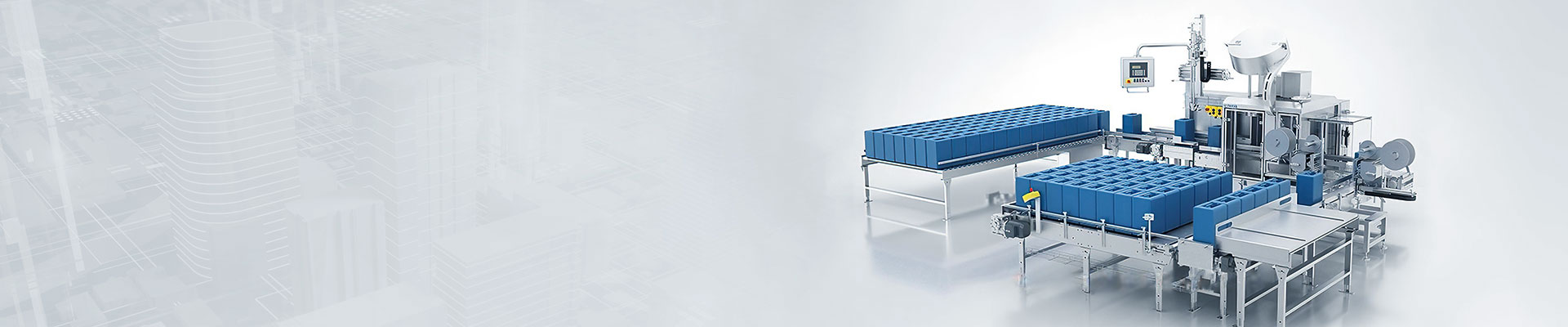
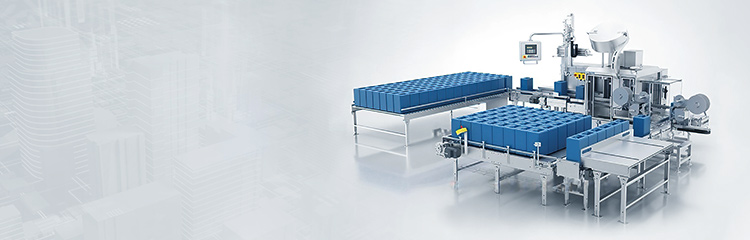
The paint filling machine takes images of the inspected barrels on the weighing platform of the inspection weighing module in real time and transmits them to the image acquisition card. After digital decoding, A/D conversion and other processing, it is transmitted to the computer memory via PCI bus for storage. Adopting automatic weighing, PLC control, electromechanical, computer interface and other automation technologies, we have developed and completed the intelligent filling weighing and inventory management system independently.

The automatic Filling machine adopts PLC control of inlet and outlet barrels, infrared ray positioning, Electronic scale measurement, automatic control of feeding pump function. The electronic scale automatically tare, weighing value instantly display, emergency stop/power failure dual protection, automatic alarm for over-difference; set up counter device to calculate and record the number of bottles, connect the counter to PLC, set and display the counting range through the touch screen control.
The automatic filling machine is equipped with front and rear bottle stop valves. The front stopper valve detects an empty bottle passing by and automatically stops the bottle, while the rear stopper valve also starts to stop the bottle, and the filling equipment starts to carry out the filling operation. The filling port is controlled by a solenoid valve and a flow meter to ensure the accuracy of the filling volume and the consistency of the filling volume. The solenoid valve and flow meter are controlled by PLC.
The capping machine is equipped with a specialized load cell to detect whether the bottle is in place or not. When the bottle reaches the specified position, the PLC sends out a command to control the capping machine for capping action. When the capping is completed, the bottle stopper valve is closed and the conveyor transfers the bottles to the next T-sequence point.
Liquid filling machine is equipped with a special labeling machine, the conveyor belt to pass over the bottle for automatic induction, when the bottle reaches the positioning point, the labeling machine to start the labeling action to complete the automatic labeling of the bottle. The automatic inkjet printer on the production line can sense the bottles for automatic inkjet operation.
In the whole filling production line, the servo system is used to control the running and stopping of the motor, so as to ensure the precision of the movement of the bottles in the whole filling process. The automatic filling machine is controlled by touch screen man-machine exchange system, when the operation of the production line is abnormal or malfunction, the system will automatically send out an alarm signal.
Technical Parameters
Weight range: 100-600kg
Material interface: DN40 material
Inlet pressure<0.6MPa
Filling speed: 1~2 barrels (200L)/minute (through diameter 1.5", material flow rate guaranteed 280L/min)
Filling accuracy: 0.2 grade
Spray gun structure: the material in contact with the material part of the material is 316, 316L stainless steel, the rest of the material is 304 stainless steel, carbon steel, etc.
Gas source: Pressure 0.5±0.1Mp, consumption 10m3/h, quick connector 8㎜ gas pipe
Power supply: 220(-15%~+10%) VAC, 50Hz