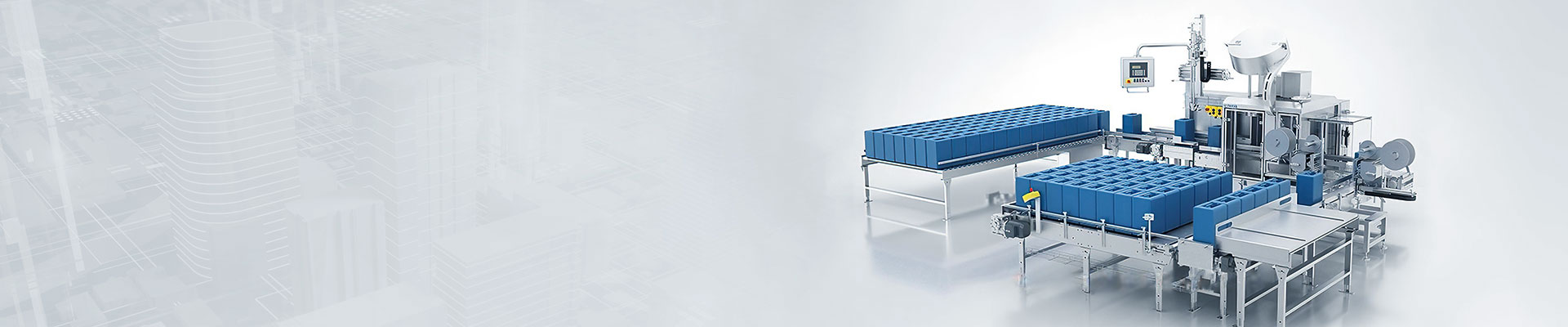
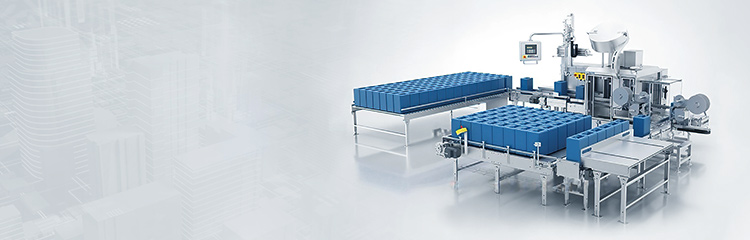
The weighing and filling line picks up the weight through the pressure weighing module, and amplifies and filters the picked up weight signal, then enters into the A/D converter for analog-to-digital conversion, and then sends it into the microcontroller to analyze and process the signal, and the result is outputted to the industrial control through the serial port of RS232C communication, and meanwhile, it makes the corresponding reaction and executes the corresponding operation according to the result of the signal.

Liquid Filling machine dive filling to prevent material foaming, material contact part is made of 316L stainless steel, corrosion resistance. Double-speed filling first fast and then slow, that ensures the speed and accuracy. When the filling is completed, the cap is screwed and sealed, and then labeled and coded. Labeling machine front section of the barrel device. This is a full-automatic single side labeling machine, with high precision labeling, labeling neatly without wrinkles, labeling firmly, not fall off. This is the whole automatic liquid filling production line operation.
The weighing and filling line adopts the FX3U series programmable controller of Mitsubishi Corporation. In order to ensure the accuracy and reliability of the action of each part of the device in the filling process, the weighing and filling machine is controlled by the PLC program for each sensor, relay, switch and solenoid valve. After the filling barrel is placed on the conveyor belt, it is transferred to the filling position by the conveyor, the proximity switch arranged at the filling position automatically senses and transmits the sensing signal to the PLC control system, the PLC controls the conveyor motor to stop rotating, and at the same time, it controls the lifting cylinder to drive the roller arm to rise and move the filling barrel to the position of the filling gun of the filler machine, and the photo-electricity sensor at the port of the filling gun automatically senses the position of the filling barrel, while the The cap suction device starts to suck the cap away; then the filling gun starts to fill the liquid into the filling barrel, and the weighing module transmits the weight signal of the liquid in the barrel to the PLC control system. When the predetermined weight is reached, the PLC controls the filling gun to stop filling, the cap suction device automatically seals the cap, and the conveyor motor is started to transport the filling barrel away.
Main parameters
Weighing range/(kg)/0.5-5/2-10/5-30/10-50/
Weighing speed (times/hour)/160-240
Accuracy class/0.25
Allowable Tolerance/±0.2%
Equipped with power supply/AC220V/50Hz±2Hz
Equipped with gas source/flow rate 0.1m3/min pressure 0.4~0.6MPa
Working temperature/0℃~40℃
Conveyor raceway/conveyor distance/1300mm
Capping machine/capping size/customization
Overall dimensions / based on the supplied outline drawing