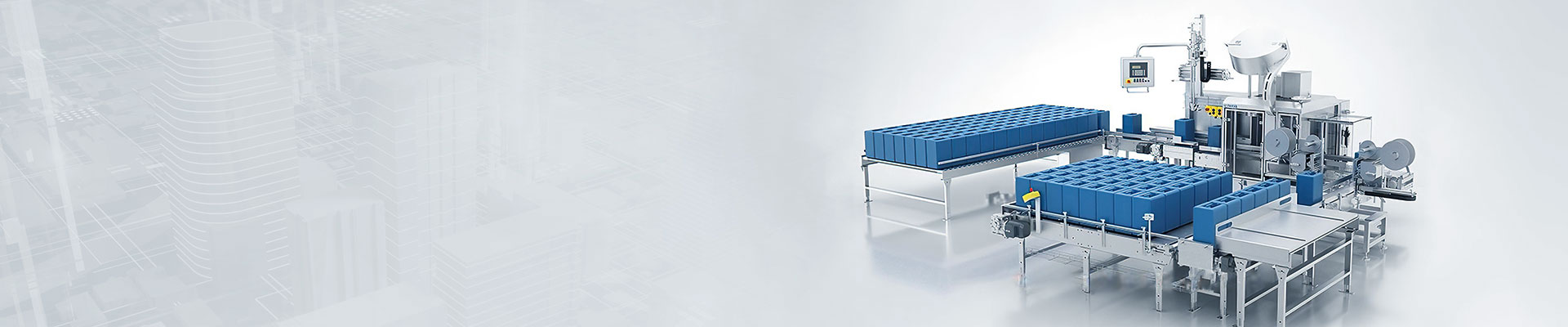
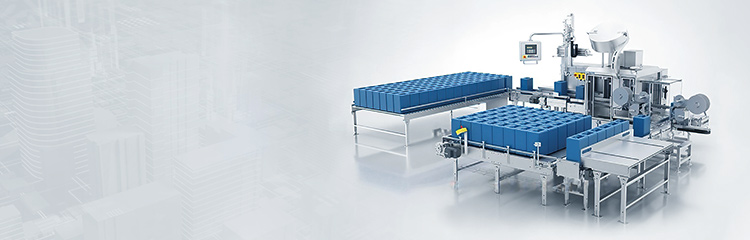
Automatic batching machine adopts intelligent production line and control system to unpack, transport, storage, measurement, dosing, feeding, mixing, packaging, encapsulation, dust removal and other production processes of raw materials. Combining the latest information technology with production management and production process, it can realize production raw material management, production plan management, production formula management, data report management, dynamic real-time monitoring, fault diagnosis and analysis, remote monitoring functions.

The automatic batching machine consists of big storage bin, bag filter, induced draft fan, balance valve, screw feeding device, storage hopper, etc. The powder sent by the conveying system is sent to different big storage bins for storage according to the model. When conveying the powder, the induced draft fan automatically opens and controls the powder flying through the bag filter, the balance valve automatically opens to balance the pressure in the big storage silo, the screw feeding device at the bottom of the big storage silo sends the powder to the storage hopper to wait for the further conveying to the Weighing system, and the balance valve will be automatically closed after the conveying is finished. The large storage silo is designed with three levels of control: high, medium and low. When the material level is at the low level, the material must be added, and at the high level, the material must be stopped.
The conveying system consists of gas source, pressure conveying tank, distribution valve and double pipe conveying pipeline. After the powder is sent to the pressure conveying tank through the unpacking hopper, compressed air is sent to the tank to blow the powder up, so that the powder is in the floating state. When the pressure in the pressure conveying tank reaches a certain value, keep the pressure for 2-3min, and then open the discharge valve, at the same time open the compressed air valve on the conveying pipeline, under the action of the compressed air powder along the conveying pipeline to the storage tank. In order to ensure that the conveying pressure is constant, there will be compressed air with the same pressure supplemented to the conveying pipeline at certain intervals, which can ensure the conveying speed. The conveying pipeline is a double tube structure, the inner tube is flexible rubber material tube, which can resist powder erosion and reduce the powder particles crushing rate in high-speed conveying. The outer tube is made of hard aluminum alloy, which can withstand certain pressure.
Powder weighing and charging is composed of day storage hopper, bag filter, balancing valve, charging screw, central bag filter, recycling screw, powder weighing module, powder calibration scale and discharging fork and so on. Powder through the conveying system to the day storage hopper waiting for weighing, start weighing and charging, the day storage hopper at the bottom of the charging valve opens, charging screw action, the powder powder will be transported to the powder weighing scale (conveying powder, the central bag filter will be adsorbed to the bag filter bag, to prevent the powder from flying pollution). After the powder weighing is completed, the disk valve of the powder weighing scale opens, and the powder is unloaded to the powder calibration scale along the charging pipe to calibrate the accuracy of the weighing. After the calibration is completed, the discharge valve of the powder calibration scale opens, and the powder is sent to the mixing chamber of the batching machine through the pipe via the discharge fork.