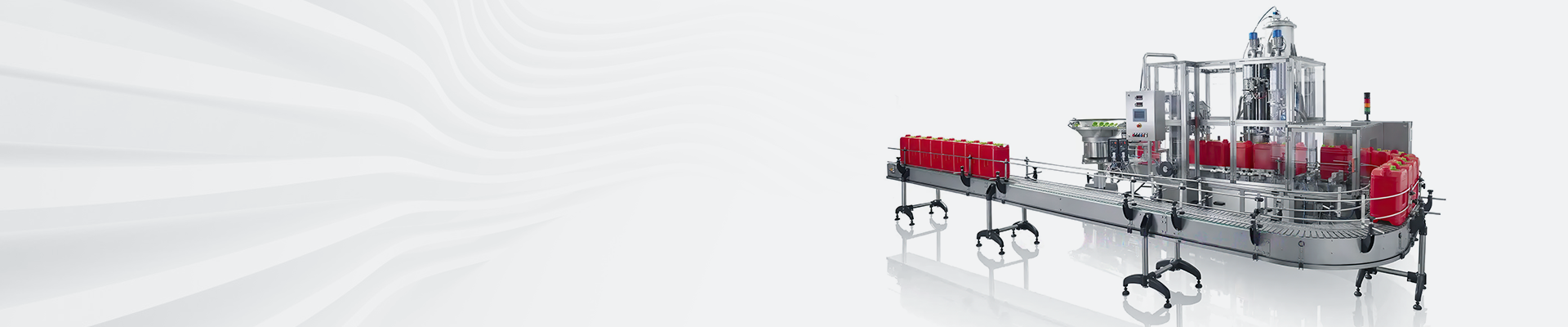
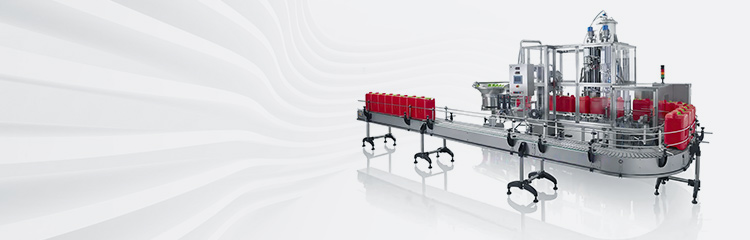

Summary:Automatic filling machine acquisition can turn the optical characteristics of the target object into an electrical signal of two-dimensional information through triggered acquisition or continuous acquisition, and then convert it into a digital image through the sampling and quantification functions of the data acquisition card or the acquisition device itself. Then perform computer processing.
Equipped with an automatic doser, the material will be filled directly into the transferred drum according to the pre-set standard and the quantity set by the filling nozzle. The whole process is accurate and fast, and will not cause material waste, not to mention environmental pollution. The filled barrels will be transferred to the next step through the power rail. The automatic filling machine consists of S7-200PLC and weighing instrument ICS241 and filling solenoid valve. PLC uses RS232C communication port to connect with the weighing instrument to collect and process the weight data through communication, as well as send tare signal to make the instrument tare. In the quantitative filling mode, the PLC receives the data from the weighing instrument as the main controller, processes the data and sends out a series of signals to control the action of the filling machine, so that the filling machine completes the quantitative filling. the PLC communicates with the weighing instrument through RS232C, and the communication between the two is a protocol-free communication, the parameters of the serial communication between the PLC and the weighing instrument need to be set in the same way. The PLC communicates with the weighing instrument through RS232C, the parameters of serial communication between PLC and weighing instrument should be set the same. The weighing instrument sends data continuously through RS232C, and the weighing instrument sends data continuously all the time to ensure that the data of serial port is synchronized with the data of the instrument.
Liquid filling machine mainly includes front weighing module, reweighing system, LMC series motion controller, LXM series servo drive and servo motor, and upper computer monitoring system. The servo motor is used to realize the rotor pump stroke control and then the filling volume control. Before filling, the front weighing module obtains the weight of empty barrel, after filling, the rear weighing module obtains the weight of filling and transmits it to the weighing instrument, the weighing instrument will externalize the filling data in real time to get the weight deviation, the filling algorithm calculates the control amount of large materials, the weighing system will send the control amount to the servo driver, drive the secondary rotor pump to execute the small amount of material to close in advance before controlling the small amount of material filling valves, and the upper computer connects with the weighing instrument through Ethernet to read the filling volume in real time, and then realize the control of small material filling. The upper computer is connected to the weighing instrument via Ethernet to read the filling data in real time, and the process parameters can be set to monitor the operation of the production line. After filling and capping, drive the gripping manipulator to accurately position to the designated unit, and grab the filling barrel on the material table to transport to the designated place and then put down. The servo motor drives the manipulator, utilizes the high-speed pulse output function of PLC, and realizes the accurate stacking control of the manipulator through PTO programming.
The main function of the weighing and filling machine is to fill the liquid medium into the packaging container to realize the functions of filling, sealing, weighing and stacking. Sequence control, motion control, communication, data management microprocessor technology and communication technology, filtering, judgment and storage of input signals, etc., the form of output signals transmitted to the actuator of the filling system to complete the filling command, real-time control of the barrel position in the online container, with pressure control on the filling barrel pre-pressure, the speed of the conveyor chain to regulate the speed of the conveyor link when the conveyor chain containers stacked blocked, but also need to coordinate Coordination of the feeding speed of each drag point of the whole production line. Coordination signal is to other conveyor chain drag in the production line, the control system also empty / full barrels in place, pile of blockage, under the lid, open / close the filling valve for real-time pick up and control. The use of PLC signals to drive motors and other transmission mechanisms to drive the manipulator to move, while driving the motor comes with the encoder feedback bit (pulse) to the drive driver to compare the two kinds of pulses and determine the deviation, according to a certain control law after the operation of the calibration signal obtained as a servo drive in the speed controller is given and then by the current regulation and power amplification, so that the gripping manipulator towards the elimination of the deviation of the direction of the movement, so as to Realize the stacking positioning of the manipulator.