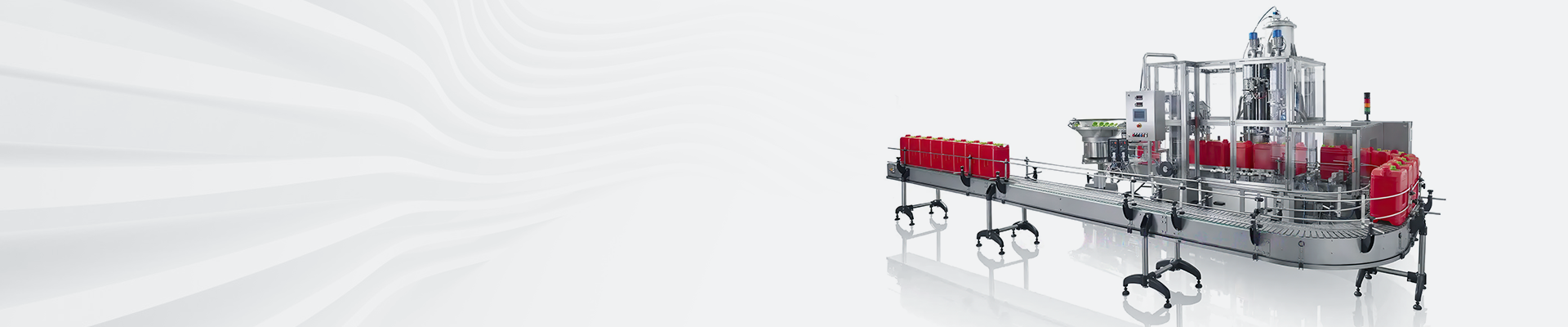
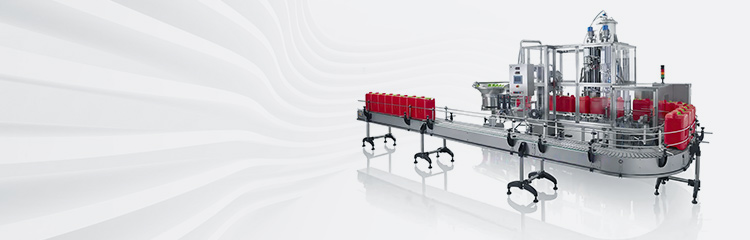

Summary:The batching system refers to equipment that adds value to materials through mixing, separation, molding or chemical reactions. Based on the BOM management method, following the batching priority of products of different properties, the default batching line and the relationship between materials constitute the ideal batching model.
I. Characterization of dosage planning and control activities
A dosing system is equipment that adds value to materials by mixing, separating, molding, or chemically reacting. Batching system processes can be continuous and batch. A batch-type batching system is a manufacturing technique in which materials are accumulated and processed one batch at a time simultaneously; a continuous feeding system is one in which the product stream is continuous, uninterrupted, and indivisible.
(1) The mixer is a large-volume continuous batching, thus emphasizing the wholeness of the batching system process and the relative stability of the process flow.
(2) The production process of batching machine includes information flow, material flow, energy flow, and accompanied by complex physical and chemical reactions, as well as mutability and uncertainty and other factors, such as uncertain input and output and co-products and by-products, etc., which is a very complex and large system.
(3) The BOM of a weighing control system is a formula, recipe, or list of ingredients, which may vary in quality from batch to batch. For secondary materials, typical BOM-based management methods can be utilized. However, the management of primary materials is different and usually requires a cross-functional committee or an operations manager to allocate the primary materials and determine the formula.
(4) batching control system production lead time is long, the equipment can not easily stop, equipment, the coupling between the operation is very high, often the adjustment of a parameter will affect the other parameters and the quality of the product in the subsequent processes, so the degree of accuracy of the batching system control is generally higher than the discrete manufacturing industry.
(5) planning and control requirements for the overall optimization. The optimization of each device is not equal to the whole plant is at the optimum, and thus in the process of seeking the global optimum will sometimes get conflicting conclusions.
(6) pay more attention to the effective utilization of equipment. Batching system plan on the equipment capacity is extremely important. The connection between the dosage system devices has piping constraints, continuous logistics, or only complex and limited intermediate storage strategy (such as storage pool capacity, temperature, storage time requirements).
(7) dosage, discrete decision variables and continuous decision variables coexist, the system includes both continuous process variables, such as the dosage process; also includes discrete process variables, such as dosage production program switching, scheduling instructions, the introduction of random events, dosage device switching, etc., so the continuous process of the dosage planning / scheduling system is a hybrid system. This kind of mixing includes both the same level of mixing, but also includes the mixing between the progressive levels.
(8) dosage is often in a very harsh dosage production environment, so the safety and environmental requirements of the dosage system is placed in the most important position.
(9) The raw materials and products used in dosage are usually perishable (e.g., foodstuffs), so this constraint is taken into account in dosage planning and inventory management.
(10) Due to the large batch sizes of ingredients and the generally more stable nature of the batching process, the batching system's batching plan and operations plan are usually closely linked and are generally difficult to distinguish. In the long-term or medium-term dosage system plan usually at the same time to take into account the detailed process issues, such as the production batch and job scheduling at the same time in the dosage system design. Whereas in discrete manufacturing of small batch multi-species dosage systems, scheduling issues are usually considered at the job planning level.
II. Algorithms for APS in automatic batching
(1) Mathematical Planning Algorithms
Mixed integer linear programming or mixed integer nonlinear programming is widely used. A mathematical planning model is built for chemical companies to solve the problem of assigning tasks in the dosage system under the condition of minimizing the total cost as well as the problem of assigning products. A generalized MINLP model is also developed with the objective of minimizing the maximum completion time and determining the production lot size. A greedy heuristic algorithm is used and compared with other heuristics.
Need to consider planning period length, raw material availability, finite loads, cleaning operations,mixed integer planning via Cplex. But mathematical models are almost non-reusable and even small changes may make the chosen algorithm extremely ineffective. Mathematical planning is too computationally intensive for solving real-world problems, such as the branch-and-bound (B&B) method. Various improved forms of B&B algorithms or simplified computational techniques are used to improve efficiency. Heuristic algorithms are used in order to consider simpler models.
(2) Constraint Planning
A representative of constraint propagation that can be successfully used to solve manufacturing batching system planning problems is ILOGOptimizationSuite.Constraint planning is very suitable when a large number of constraints must be considered in the plan. A methodology adapted to the needs of dosage systems. This approach uses constraint directed search for the combinatorial part of the solution to the problem and determines whether the remaining (N)LP problem is solved. The combinatorial part of the solution includes, among other things, user interventions through the assignment of values to the variables and heuristic rules that specify the values and order of the variables.
(3) Simulation Methods
The general simulation approach is combined with mathematical modeling and rule scheduling to solve the problem. In contrast to mathematical planning, which uses a global, simplified view, simulation provides a localized visual observation of the results of all tasks, sequencing, and timing decisions, and enables a detailed, fast analysis of a particular planning problem at a low computational cost. Simulation is generally a comparative analysis of available alternatives and can be used to evaluate candidate plans proposed by the user.
(4) Artificial Intelligence
In recent years, artificial intelligence techniques have been introduced into the field of ingredient planning as an effective way to solve planning problems. Combining mathematical planning methods with artificial intelligence techniques and expert systems is a better approach. Artificial intelligence has been significantly successful in solving complex problems in a large number of scientific fields.
For example, simulated annealing algorithm is superior to heuristic methods in solving batch scheduling problems with hybrid optimization methods. A neural network based model for batch batching schedule control tool for maximum completion time (makespan) is proposed. The model predicts well. However, the neural network model cannot visualize the job nature and job interaction. Genetic algorithm is a stochastic search technique that mimics the natural evolution of organisms. Since Goldberg and Davis published the genetic algorithm, it has been used to solve scheduling problems.
III.DEVELOPMENT OF AUTOMATIC BATCH PLANNING MODELS APS
MRP system is not adapted to the dosage, for the characteristics of the chemical industry: the special nature of the demand for raw materials; the special nature of the dosage management; planning and scheduling of the special nature of the emergence of automatic dosage specifically for the APS system.
APS can be used to achieve flexible and variable dosage planning, visualization of dosage sequencing, automatic dosage operation instructions, dynamic supply chain planning adjustments, and maximum utilization of equipment dosage capacity.
Factors to be considered for modeling automated batching plan scheduling:
(1) Recipe Management: The BOM for automated batching is a formula, recipe, or list of ingredients that may vary in quality from batch to batch. For auxiliary materials, typical BOM-based management methods can be utilized. However, the management of primary ingredients is different and usually requires the operations manager to allocate the primary ingredients and determine the formula. Co-products and by-products (co-Product and by-Product) need to be handled in the formulation
(2) Batching capacity: Batching line capacity: information on the capacity per unit of time for each product on each batching system, the feed lot, and the output lot.
(3) Batching Calendar: the working calendar of each batching line in the batching plant, which can be defined and adjusted to each minute and second according to the need.
(4) Batch management: You can customize the rules of product batch number and encrypt the batch number.
(5) Cleaning time: Cleaning information: Usually, after a product is finished dosing, it can not directly dosage the next product, but need to clean the residual material left in the dosage line before starting to dosage the next product. The cleaning time from one product to the next may be different.
(6) Multiple units of measurement: in the storage and transportation of materials and processing, the unit of measurement will be a variety of conversions, the effectiveness of the relationship between multiple packaging units.
(7) optimization of the dosage line and material correspondence dosage mode: ideal dosage mode: in a certain cycle range, dosage of multiple products, will follow a certain order of priority to arrange the dosage. Usually in the dosage scheduling process, in the same dosage line, the dosage priority of products of different nature, the default dosage line and the relationship between the material constitutes the ideal dosage pattern.
IV. Advanced Planning
Develop medium and long term sales plans based on demand plan forecasts from APS; develop and revise rolling sales plans based on sales orders and sales forecasts; develop and revise rolling ingredient plans based on rolling sales plans with reference to dynamic inventory constraints and capacity constraints.
Based on demand forecasts and distribution plans, the processing and aggregation of enterprise medium and long-term plans can be formulated, and can be automatically homogenized in accordance with the calendar cycle; the rolling sales plan can be dynamically adjusted and optimized based on the weekly/monthly sales situation; the formulation and revision of rolling batching plans can be simulated in real time with reference to the setting of upper and lower inventory limits, the dynamics of stocking out and stocking in, and the finite capacity constraints; it can meet the needs of dynamically changing plan management. To meet the needs of the dynamic change of the plan management, whether long-term or short-term plan with optimization, comparison, executability; dosage system and procurement of the unified coordination, unified plan management platform;
V. Advanced Dynamic Sorting
Through the dosage scheduling automatically according to the standard capacity of each product in the dosage line, priority, machine cleaning time, etc., accurate arrangement of the daily order plan. It can insert and reduce the order of dosage in real time according to the influence of order urgency, dosage change and material preparation.
Batching sequencing can be corrected for start time and production, and the batching line can be readjusted to automatically reschedule the batching plan based on the corrected values. Supports scheduling beyond the factory calendar time range and allows dynamic overtime. Visualization of production scheduling by human-computer interaction, and support production scheduling of multiple batching lines in the same interface. Dosage scheduling data can be backtracked to the source of demand. Considerations. Uncertainties in delivery, batching, and demand The APS model considers the randomness of delays in delivery, the randomness of output, and the randomness of demand in the deterministic model, respectively.
VI. automatic product recovery oriented batching
For the quantitative model in reverse logistics is can be divided into three areas: distribution planning, inventory control, batching plan.
The batching plan is mainly the reuse of materials. The trade-off between the value of regenerated and reusable materials. the APS model mainly requires the calculation of the cost and processing time for all possible regeneration and reuse.
Consider reverse logistics in the context of stochastic demand, recycling, and output, and use simulation to ensure the level of safety stock required for a given level of service.
VII. Lean Batching
The capacity of automated batching is fixed due to the capital sensitivity or resource constraints of the batching process. Despite the lack of flexibility in automated batching activities, it is possible to adopt a lean philosophy that focuses on non-batching activities such as raw material movement and storage, and rarely on flexible batching activities, with a general focus on raw material and distribution management. Since the machine cannot be stopped, find ways to apply lean principles in other areas. For example, limit the number of problem points and avoid variation. Identify bottlenecks and readily mobilize labor based on inventory to avoid rigidity, etc. Improve logistics activities to eliminate waste, such as overstocking, excessive lead times, waiting times, extra transportation, and other activities.
VIII. Digital factory with automatic dosage
In the petrochemical, iron and steel, metallurgy, building materials, textiles, paper, pharmaceuticals, food and other process manufacturing areas, the intrinsic motivation for the development of intelligent manufacturing is the quality of the product can be controlled, focusing on the digital construction from the dosage to start, based on the demand for quality control from the end of the product to the whole process of control change.
Digitization of the dosage process, in the dosage manufacturing, process management and other individual aspects of information system construction, based on the construction of a dynamic and transparent traceability system covering the entire process, based on a unified visualization platform to achieve the whole process of product dosage cross-sectoral collaborative control.
Integration of ingredient management, build enterprise digital integrated system, deepen the integration of ingredient manufacturing with core business systems such as operation management, procurement and sales, and promote the integration and sharing of resources and information within the enterprise.
Supply chain synergization, based on raw material procurement and distribution needs, expand the digital factory to suppliers and logistics enterprises, horizontally integrate suppliers and material distribution synergistic resources and networks, realize the systematization and proceduralization of external raw material supply and internal batching and distribution, and improve the efficiency of supply chain operation inside and outside the factory.
Nine, the transformation and upgrading of the automatic dosage system in the era of intellectual manufacturing
Automatic dosage enterprises are characterized by pipeline material transportation, strong dosage continuity, more standardized processes, less process flexibility, more single products, more stable raw materials. For automatic batching, it is difficult to realize digitalization due to the physical and chemical process carried out by raw materials throughout the material transformation process, and the continuity of the process makes the influence of the previous process on the next process conductive, i.e., if the raw materials of the first process are unavailable, it will affect the second process.
Therefore, the focus of automatic batching intelligent construction is to realize intelligent optimization of batching process and intelligent optimization of the whole process of batching, i.e., intelligent perception of changes in batching conditions, autonomous decision-making system control instructions, automatic control of the equipment, in the event of abnormal working conditions, instant prediction and self-healing control, to exclude anomalies and achieve safe and optimal operation; on this basis, to realize the APS Advanced Optimization Decision-making System, and then gradually evolve to the CPS Advanced Intelligent System, which intelligently senses the changes in batching conditions. On this basis, it realizes APS advanced optimization decision-making system, and then gradually evolves to CPS advanced intelligent system, which intelligently senses the status of logistics, energy flow and information flow, learns and responds autonomously, and realizes automatic decision-making.