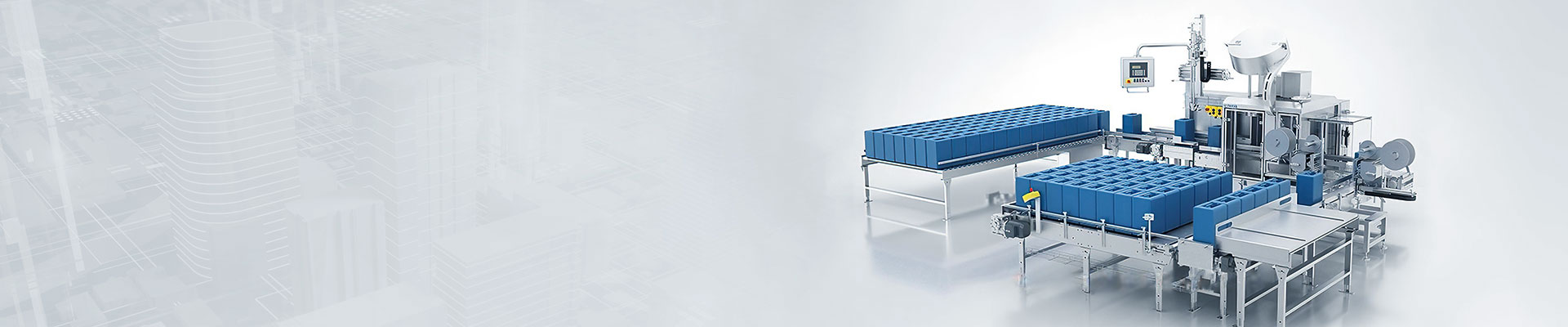
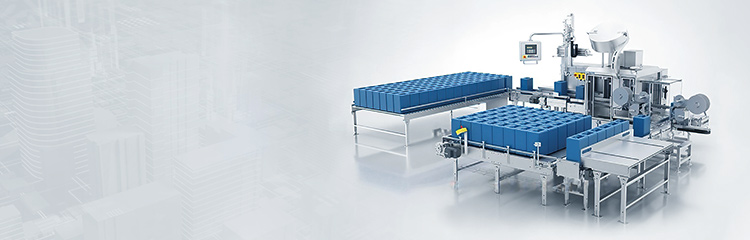
The automatic feeding system realizes a historical record of all measurement points on the basis of real-time trends. Once you need to trace the past data information, open the historical trend page, click the right mouse button on the blank space below, and in the pop-up dialog box, you can select any curve you want. Through the "Set Parameters" button on the Historical Trend page, the curve can be displayed according to the time period specified by the user. Meanwhile, the events occurred during the operation can be displayed in real time and queried in the history alarm page, the query content includes: time, date and time of alarm occurrence, alarm limit value, alarm recovery time, operation user, alarm variable name, etc.

The automatic feeding system realizes the historical record of all measuring points on the basis of real-time trend. Once you need to trace the past data information, open the historical trend page, click the right mouse button on the blank space below, and in the pop-up dialog box, you can select any curve you need. Through the "Set Parameters" button on the Historical Trend page, the curve can be displayed according to the time period specified by the user. Meanwhile, the events occurred in the process of operation can be displayed in real time and queried in the history alarm page, the query content includes: time, date and time of alarm occurrence, alarm limit value, alarm recovery time, operating user, alarm variable name and so on.
The automatic feeding system is after the feeding equipment puts all kinds of different raw materials into their respective hoppers, and then feeds them into the weighing hopper according to the given ratio of the formula and weighs them, and then sends them into the mixing machine for a certain period of time for stirring and mixing them uniformly into the finished products. Various fixed formulas are inputted into the computer beforehand, and the computer controls the discharging, weighing and mixing according to the proportion of the formulas, and detects the signals of the weighing module in real time, makes a judgment, and sends out the commands to each actuator of the dosage, so as to realize the automation of the dosage. The whole production system is equipped with manual control auxiliary mechanism, which can be controlled according to automatic or manual working mode.
Automatic Dosage system has a total of kettle weighing control in the dosage of the dosage weight that is Weighing modules and weighing instruments, each kettle weighing are 3 or 4 measurement modules, each group of weighing modules in parallel or in series by 4 or 6 with the signal line to access the signal line junction box of the weighing module, and then access to the TR200H weighing indicator, the load cell signal is 2MV/V, sensitivity of high and low signal transmission, shall be through the weighing terminal The load cell signal is a 2MV/V signal with low sensitivity, which must be converted into an analog signal by the weighing terminal and sent to the analog signal acquisition module of the PLC.
The whole loading system only needs weighing module, junction box, weighing control instrument, wiring cabinet, PLC, analog input module, communication module, touch screen synchronous control, the main hardware consists of two computers, high-performance microcomputer controllers, human-computer interface, high-speed and high-precision weighing unit and internationally famous low-voltage electrical components, combined with self-developed professional control software to achieve the automation of the control of the production of chemical liquids, the High metering precision and low manufacturing cost.