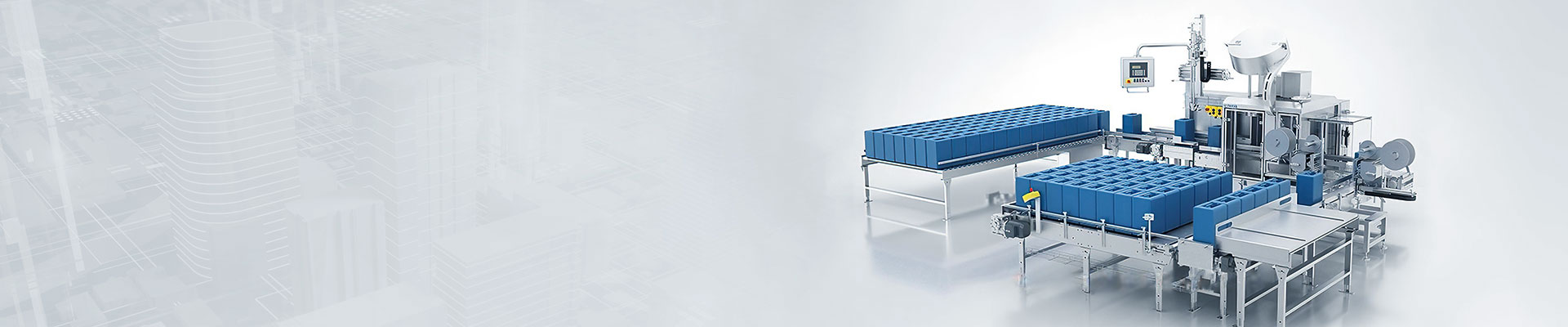
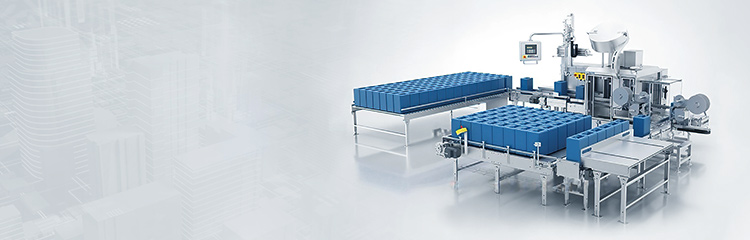
Disinfectant water filling machine has fast and effective product conversion and fast and automatic in-situ cleaning procedure with sealing device and unique self-discharge filling. The material filling can be effectively controlled in real time, realizing real-time detection of filling weight and real-time opening and closing of solenoid valve in the filling process, and data uploading for effective microcomputerized management.

Automatic Filling machine to realize filling by a certain proportion of the full automation and intelligence, the upper computer to send the formula filling weight instructions, Filling system using industrial mechanisms with communication board, can provide RS422 communication port and RS232 communication port, communication port were connected to the upper computer. The communication protocol adopts the query scanning method. Text communication content FCSe / machine number command prefix completion code check code completion code is a binary decimal number related to the programmable logic controller response to the commands sent by the host computer, which greatly improves the reliability of the system data transmission.
Automatic filling machine according to the production task for a variety of initialization and the formation of the recipe, the recipe includes the name of each component, quantity, production, standard ratio, standard weight, etc., and then send the parameters to the weighing instrument and programmable controller, in accordance with a certain time sequence to control, weighing instrument and conveyor trolley startup, read the weight signal of the liquid filling scales and cumulative, according to the cumulative value of the components of the calculation of the actual ratio, and the actual ratio with the standard to correct the amount of each regulator to give the system the best ratio. The actual ratio is calculated according to the cumulative value of each component, and the comparison of the actual ratio with the standard ratio corrects the feeding quantity of each regulator, so that the system works in the best ratio state. When the preset output is reached, the filling speed control curve stops according to a certain time sequence.
Basic parameters:
Maximum weighing capacity: 30kg
Minimum Sensitivity: 0.01kg
Filling error: ±0.01-0.02kg
Filling speed: 20L about 150-180 barrels/hour
Control mode: 2-speed control
Filling method: Insertion, liquid level up
Gun head line: Teflon gun head, valve + Teflon hose
Structure material: host SUS304 stainless steel, conveying palletizing carbon steel anticorrosion paint.
Weighing platform size: 400 × 800mm (304 stainless steel power raceway)
Empty barrel raceway: 400mm × 2500mm (304 stainless steel power raceway) with another 1200mm slope without power roller
Heavy drum raceway: 400mm×2500mm (304 stainless steel power raceway, 2 sets)
Separate barrel device: for 20L barrels, carbon steel anticorrosive paint structure, 304 stainless steel raceway.
Palletizing equipment: pan-transfer type, suitable for pallets 1200×1200×140mm, including supplying pallets, palletizing, and lower pallet conveying.
Pipe pressure: 0.2-0.6MPa (related to material properties).
Material interface: DN40 flange connector 4, according to the user to provide interface standards
Air Connection: User supplied 12mm air hose connector for quick coupling connection
Power supply: AC220/50Hz (user-supplied to one side of the machine)
Using air source: 0.4-0.8Mpa (provided by the user to the side of the machine)
Use temperature: -10℃-50℃
Base conditions: solid concrete floor of the assistant suspension agent flat, concrete thickness should be more than 10cm.
Optional models: standard, explosion-proof filling