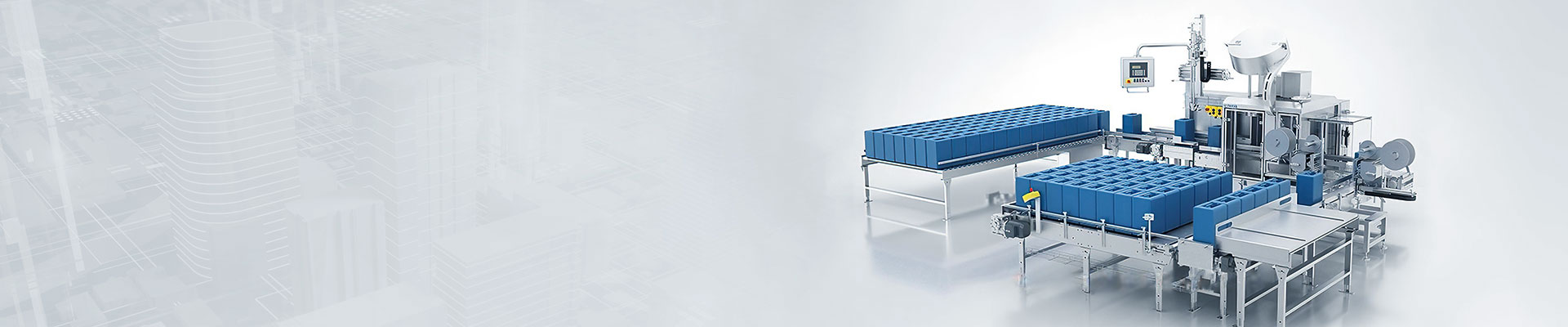
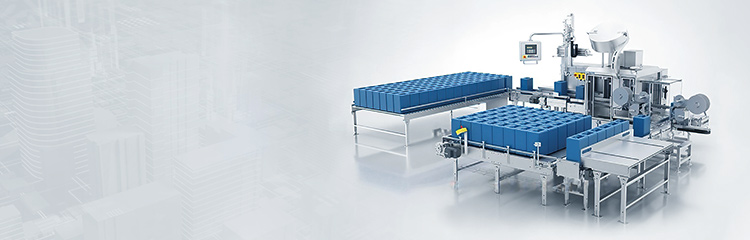
Automatic filling machine to realize the instrumentation and PLC and the host computer communication connection, real-time processing and the corresponding components of the formula for comparison of the settings. The use of RS485 bus type to realize the connection with the filling machine port, in order to achieve the instrumentation and PLC and the host computer running state is consistent, read through the interface stored in the filling machine touch screen, easy to fill management and query.

The automatic Filling machine adopts speed control instructions to cycle the movement in 360 cycles, and the pause function program needs to pause the equipment by simply executing the instructions. When starting again, just execute the instruction again, the equipment will continue to run from the current stop position. The advantage of the pause is that when the operator needs to temporarily stop the equipment, do a simple processing, and then need to quickly restore the production state, do not need to find the origin again.
Liquid filling machine according to the characteristics of the crank mechanism, when the servo rotates at a constant speed, you can give different speeds when the filling servo reaches each position, by giving the angular speed of "multi-stage speed" to achieve a basic constant vertical speed. The speed change is realized by writing the speed every 10ms. The linear relationship between the servo angular position and the vertical position of the crank is obtained through plane analytical geometry and trigonometric operations. In the end, the touch screen can be used to set the filling volume in "milliliters".
Changes in the cam table After the cam table has been prepared, each head will repeat the movement according to its own cam table data. If the product is changed (mainly because of a change in bottle size), the movement of the individual head has to be changed. By changing the program, the loop variable of the FOR loop statement, changing several points in the cam table in sequence through the FOR loop statement, and then saving it through the following instruction, the movement from the head will be carried out in accordance with the new cam table.
Technical Parameters
Filling speed: 180 cans/hour, 250 cans/hour
Feeding range: 4~20kg
Feeding accuracy: 1/500~±1/1000
Minimum display: 200g
Power supply: AC110/220V, 50/60H
Use of air pressure: 5kgf/c ㎡