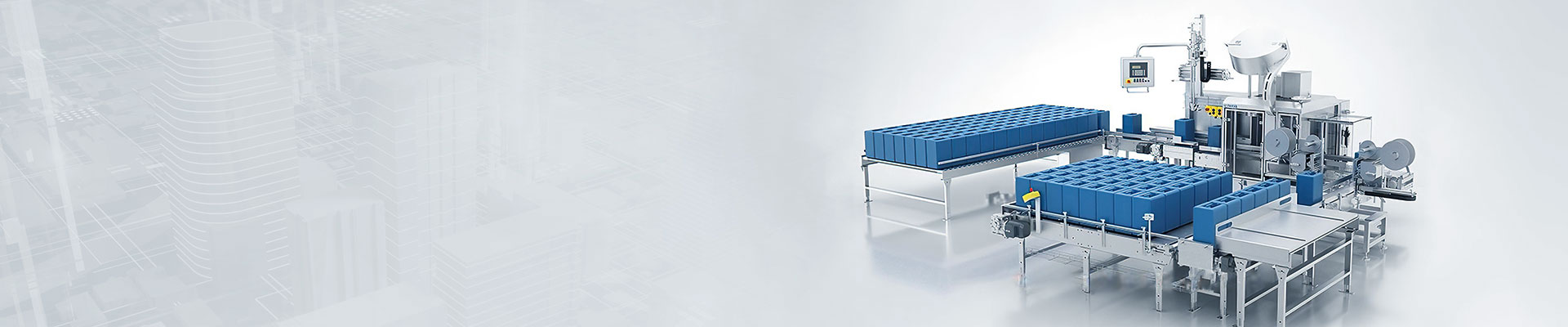
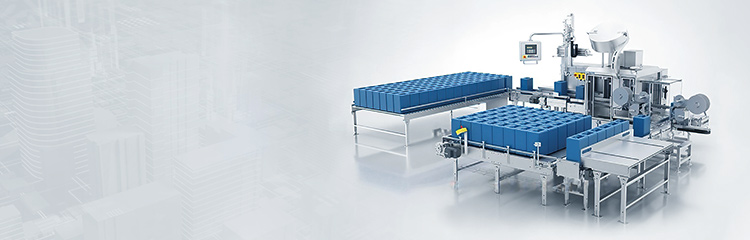
The weighing and feeding machine is composed of PLC, weighing control instrument, weighing module and reaction kettle. PLC is used to configure the start and stop and the opening and closing of the warehouse door, to detect the status of the warehouse door and operation configuration, and to implement the system interlock of the batching system.

The composition of the Feeder is based on the existing Batching system, combined with the expansion of the new system process equipment configuration automatic control scheme. The newly expanded raw material feeder includes two sets of systems, east and middle, each system has 2 powder silos, 4 sets of raw material constant volume feeder, 2 sets of weighing instruments; The control batching machine includes 2 industrial control machines, 1 set of PLC Feeding machine, 2 field operation boxes and the control device of batching scale. Among them, the industrial control machine mainly completes formula management and historical data query. The core of the feeding machine is composed of a set of SIEMENS S7-300 series PLC, which mainly completes: raw material supply and transportation control; Control of the material ratio of the formula; Communication and data exchange.
The dosing control of the feeder is based on the formula ratio and control requirements input by the operator, and is calculated by PLC in batches according to the preset kilograms of raw material ingredients. First set the high and low limits of the powder hopper, such as the high limit is set to 2500kg, the low limit is set to 500kg, and the ton/powder is 20kg, then input: (2500-500) / 20=100 in the "formula number" column. After logical calculation, PLC controls the action times and action intervals of the raw material blanking cylinder according to the actual measured value change of the Electronic scale during the process of hopper blanking, that is, the constant volume cylinder with a capacity of lkg operates once every 100kg powder. When the powder blanking speed is accelerated, the action interval time of the raw material blanking cylinder is shortened accordingly. Thus, the powder is evenly proportioned. When the actual material quantity of the hopper reaches the low limit, the PLC sends a signal to the hopper low material valve and the raw material blanking cylinder to stop the blanking, the batching is completed, and then the next assembly process is entered. The actual amount of powder hopper and the number of movements of the raw material discharging cylinder are displayed in real time on the remote terminal. The industrial control machine displays the current actual batching situation with text, dynamic graphics and figures on the CRT.