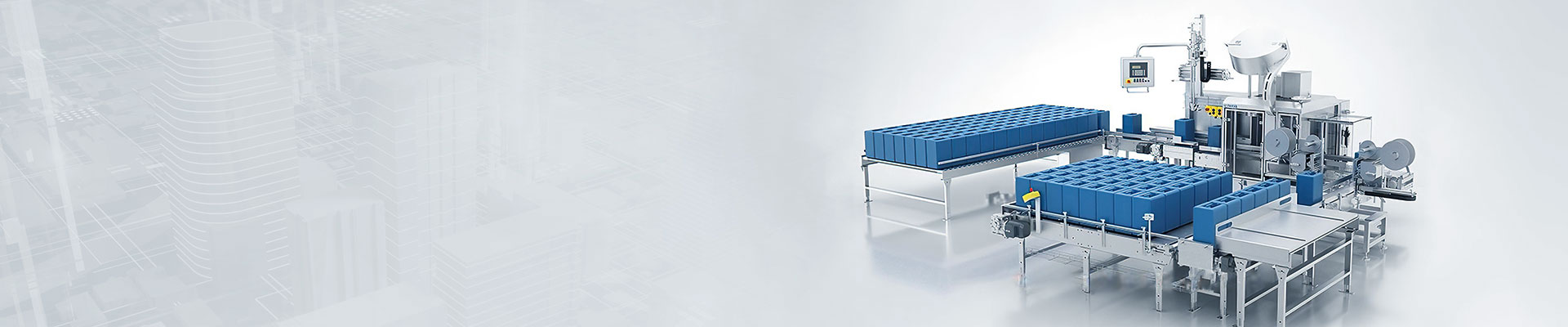
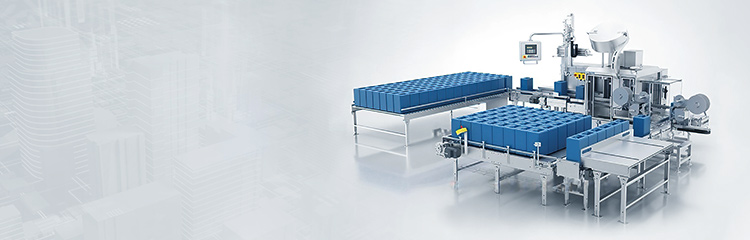
The filling machine sends the barcode data to the server by weighing module to get the barrel file data, and then sends it down to the filling scale through the weighing module. It adopts Profibus system configuration with PLC controller as the master and ET200 distributed I/0 as the slave to realize the control of the electronic scale, frequency converter and centrifugal pump as well as the monitoring of the level of each barrel and the manipulator. It accomplishes the functions of status monitoring, alarm display and manual operation of the metering and conveying process.

The Filling system is composed of three cylinders or oil cylinders (upper cylinder lower cylinder, control cylinder), two one-way filling valves (upper filling valve, lower filling valve), a quantitative cylinder and pipeline and other accessories. The storage tank is located in the high position by the pipeline and the upper filling valve connected to the upper filling valve by an elastic membrane is divided into two parts, can be separated from the material and the action of the upper cylinder to ensure that the material hygiene. The lower part is the main body of one-way filling valve with spring reset, which is connected with the storage tank and dosing cylinder. The upper part of the filling valve is installed with the upper cylinder, the piston rod of which controls the opening of the upper filling valve through the action of the elastic membrane. In the upper part of the upper cylinder is also installed a control cylinder, through which the cylinder can determine the upper cylinder piston rod stroke for the size of the two ways, and thus control the upper filling valve opening port size.
The core of the automatic Filling machine process lies in two filling processes: pre-filling and refilling. After peeling the empty cans by the filling system sent to the pre-filling below the pre-filling, pre-filling amount set in advance in the PLC, by the same service motor according to the PLC pulse command to drive the filling screw for filling. After the pre-filling is completed, the filling system sends the cans to the pre-filling and weighing station, the weighing module weighs the cans (generally in the pre-filling, about 1%-5% of the target weight will be left for the supplemental filling), and the actual value of the weighing is fed back to the PLC, which calculates (supplemental filling quantity = target weight - actual value of the pre-filling weighing) and gives the quantity of the supplemental filling, and the filling system sends the cans to the supplemental filling station to start supplemental filling. The filling system sends the can to the refilling position to start refilling. The filling system sends the can to the refilling position to start refilling. After the refilling is completed, the filling system sends the can to the refilling weighing module for testing, if the weight is qualified, the refilling is completed and the can is discharged; if there is a big gap from the target value, the can is sent to the refilling position by the filling system for the second refilling until the weight is qualified and the can is completed and the refilling is discharged.
Technical Parameters
Weighing range: 30kg
Weighing speed: (barrels/hour)
Allowable error: ±0.5%
Equipped with power supply: AC220V/50Hz±2Hz
Equipped with gas source: flow rate 0.3m3/min pressure 0.4~0.6MPa
Working temperature: 0℃~40℃Equipped power: 200(w)
Conveying distance: 1500(mm)
Long external dimensions: 500×800×1600(mm)