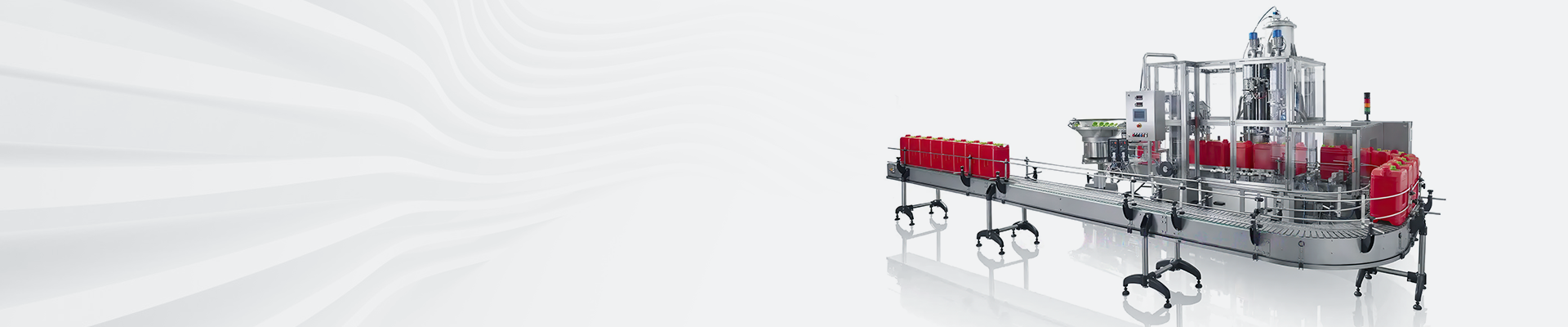
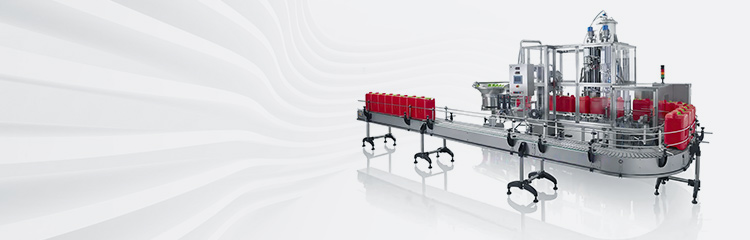
摘要:全自动灌装机能完成称量、混合、输送、贮存等环节的自动化生产线,将称重的实际值反馈给PLC,由PLC运算(补充填量=目标重量-预充填称重实际值)给出需要补充填的量。
全球经济的多元化发展,无论是国内市场还是国际市场,竞争都非常激烈,企业要做大做强,要实现持续稳定的发展,就必须开拓创新,积极引进新技术、新设备,进一步提高生产效率,保证产品质量,提高自身的综合实力。对于机械加工企业而言,机械化、自动化生产线的引进和应用,取代了原有的晶体管逻辑控制系统,不仅自动化程度高,而且性能优越,精度高,可控性好,是现代企业生产的必需。集成电路和微处理器的发展和应用,一种可编程逻辑控制器(简称PLC)应运而生,并在工业、机械领域的自动化控制场合率先加以应用,这也是工业自动控制生产线的发展趋势。在市场竞争日益激烈的经济形势下,企业引进并应用具有高精度的自动化控制生产线,是提高市场竞争力的必要手段。
自动灌装机的控制要求和控制方法
1控制要求
(1)操作模式设置为自动化操作,打开开关选择“自动”,驱动电机运转,驱动传送带运行,当称重传感器检测到瓶子到达指定位置呈停止状态时,传送带停止运行或者是停止开关启动,传送带停止运行。瓶子注满液体后,系统自动启动电机,电机再次发生驱动作用,直到到达另一个停止状态后再次停止,此动作循环进行。
(2)灌装系统上设置定位开关,当瓶子到达指定位置时,传送带运行暂停,称重灌装机随后开始进行灌装工作,在5S内灌装完毕。在此期间如果发生异常或者错误,系统会以声光的模式发出报警信号。
(3)设置有两个传感器和加法器,用于对瓶子的状态进行检测,同时对已注满的瓶子和空瓶子的数量分别加以记录,计数从系统运行开始,一般100万瓶为一个量程。
(4)系统复位和数据清零采取手动的方式,以防止自动清零造成的数据丢失或者系统误操作。
2各个环节的电气控制
(1)计数:设置计数器装置,对瓶子数量进行计算并记录,将计数器连接PLC,通过触摸屏控制对计数量程进行设置和显示。
(2)灌装:生产线上设置有前、后两个挡瓶阀。前挡瓶阀检测到空瓶经过,会发生自动挡瓶动作,同时后挡瓶阀也启动挡瓶动作,灌装设备开始进行灌注操作。灌装口由电磁阀和流量计对其加以控制以保证灌注量动作的准确和灌装量的一致性。电磁阀和流量计都由PLC来进行控制。
(3)压盖:在压盖机上配置有专门的传感器,用以对瓶子是否到位进行检测,当瓶子到达指定位置时,PLC发出指令控制压盖机发生压盖动作。压盖完毕后挡瓶阀收起,传送带传送瓶子至下一个T序点位。
(4)贴标:生产线上装置有专门的贴标机,对传送带传递过来的瓶子进行自动感应,当瓶子到达定位点时,贴标机启动贴标动作完成对瓶子的自动贴标。
(5)喷码:生产线上自动喷码机能感应到瓶子进行自动喷码操作。
在整个灌装生产线上,通过伺服系统来对电机的运行和停止进行控制,以此来保证整个灌装过程中瓶子的运动精度。自动填充机采用触摸屏式的人机交换系统进行控制,当生产线的运行发生异常或者故障时,系统会自动发出报警信号。
3电气控制电路设计
液体灌装机设置有五个断路器,通过断路器引人三相电源,并起到短路保护的作用。另外设置有三个热继电器,对电机起到保护作用,防止过载对电机的损坏。
灌装电气控制系统设置两种操作模式,即白动和手动。在自动模式下,启动系统后,电机自动启动运行驱动传送带的运行工作,直至停止开关启动则电机停止运行。或者当称量模块检测到生产线上有瓶子发生停止处于灌装状态,则传送带停止运行,瓶子灌注完毕后传送带自动恢复运行,直到受到下一个停止信号前,以此循环。在手动操作模式下,由开关控制系统,开启开关,系统启动,瓶子到达灌注位置,系统停止。松开启动开关,按下灌注开关,则开启灌注动作,同时计时器开始工作,对灌注的时间进行控制,到达时间后灌注停止。在此按下系统启动开关,系统开启运行模式。
系统设有报警装置,当系统发生故障或者有异常情况会向PLC发出故障信号,PLC启动报警程序由报警装置以声光的形式发出报警信号。
4结论
基于PLC的灌装生产线控制系统是融合了自动控制机械、传感技术等多学科、多项技术的综合性系统,涉及范围广泛,性能优越,具有一定的复杂性。PLC称重灌装机包括工艺流程的设计、生产设备的配置、称重控制仪表的选择、控制指令的设计、控制程序的设计、PLC软件的配置和硬件的配置等,技术含量高,对相关的配置都有一定的标准要求,满足现代企业生产实现一体化控制的要求。PLC填充系统的应用,对于企业提高生产效率.保证生产质量,降低工人劳动强度,提升企业综合实力都具有重要的推动作用,也是现代工业加工领域发展的主流方向。