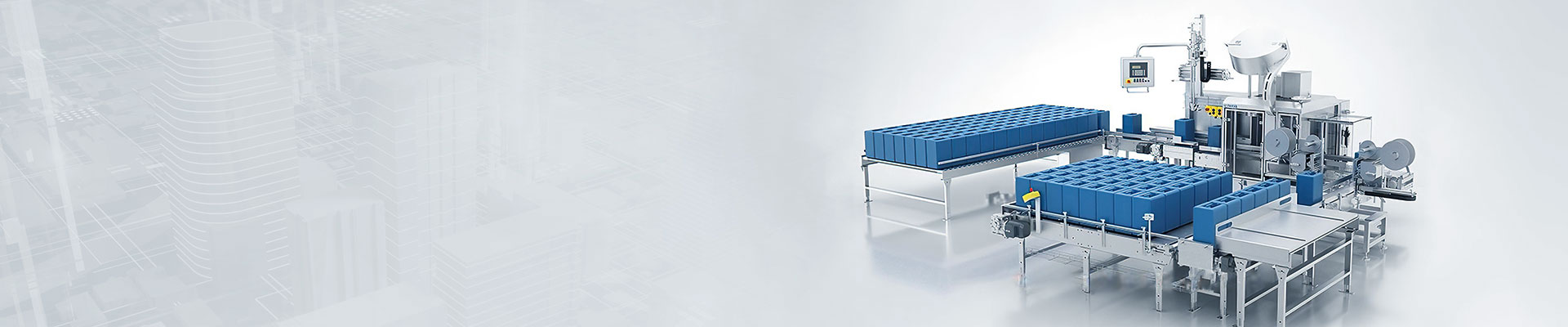
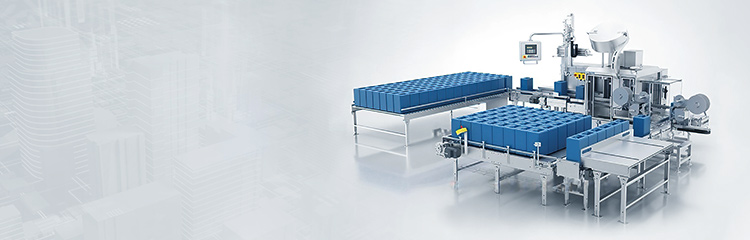
The cleaning solution filling machine realizes monitoring and control functions by operating on real-time data. Provides a real-time database that helps monitor the production process. The equipment screen with real-time updated data display also provides a large screen showing the entire operation process, making it easy to observe the entire production process. Data displayed includes operation mode, weight, totalized amount, set point, deviation, and other similar data.

Automatic Filling machine is mainly used for filling low viscosity liquid, using the method of controlling the liquid level quantitatively to fill liquid materials into rigid (such as glass bottles) or semi-rigid (such as plastic bottles) containers in the production equipment. It is mainly composed of machine frame, weighing and conveying table, positioning mechanism, Filling system, linkage compactor, liquid storage tank and control box.
The automatic filling machine achieves the control of filling quantity by utilizing the method of controlling the liquid level height Electronic scale metering in the bottle. The control level quantitative method is not only simple but also reliable, and is widely used in filling equipment. The liquid level position of the control level dosing method is mainly realized by controlling the height of the liquid return port of the liquid return pipe. The height of the liquid return port of the liquid return pipe can be adjusted according to the needs of the filling volume after calculation, in order to meet the needs of filling various sizes of bottles.
Main working procedure and working principle: the conveyor belt on the feeding table conveys empty bottles at a speed of 1,2m/s, when the first empty bottle is about to arrive at the predetermined position, the front bottle stopper rod of the positioning mechanism pops up under the control of the front photoelectric head, blocking the empty bottles so that the first empty bottle of each batch is in the accurate designated position; the rear photoelectric head counts the set batch quantity; the rear bottle stopper rod serves as an isolation rod between the batch and the batch to ensure the number of empty bottles (between front bottle stopper rod and rear bottle stopper rod) to be filled for the set batch quantity in each batch. The number of empty bottles (between the front stopper bar and the rear stopper bar) in each batch is the set batch number.
When the rear bottle stopper is extended, the conveyor belt stops conveying to avoid the friction between the bottom of the stationary bottle and the moving conveyor belt surface during filling, to prevent unnecessary wear and tear of the bottom of the bottle, and at the same time to ensure the stability of the bottle, which is conducive to filling. After the conveyor belt stops, the liquid filling system will be eight liquid nozzles at the same time one-time inserted into eight empty bottles and rely on the spring pressure and expandability and eight bottles at the same time compression sealing, the spring's expandability can effectively compensate for the eight bottles free height of the error caused by the improvement of Liquid filling machine to improve the sealing of a variety of bottles to improve the adaptability of the bottle filling machine.
At this time, the diaphragm pump starts, began to fill liquid to eight empty bottles at the same time, with the rising height of the liquid surface, the bottle air discharged through the return pipe, to be set to control the height of the liquid level (filling volume), the return pipe began to contact with the liquid surface and began to return to the liquid. Higher than the liquid return pipe mouth of the liquid return to the liquid storage tank to ensure that the liquid level in the empty bottle is always the set value, when the batch of eight empty bottles are filled, reaching the set control level height, the diaphragm pump automatically stops running, the filling system stops to empty bottles filled with liquid, adjusting the seat frame rises, while lifting up the eight liquid nozzle, so that the liquid nozzle and the filling of a full batch of bottles completely out of contact with the conveyor belt to open the The conveyor belt starts to send out the bottles filled with liquid, and at the same time, the next batch of empty bottles is transported to be filled, so that the filling machine completes a cycle of action.
Basic parameters:
Maximum weighing capacity: 30kg.
Minimum Sensitivity: 5g.
Filling range: 10-30kg.
Filling precision: ≤0.1%.
Filling speed: 200-500 cans/hour.
Container specification: ≤φ300×h350.
Gun head material: SUS304/316.
Power supply: AC220/50Hz.
Using gas source: 0.5Mpa.