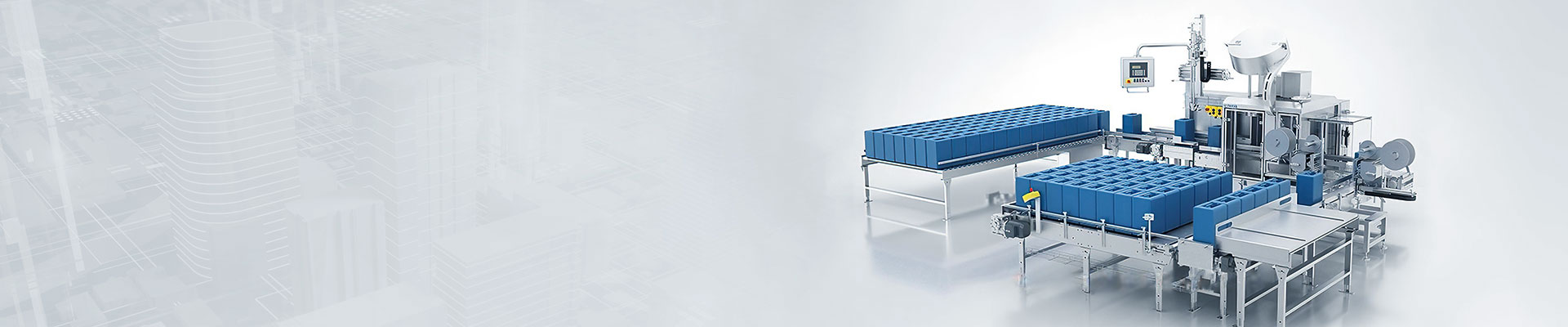
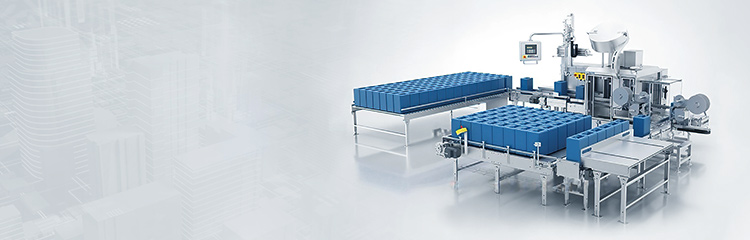
Automatic filling machine adopts WIN7 system platform, serves the software of automatic process control, uses computer identification technology, printing technology, automatic control technology, information technology to form intelligent filling, to meet the requirements of filling process automation, information and intelligence.

Weighing and Filling machine using WIN7 system platform, serving in the automatic process control software, the use of computer identification technology, printing technology, automatic control technology, information technology, the formation of intelligent filling, the use of weighing sensor platform under the control of microcomputer program set, integrated machine, electrical, instrument new machine, the ideal filling equipment integration of weighing and filling. When filling, the tare is removed first, the operator only needs to put the container into the platform, the barrel mouth is aligned with the filling nozzle, at this time the program starts, the filling valve is opened to feed, the filling head automatically dives into the bottom of the barrel, and the material is injected into the container by a large amount of rapid filling and then a slow and small dose correction measurement, when the set amount is reached, the filling is automatically stopped, the filling nozzle rises, and the filling process is completed. This submersible weighing filling is specially used for weighing and quantitative filling of various foam liquids.
The basic structure of the automatic filling machine is composed of five parts: cleaning link, filling link, capping link, packaging link and testing link. The cleaning process is to clean the recovered beverage bottles, first inject special cleaning solution into the empty bottle, clean and disinfect the bottle, and then pour out the cleaning solution through the bottle pouring machine, and then send the cleaned empty bottle through the conveyor belt to the filling link. In the filling process, the PLC controls the solenoid valve to conduct the air pressure so as to control the air pressure valve to fill the bottle. When the liquid level reaches the standard, the air pressure valve stops filling. The filling port puts the filled bottle down. The bottle is then transported to the next stage by a conveyor belt. Capping link fixed frame puts the bottle cap on the bottle mouth so that the screw thread of the bottle cap coincides with the screw thread of the bottle mouth. The bottle is rotated through the friction chain of the conveyor belt to measure the wall, and the bottle cap is tightened to achieve capping. The packaging link is composed of two shafts that hold the wrapping paper in place, and the wrapping tape binds one end to the side wall of the bottle when it is delivered to the packaging location. Then rotate the bottle and let the wrapping paper wrap around the bottle for a week. After the wrapping paper is cut off, the other end of the wrapping paper is fixed and glued to the bonding place. The packaging link is over. After the final processing of the product through the detection process of poor sensor detection, including external damage to the bottle, bottle cap packaging, poor packaging, filling level, etc., finally the robot will move the unqualified products to the designated area, qualified products are packed so that the entire processing process to end the control requirements.