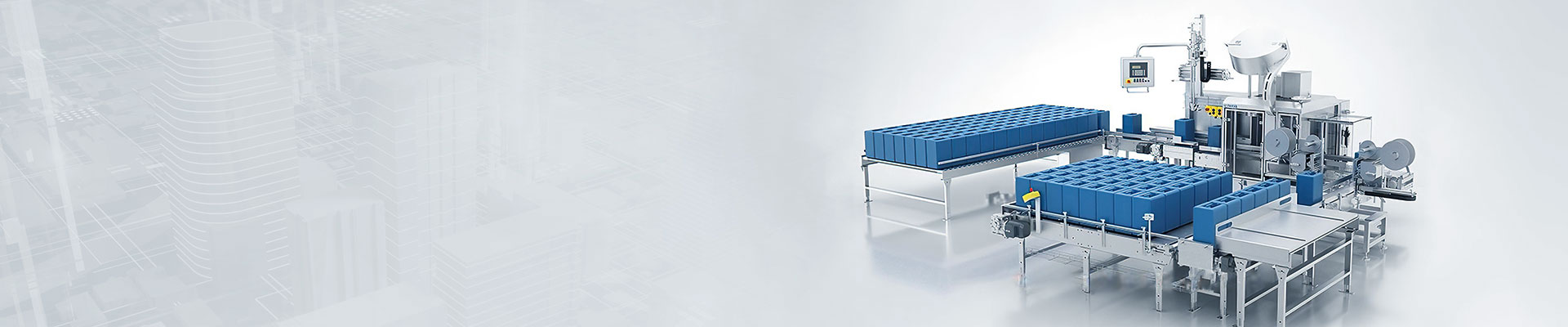
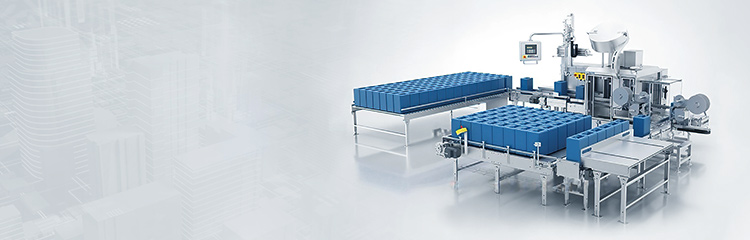
The auxiliary filling machine is composed of a filling gun, a filling barrel, a synchronous motor, a rodless cylinder and a roller arm. The conveyor belt is transmitted through the transmission gear, and the barrel is sent to the specified position. The sensors, relays, switches and solenoid valves are controlled by PLC program. Fill the material input weighing, and record, to achieve the management of material feeding.

Automatic Filling machine using Electronic scale PLC programming control touch screen operation control, A/D chip and anti-vibration technology, interlocking control of various operating processes. An independent cylinder controlled residual drop collection tank is installed below the filling head, with adjustable variable speed filling function. The core part of the weighing control system is Siemens 57-200 PLC. Kingview developed monitoring system software PLC, which is responsible for collecting input signals, realizing the frequency converter to control the spiral speed and adjust the filling weight. By measuring the instantaneous flow rate, the frequency converter can adjust the spiral speed and adjust the feeding quantity equal to the set value to complete the automatic filling process.
The automatic filling machine uses weighing control to start the feed pump of raw materials until the qualified material weight is sent to the filling barrel, which will include the control and interlock of all feed and discharge valves, the start and stop of each feed pump, the control of fast and slow feeding, the status detection, and all data processing functions. It is composed of weighing unit, data processing unit and logic control unit, which work independently of each other and are closely connected by question and answer. Flexible and mobile, while improving the degree of automation, but also improve the reliability of filling, to ensure that users can long-term trouble-free operation.
The core unit of automatic control is PLC, which is composed of interface and other actuator. The initial screen, equipment status aspect, user operation panel, alarm screen, and curve diagram for displaying real-time changes of reactor motor and liquid level are displayed when starting up. Set up material mixing display window, set up database variables and complete attribute definition. Through attribute definition, space, policy equal segment, complete the design of dynamic screen, set the storage attributes of data variables, establish data query and curve browsing. Establish the communication connection of external devices and set parameters to realize the function of transport monitoring and data management.