling production line, the servo system is used to control the running and stopping of the motor, so as to ensure the precision of the movement of bottles in the whole filling process. Automatic filling machine using a touch-screen man-machine exchange system for control, when the operation of the production line abnormalities or failures, the system will automatically send an alarm signal.
3 electrical control circuit design
Liquid filling machine set with five circuit breakers, through the circuit breaker leads to the three-phase power supply, and play the role of short-circuit protection. In addition, there are three thermal relays, the motor to play a protective role to prevent overload damage to the motor.
The filling electrical control system is set up in two modes of operation, i.e. white motion and manual. In the automatic mode, after starting the system, the motor automatically starts to run to drive the conveyor running work, until the stop switch is activated then the motor stops running. Alternatively, when the weighing module detects that a bottle has stopped on the production line and is in the filling state, the conveyor stops running, and the conveyor automatically resumes running after the bottle has been filled until the next stop signal is received, and so on. In manual operation mode, the system is controlled by a switch, the switch is turned on, the system starts, the bottle reaches the filling position and the system stops. When the start switch is released and the filling switch is pressed, the filling action is initiated and the timer starts to work to control the time of filling and the filling stops when the time is reached. Pressing the system start switch here, the system turns on the operation mode.
The system is equipped with an alarm device, when the system malfunctions or there are abnormalities will be sent to the PLC fault signal, PLC start the alarm program by the alarm device in the form of sound and light alarm signals.
4 Conclusion
PLC-based filling production line control system is a fusion of automatic control machinery, sensing technology and other multidisciplinary, multi-technology comprehensive system, involving a wide range of superior performance, with a certain degree of complexity.PLC weighing and filling machine, including the design of the process, the configuration of the production equipment, the selection of weighing and control instrumentation, the design of control commands, the design of the control program, the PLC software configuration and hardware configuration, etc., high technology content. PLC filling system application, for enterprises to improve production efficiency, ensure production quality, reduce the labor intensity of workers. The application of PLC filling system for enterprises to improve production efficiency, ensure production quality, reduce the labor intensity of workers, enhance the comprehensive strength of enterprises have an important role in promoting the development of the mainstream direction of the field of modern industrial processing.