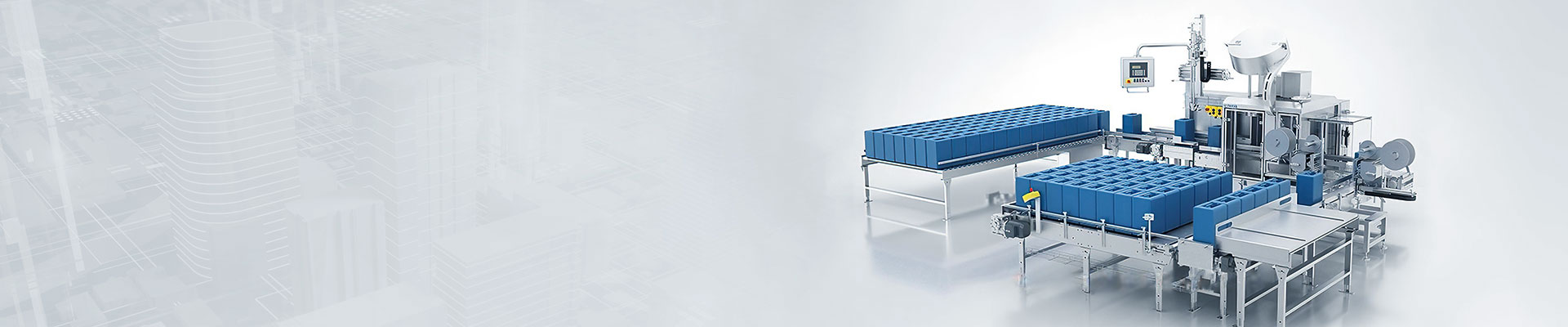
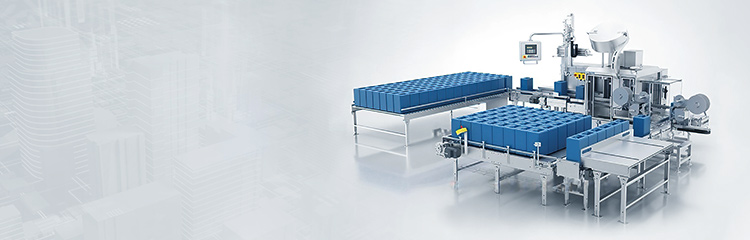
The vacuum mixer adopts a master-slave batching system with PLC as the main controller and industrial computer as the upper computer, which can meet various requirements of the system and overcome the disadvantages of the above two systems. Operators can input and modify the formula through the keyboard and CRT display, dynamically monitor the production process of batching, and print batching results and production reports in time, so as to realize scientific batching production automation and management. Information such as the weight of each material, the cumulative blanking amount and the given value of each material are displayed on CRT, and relevant database files are formed. When necessary, various management files and reports are printed out.

The vacuum mixer is an intelligent full-automatic and high-precision material (granular, powdery and flaky) metering and Batching system for rubber, plastic, food, feed, pharmaceutical and other industries; Adopt electromagnetic vibration, double (single) spiral feeding and other feeding methods and continuous stepless speed regulation intelligent control device, multiple Electronic scales are independently set and driven, and share automatic batching and mixing. The batching system consists of a set of PLC, touch screen and several accessories. And through 485 communication and computer into a network, providing a convenient platform for the company's unified management. The vacuum mixer is composed of several pneumatic/manual valves, etc. The automatic control part of the production line is controlled by a set of PLC and touch screen. The low material level signal of the storage tank, the alarm signal of the screw Feeder, the signal of the feed valve/discharge valve position, the starting signal of the mixer or the on-site manual feeding and discharging signal are connected to the input of the PLC, and the signal of the weighing module is input to the PLC through the 16-bit high-precision A/D conversion module of the PLC. Through programming, the PLC controls the whole batching weighing process, data processing and alarm output of the Weighing system. The data parameters and operation of batching are directly controlled by touch screen interface. The system is connected with the computer through the 485 communication module, and the computer monitors and processes the data.
principle of operation
Pneumatic batching is a concrete application of fluidization technology, which uses the energy of airflow to transport granular materials along the direction of airflow in a closed pipeline. Generally speaking, the capital cost of the system is low, and the clearance under the ash hopper is required to be minimum. Because the leakage only occurs inside the system, the operation is relatively clean. The pneumatic ash removal system is suitable for the pneumatic ash removal system of small and medium-sized thermal (fire) power plants (boilers with 200MW and below). When the dry ash conveying distance is equivalent to 300 meters in length and 90 meters in vertical height, and the system conveying capacity is less than 100t/h, the system has the best cost performance. The system belongs to low positive pressure dilute phase conveying system.
Dry ash enters the buffer bin and continuous delivery pump from the ash hopper of electrostatic precipitator (or bag filter) through the ash dropping pipe, and is transported to ash storage through the ash conveying pipe at a certain speed with Roots blower as the gas source (the pressure is below 98KPa). The gas separated from the feed gas is discharged into the atmosphere after passing through the bag filter. There are two ways of discharging dry ash in ash storage: dry discharging (automobile bulk loader) and wet discharging (humidifying mixer). Users can choose according to the use of fly ash.
technical parameter
The pneumatic system is a fully enclosed pipeline transportation system; Flexible layout; No secondary pollution; Efficient and energy-saving; Convenient material transportation and recovery, leak-free transportation, computer control, high degree of automation, stable operation of the rotary feeder, safe and reliable, and no pipe blockage; Roots blower is used as the air source, and the reliability of roots blower also determines the reliability of the system. Moreover, the designed pneumatic ash removal system has the advantages of simple process, maintenance-free, few equipment parts, no frequent action, few failure rates and almost no wearing parts. Low pressure continuous transportation, low and constant flow velocity in the pipe, so the wear is small. Low energy consumption, low operation cost and comprehensive investment saving. The system is equipped with low-pressure roots blower, which saves more than 20% energy, 50% operation cost and 30% comprehensive investment compared with warehouse pump system.