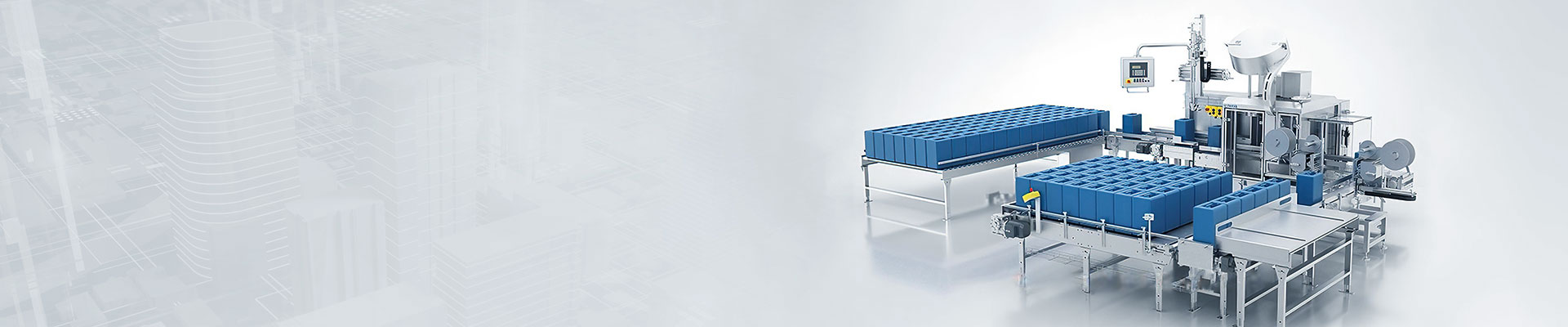
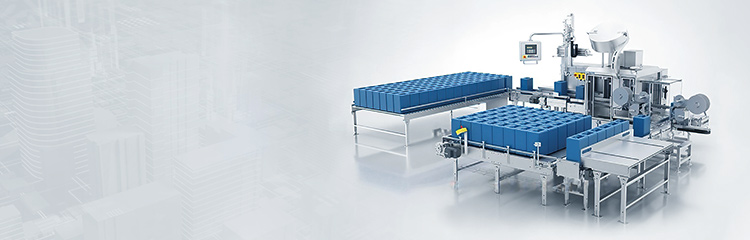
The Chinese herbal medicine feeding machine is composed of weighing and feeding machine, intelligent cache equipment, lifting conveyor, pre-feeding cache equipment, flipping feed scale, cleaning machine, information bar code tracking system and computer information system, which realizes the functions of silo conveying, feeding, weighing, caching, feeding and cleaning. The system can realize pre-treatment receiving, weighing, information input, online caching, feeding grouping, lifting and conveying, caching before feeding, turning feeding and dust removal, information verification, empty warehouse return, cleaning and washing slag, drying and discharging slag.

The Chinese herbal medicine Feeding machine is composed of weighing and feeding machine, intelligent cache equipment, lifting conveyor, pre-feeding cache equipment, flipping feed scale, cleaning machine, information bar code tracking system and computer information system, which realizes the functions of silo conveying, feeding, weighing, caching, feeding and cleaning. The system can realize pre-treatment receiving, weighing, information input, online caching, feeding grouping, lifting and conveying, caching before feeding, turning feeding and dust removal, information verification, empty warehouse return, cleaning and washing slag, drying and discharging slag. Through the system cooperation, to achieve accurate control of each production link, complete product formula management. Develop servo system and electronic label information tracking system to realize binding, tracking and feedback of basic information, and realize real-time collection, binding, tracking and feedback of basic information such as Chinese herbal medicine name, batch number and production date, visualization of process monitoring and parameterization of production process.
Online automatic precision weighing, feeding function
According to the different production process parameters set by different material production processes (variety formula, prescription amount), the material is received through the turnover bin, the turnover bin loaded with medicinal materials is automatically weighed and weighed on the conveying platform, the weight deviation is controlled within 3%o, each turnover container is equipped with RFID card, each RFID content is the turnover container number and material information. The turnover box number is unique. After the material received by the silo is weighed and reviewed, it is transported by shuttle to the storage space for material temporary storage. The pre-treated materials are transported into the cache tank. When the weighing module of the Weighing system detects that there is a lot of missing materials, the climbing belt and the horizontal belt are rapidly fed at the same speed in order to ensure feeding efficiency. When the weighing module of the weighing system detects that the weight of materials in the material tank (circulating material tank) is close to the set weight value, the climbing belt and the horizontal belt decelerate. In order to evenly distribute the material on the horizontal belt and ensure feeding accuracy, the climbing belt and the horizontal belt will use different transfer speeds. Use the speed difference to achieve precise feeding.
Intelligent cache function
There are a variety of material ratios in the cache part of the hopper scale, which can automatically manage the cache information through the computer information management system, and can prompt or display the storage location of the bunker according to demand. In the material intelligent cache device, the core device is the cargo fork intelligent shuttle, which works with the intelligent cache scheduling system to complete the storage and removal of materials. The shuttle conveyor is composed of shuttle bicycle, shuttle control system, shuttle power supply sliding line system, shuttle running double track system and other auxiliary equipment. The shuttle car is equipped with a detection and interlocking device to ensure safe operation, and for the first time, the bidirectional fork of the stacker machine is applied to the shuttle car, and the shuttle car and the roller line or the chain machine are used together to achieve the logistics conveying function, the movement rhythm is fast, there is no need to adjust the direction in advance, as long as the program can be programmed according to the logic relationship to achieve automatic caching to both sides. The mechanism is simple in structure, completely eliminating the rotating parts, and realizes the two functions of adjusting the direction and moving out through the fork, which reduces the complexity of the mechanism and also reduces the risk of error of the mechanism. The precision is high, and the positioning accuracy in the cache process is fully guaranteed, and the left and right are completely symmetric, which also ensures the symmetric accuracy of the cache on both sides.
Lifting conveyor
The main job of lifting the conveying equipment is to transport the materials stored in the material intelligent cache device to the cache device before feeding. The elevator uses the up and down reciprocating movement of the lifting platform to achieve the vertical conveying of materials. Different kinds of conveying equipment can be installed on the lifting platform, and it can be matched with the inlet and outlet conveying equipment to achieve complete automation of the conveying process. The upper and lower stroke of the lifting platform can transport materials, and the materials can flow to both sides at the same time in a cycle process of the lifting platform. The lifting stroke range is large, and the throughput decreases with the increase of the stroke. The lifting platform is connected with the main frame by the lifting chain, and is guided by the roller and guide rail, and the other end of the lifting chain is connected with the balance weight block. Roller conveyors or chain conveyors can be installed on the lifting platform. The reciprocating elevator has various forms and flexible layout, and the materials can enter and exit the elevator from all directions, which is convenient for the layout of production equipment; Large bearing range, can be set up a variety of safety devices, improve the safety of equipment operation, suitable for vertical transportation of various industries.
Cache device before feeding
The pre-feeding cache device is mainly used to cache the materials that need to be fed. The roller conveyor is one of the main equipment for palletized goods to enter and leave the automated three-dimensional warehouse with the stacker. It relies on the chain to transfer torque and drives the roller to continuously transport materials. It has the advantages of low noise, smooth transportation, large load bearing, excellent performance and beautiful appearance. The roller conveyor is mainly composed of frame roller table components, legs, driving frame, chain, protective cover and other connecting parts. The motor drives the chain to pull the driving roller, and the driving roller adopts cascade transmission to drive other rollers to the handling machinery transporting materials. The roller assembly of the frame is composed of the frame and the roller, the roller shaft and the frame are connected by bolts, and the two ends of the roller shaft are provided with internal threaded holes, and the rigidity of the frame is enhanced by the connection of the roller shaft with the two frames. The number of legs depends on the length and load weight of the roller conveyor. Roller drive is driven by the motor sprocket through the chain on the 2 rollers, each roller is arranged according to a certain distance, each roller has a double row of sprockets, and then by the 2 rollers a ring set a ring drive the rest of the roller, the continuous operation of each drive roller drives the unit load forward. The motor is centered on the drive frame, and the motor chain is tensioned by bolts on the drive frame and placed on the inside or outside according to the conveyor layout and space size. The driving device is driven by SEW motor reducer chain.
Intelligent feeding machine
The flip feeding system is used to drop the cache part of the material before feeding into the corresponding feeding port. Its main body is a gantry truss structure, that is, a five-axis gantry manipulator. The specific implementation method is as follows: The five-axis gantry manipulator is used to realize the two-side flip feeding required by the process, and the positioning of different feeding ports, hopper and air feed hopper is realized through X, Y and Z axes, and the flip feeding process is realized through clamping and rotation. The conveying, lifting and rotating of the hopper are all driven by Lentz motor, in which the conveying, lifting and rotating are controlled by servo frequency conversion to fully ensure the accuracy of each part. The whole feeding process is intelligent and automatic, the rotation is driven by servo motor, the rotation speed and rotation Angle can be automatically controlled, and the appropriate adjustment can be automatically made according to different medicinal materials to meet the requirements of different materials delivery.
Cleaning machine
With the continuous expansion of the scale of enterprises in the pharmaceutical industry and the popularity of automatic upgrading mixers, container (silo, etc.) cleaning has become an important bad part in the production of solid preparations, which makes pharmaceutical companies put forward higher requirements for the efficiency and quality of container (silo, etc.) cleaning. The fully automatic container washing and drying machine can thoroughly clean and dry the inside and outside of the container, which fully meets the GMP requirements of pharmaceutical production. The machine adopts the principle of high pressure and high temperature cleaning, through the high pressure pump in the pipeline to lift the pressure of the cleaning medium, and then by the nozzle of each part of the high-pressure liquid droplets, the inside and outside of the container thoroughly clean ten, and then use the room temperature clean air shower, the liquid droplets on the wall of the container, and then dry with 50℃ clean air, and finally cool the container to room temperature clean air. When working, just place the container needed to be cleaned in the box of the washing machine and start the automatic cleaning procedure to complete the cleaning, drying and cooling of the container.
Information bar code tracking system
The information bar code tracking system is adopted to implement intelligent management of product information binding, tracking, classification, storage and storage. The material information is tracked in the whole process, and each turnover container is equipped with a unique identification bar code, the bar code content is the turnover container number and material information, which can record and read the product name, batch number, production date, status, weight, etc. By scanning different barcodes of different items at different locations, the information on the barcodes can be passed to the system to implement item information tracking. Through the automatic control and process monitoring of turnover container inter-process transfer, the monitoring display can be visualized and the production process control can be parameterized. And reduce the human information error, improve the stability of product quality, and provide data support for the realization of the whole process of production management information traceability.