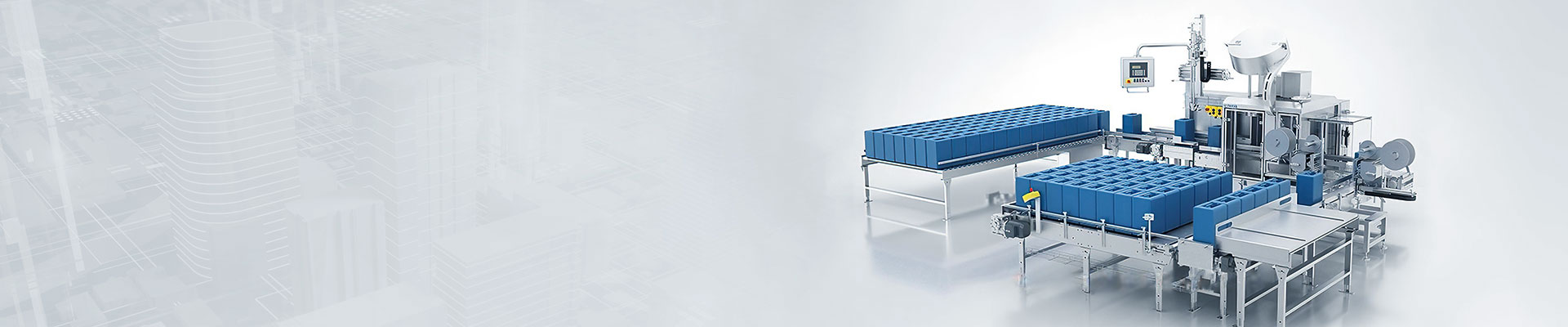
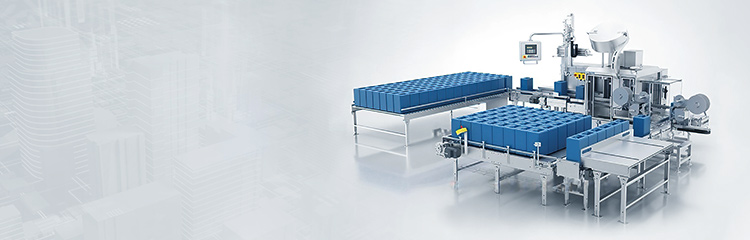
The automatic mixer is equipped with an activation hopper and gasification at the bottom of the storage bin. When discharging, the activation hopper vibrates continuously and the gasification purging ensures the smooth falling of materials, and the eccentric vibration module can be used to adjust the vibration amplitude to improve the efficiency and gasification purging frequency. When conveying materials, the conveying capacity and conveying efficiency can be changed by adjusting the air time and material time of the air knife valve, which is helpful to meet some links with high requirements for crushing rate. The pulse interval and pulse width can also be adjusted to avoid dust leakage in the storage bin during transportation.

Weighing and mixing machine through the dosage of each raw material ratio, to achieve the requirements of the dosage control accuracy, try to reduce costs. According to the different materials in each batch and arbitrary changes to optimize the calculation table into the database using VisualBasic to develop a visual human-computer interface, read the calculation data and display it in the interface, visual creation of database applications, so that the application of the database is more convenient, flexible, and at the same time, support for the application of the network environment.
The dosing machine adopts pulse width modulation (PWM) control method based on incremental PID algorithm, i.e. the duty cycle of PWM square wave is obtained by incremental PID algorithm. The regulation signal derived from the algorithm is output to the D/A holding circuit through the PB1 port (PWM) of ATmega8, and the amount of regulation determines the duty cycle of the PWM square wave. The D/A holding circuit converts the duty cycle of the PWM square wave into the corresponding 0-5V voltage value and outputs it after optoelectronic isolation, and the frequency inverter determines the screw speed according to the voltage value, thus controlling the flow rate of the material.
The feeding system detects the material level switch of the raw material warehouse, automatically controls the elevator of the raw material warehouse and the feeding plug valves of the 1#~4# tanks and realizes the system interlocking to ensure that the raw material warehouse is not empty to ensure the supply of raw materials to the system. The centralized control system and Siemens weighing control system realizes automatic control and interlocking of star unloader and electro-hydraulic three-way flap valve of 1#~4# silos, which are automatically transported to 1# and 2# metering drums successively, and the weight of silo feeding can be set and modified in the computer of the operation station. After receiving the request for discharging, the feeding plug valve of the chemical compound barrel will be opened automatically, and when the weight of discharging reaches the set value, the plug valve will be closed automatically, so as to realize the quantitative automatic loading of the chemical compound barrels, and the quantitative value and the number of times of discharging can be set in the computer of the operation station and can be modified. The system realizes the automatic start and stop, switching and interlocking and time delay of each conveyor, mixer, elevator, valve and other equipments to ensure the safe production requirements of the batching automatic metering control system.
Components of pneumatic feeding systems
Dense-phase pneumatic batching is a high concentration ratio, high mixing ratio, low-flow state conveying, materials in the pipeline into a peg or dune shape, in the form of a group to push forward, the source of conveying power mainly depends on the pressure difference between the front and rear of the pegs to achieve the material dosage, which mainly consists of compressed air air supply system, material supply system, control system, piping system, material storage and its ancillary systems, etc..
(1) compressed air air source system mainly consists of air compressor, de-oiler, dryer, storage tanks and pipelines, mainly for material transportation and air control components to provide high-quality compressed air. In short-distance transportation can also be used instead of high-pressure Roots blower.
(2) The main purpose of the weighing control system is to supply the material from the low-pressure container to the high-pressure conveying pipeline, and as far as possible to ensure that the material enters the high-pressure pipeline as far as possible to ensure that the compressed air and compressed air are evenly mixed. At present, the common feeding device is mainly warehouse pneumatic conveying pump, in the case of conveying distance is not far away can also be used in high-pressure rotary Feeder. At present, the main feeding devices used in our company are F-type warehouse pneumatic conveying pump, V-type warehouse pneumatic conveying pump and L-type warehouse pneumatic conveying pump.
(3) The feeding system is mainly controlled by microprocessor-based programmable controller PLC, which can realize in situ manual control, automatic control or remote computer centralized control, etc., the action of each mechanical component to realize the automatic operation of each control component of the conveying system and data acquisition with manual operation switching function.
(4) The piping system includes conveying pipes, elbows, necessary reducers and make-up valves, etc. The main purpose is to ensure that the material is conveyed in a closed state, without pollution to the outside world, and to ensure that the material in the conveying process and the mixing of gases, to prevent the phenomenon of blocking the pipe.
(5) The material storage and its ancillary systems mainly include material storage, material level meter, pressure vacuum release valve, dust collector, unloading valve and other devices.