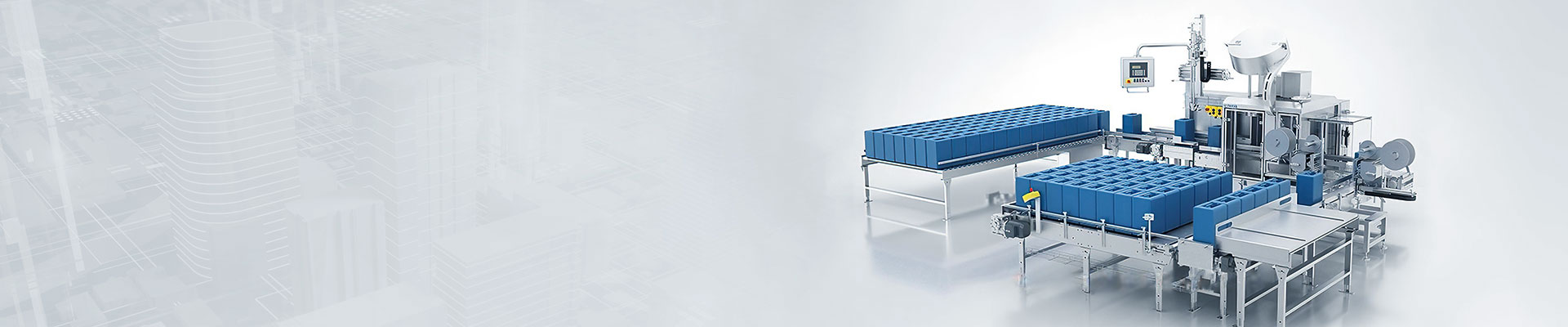
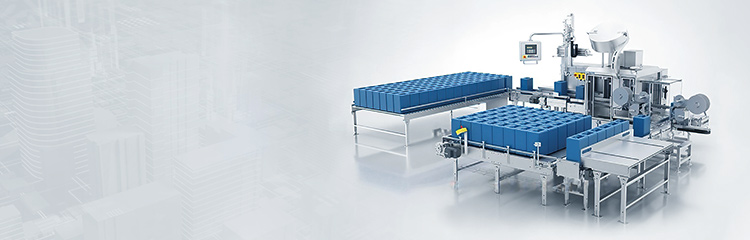
The weighing and feeding system is usually used for batch mixing of two or more raw materials in proportion to each other, and programmed to make the batch mixing continuous, so as to achieve uniformity in the mixing ratio. The human-machine interface is used to input the corresponding proportioning parameters, the signal of each weighing scale is transmitted to the weighing instrument through the load cell, and then the signal is converted by the weighing instrument and connected to the central controller, which, combined with the set formula and according to the real-time data of each weighing unit, controls the charging time and the amount of each kind of material, when all the raw materials are weighed and finished, they all enter into the reactor, and then, after sufficient mixing, enter into the dosing kettle by means of screw or gravity. After sufficient mixing, they will enter into the dosage tank by screw or gravity.

Weighing and feeding system is divided into material storage, batching, Measuring system and electrical control system, of which the control system has two operation modes, automatic and manual, simple operation, flexible control, which can satisfy all kinds of needs of the production, and it has high practicality. It can be adapted to powder, granule, liquid and other materials batching, mixing control. According to your requirements, we can customize a set of efficient, stable, fully meet your company's control requirements of industrial batching control system, batching software system solutions.
Weighing and feeding system is usually used for batch mixing of more than two kinds of raw materials according to the proportion, and programmed to make the batch mixing do continuous action, so as to achieve the uniformity of the mixing ratio of the performance. The human-machine interface is used to input the corresponding proportioning parameters, the signal of each weighing scale is transmitted to the weighing instrument through the load cell, and then the signal is converted by the weighing instrument and connected to the central controller, which, combined with the set formula and according to the real-time data of each weighing unit, controls the charging time and amount of each kind of material, when all the raw materials are weighed and finished, they all enter into the reaction kettle, and then, after sufficient mixing, enter into the batching kettle through the screw or gravity method. After sufficient mixing, they will enter into the dosage tank by screw or gravity.
The main functions and advantages of automatic Batching system:
1) It has the function of automatic dosage control for all kinds of solid materials in the formula, and the function of hand-feeding control.
2) With liquid scale weighing and liquid addition control function.
3) With flow meter adding liquid control function.
4) Timing control function for dry mixing, wet mixing and discharging of the mixer.
5) The system establishes a set of advanced security mechanisms and user rights management system, and assisted by the database security mechanism to ensure the safety of the software system information.
6) Adopt hybrid computer system design, stronger fault tolerance and high reliability.
7) Equipped with perfect special dosage software, system stability, high degree of intelligence.
8) Optional function: with formula import function.
9) Optional function: support production data uploading.
Feeding system perfect batching production information management system:
1)Formula management: input, storage, modification and deletion of formula.
2)Production management: order placement, execution and raw material demand statistics.
3) Raw material management: addition and deletion of raw materials.
4)Alarm management: alarm record, view and delete.
5)System parameters: mixing time, spotting time, closing time, drop compensation and hundreds of parameters such as silo, weighing hopper, mixer, small hopper, liquid spray, etc. can be set, modified and stored artificially.
6) Production data: you can add, delete and view the original production data.
7) report statistics: provide a variety of forms of various types of production reports, can meet the query requirements of different departments, all forms are provided in Excel file format to download.
8) User management: Permission management for system users; data backup and recovery functions.