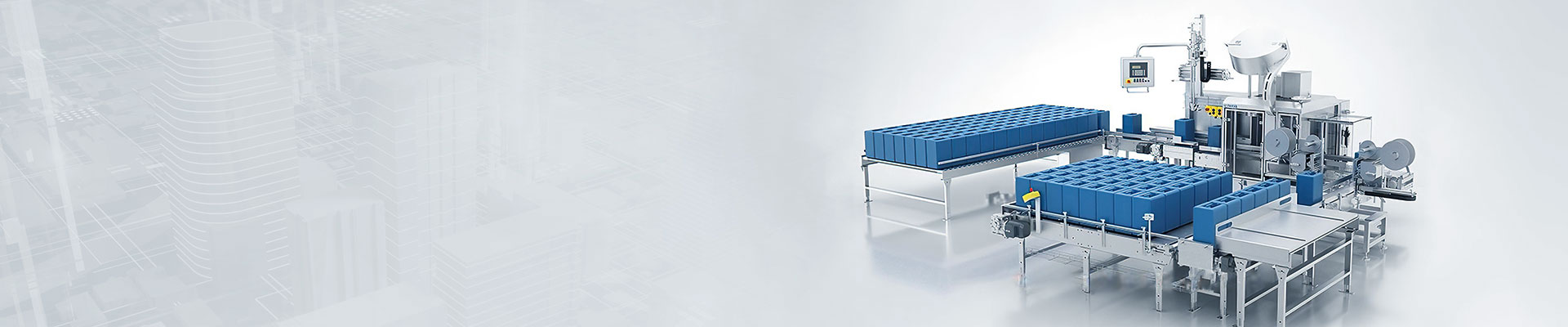
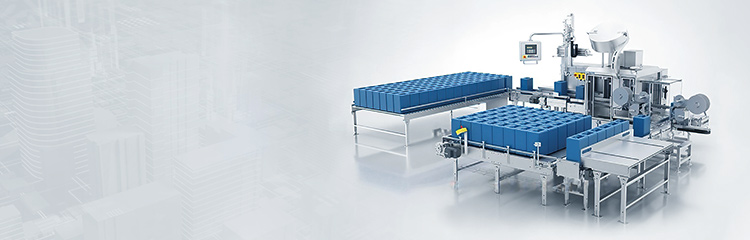
After the mixer reads it through PLC communication, the corresponding operation is performed. At the same time, PLC moves the monitoring signals to be collected by the touch screen into the communication storage area, and the touch screen can be monitored on the PC by reading the data, and the whole system is connected in series through pressure elements and weighing modules, so as to realize industrial automation, improve transportation efficiency and effectively prevent dust leakage, providing good environmental protection for field workers.

The weighing batching machine installs a weighing module at the bottom of the silo, which is accurately controlled by an electrical program to ensure the normal operation of the whole system. Positive pressure pulse acid pneumatic conveying link control object for the silo in the exhaust valve, feed valve, discharge valve, pulse air knife air valve and the upper air inlet valve. The control mode is controlled by Siemens programmable controller as the control source, through the operation of the Proface touch screen, contactor, intermediate relay on the solenoid valve and motor control, easy debugging and maintenance.
The automatic mixer is installed with activation hopper and gasification at the bottom of the storage bin. When discharging the material, the activation hopper vibrates continuously and the gasification sweeps to ensure the material falls smoothly, and the eccentric vibration module can be used to adjust the vibration amplitude to improve the efficiency and the frequency of the gasification sweeps. When conveying materials, the air knife valve can be adjusted to change the conveying volume and conveying efficiency by adjusting the air time and material time, which can help to meet the high requirements of some of the crushing rate. The pulse interval and pulse width can also be adjusted to avoid the leakage of dust from the receiving bin during the conveying process.
The automatic Feeder is installed with activation hopper and gasification at the bottom of the storage bin. When discharging the material, the activation hopper vibrates continuously and the gasification sweeps to ensure the material falls smoothly, and the eccentric vibration module can be used to adjust the vibration amplitude to improve the efficiency and the frequency of gasification sweep. When conveying materials, the air knife valve can be adjusted to change the conveying volume and conveying efficiency by adjusting the air time and material time, which can help to meet the high requirements of some of the crushing rate. The pulse interval and pulse width can also be adjusted to avoid the leakage of dust from the receiving bin during the conveying process.
Advantages of automatic dosing:
1,With automatic dosage control function and hand feeding control function for various solid materials in the formula.
2,With liquid scale weighing and adding liquid control function.
3,With flow meter adding liquid control function.
4,Timing control function for dry mixing, wet mixing and discharging of the mixer.
5,the system to establish a set of advanced security mechanisms and user rights management system, and assisted by the database security mechanism to ensure the security of the software system information.
6,Adopting hybrid computer system design, stronger fault tolerance and high reliability.
7,Equipped with perfect special dosage software, stable system, high degree of intelligence.
8,Optional function: with formula import function.
9,Optional function: support production data upload.
The dosing system improves the production information management system:
1,Recipe management: input, storage, modification and deletion of recipes.
2,production management: order placement, execution and raw material demand statistics.
3,raw materials management: the addition and deletion of raw materials.
4,alarm management: alarm records, view and delete.
5,the system parameters: mixing time, pointing time, closing time, fall compensation and silo, weighing hopper, mixer, small hopper, spray liquid and other hundreds of parameters for human setting, modification and storage.
6,production data: you can add, delete, view the original production data.
7,report statistics: to provide a variety of forms of various types of production reports, can meet the query requirements of different departments, all forms are provided in Excel file format to download.
8,User management: Permission management for system users; data backup and recovery functions.