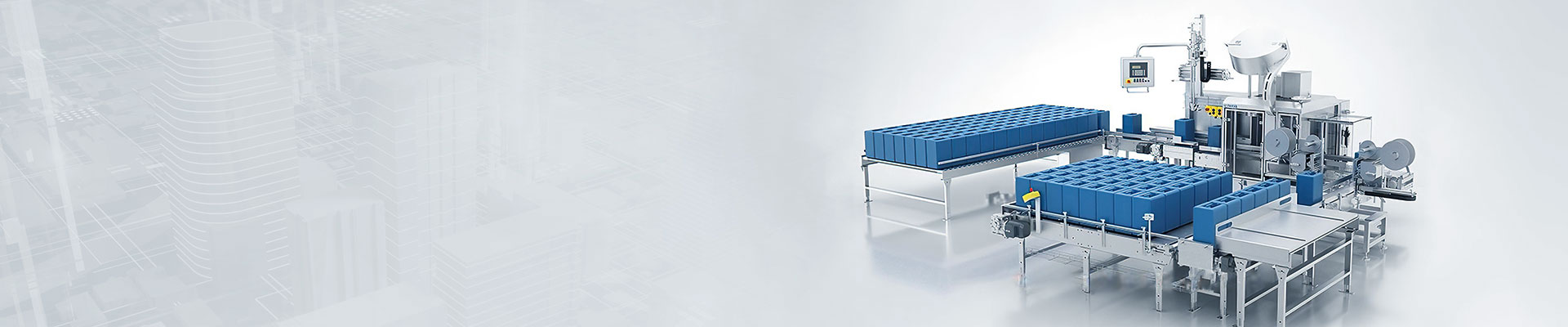
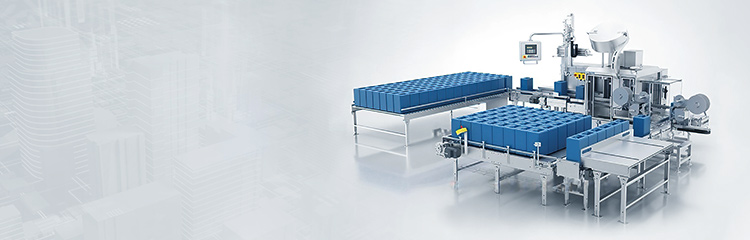
Liquid dispenser is a weighing system that integrates weight information collection, amplification, transformation, transmission, processing and display, and controls each sensor, relay, switch and solenoid valve through PLC program. It draws on advanced technology and techniques, and combines with its own long-accumulated experience to integrate inventory management, filling management, filling and weighing, process control, and product traceability into one.

Automatic Filling machine is a kind of mechanical equipment used for automatic filling of liquid, realizing automatic filling, sealing, conveying and other functions. It mainly consists of filling head, conveyor belt, control device and so on. The liquid is injected into the container by means of piston pump or peristaltic pump. The conveyor belt is used to send the empty containers to the filling position and transport the filled containers to the designated weighing position, which is capable of filling control equipment start, stop, speed and so on.
The weighing and distributing machine transforms into 4~20mA current as the input signal for system display and control through the weight transmitter. The current weight of the raw material barrel is taken as the starting weight setting value, and is set as the target dosing value through the display instrument or DCS system. When the weighing module detects that the weight in the canned barrel rises up to a certain value, at this time, the output current is basically in a linear relationship with the weight value, and in order to ensure the accuracy of each point, the liquid level signal of the filling barrel is taken as the control signal of the feeding valve for automatic adjustment of the liquid level parameters. In order to ensure the accuracy of each point, the liquid level signal of the filling barrel is used as the control signal of the feeding valve for the automatic adjustment of the liquid level parameter, so that the whole automatic filling machine realizes the automatic adjustment function of the continuous production process.
Basic parameters:
Maximum weighing capacity: 30kg
Minimum Sensitivity: 0.1kg
Filling error: ±0.1-0.2kg
Filling speed: 20L about 1500-1800 barrels/hour
Control mode: 2-speed control
Filling method: Insertion, liquid level up
Gun head line: Teflon gun head, valve + Teflon hose
Structure material: host SUS304 stainless steel, conveying palletizing carbon steel anticorrosion paint.
Weighing platform size: 400 × 800mm (304 stainless steel power raceway)
Empty barrel raceway: 400mm × 2500mm (304 stainless steel power raceway) with another 1200mm slope without power roller
Heavy drum raceway: 400mm×2500mm (304 stainless steel power raceway, 2 sets)
Separate barrel device: for 20L barrels, carbon steel anticorrosive paint structure, 304 stainless steel raceway.
Palletizing equipment: pan-transfer type, suitable for pallets 1200×1200×140mm, including supplying pallets, palletizing, and lower pallet conveying.
Pipe pressure: 0.2-0.6MPa (related to material properties).
Material interface: DN40 flange connector 4, according to the user to provide interface standards
Air Connection: User supplied 12mm air hose connector for quick coupling connection
Power supply: AC220/50Hz (user-supplied to one side of the machine)
Using air source: 0.4-0.8Mpa (provided by the user to the side of the machine)
Use temperature: -10℃-50℃
Base condition: Horizontal solid concrete floor, concrete thickness should be more than 10cm.
Optional models: standard, explosion-proof filling scale