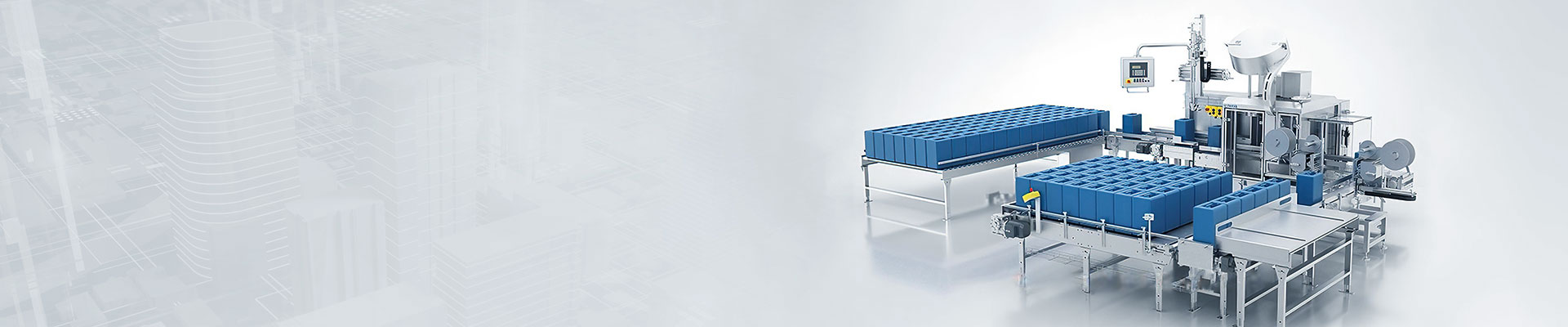
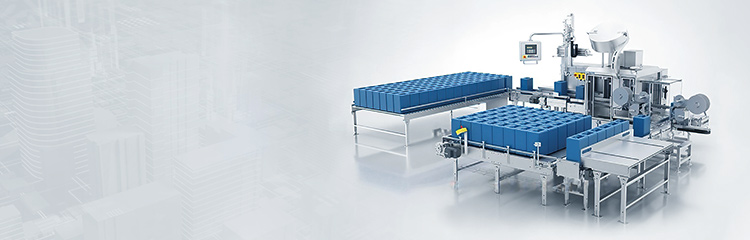
The dosing machine adopts pulse width modulation (PWM) control method based on incremental PID algorithm, i.e., the duty cycle of PWM square wave is derived from the incremental PID algorithm. The regulation signal derived from the algorithm is output to the D/A holding circuit through the PB1 port (PWM) of ATmega8, and the amount of regulation determines the duty cycle of the PWM square wave. The D/A holding circuit converts the duty cycle of the PWM square wave into the corresponding 0-5V voltage value and outputs it after optoelectronic isolation, and the frequency inverter determines the screw rotation speed according to the voltage value so as to control the flow rate of materials.

The kettle weighing shows the weight of the material in the hopper in real time by means of A/D conversion, where the weight indicator transmits the displayed weight data to the PLC by means of serial communication, the PLC compares the collected weight of the instrument with the weight set by the touch screen (or by the computer), and the weighing control instrument controls the weighing action of the whole metering and dosage machine. If configured with computerized management system, the computer can dynamically display the working status of the batching machine, print the weighing data in real time and store the historical data records, which is convenient for the users to monitor the working status of the batching machine and find the historical data. In addition, the weighing terminal in the office of the company through the wide area network, the company's computer and the field user's computer connection, the company's engineers can be operated in the company's office on-site user's computer, real-time monitoring of the weighing status of measuring and batching machine, once the user equipment problems, the user only need to connect the network cable to the system, the company's professional engineers can be in the company for the user thousands of miles away from the implementation of remote service, truly realize the fastest and most convenient way to achieve the goal. The implementation of remote service, really fast response.
The design of measuring batching machine Batching system, must achieve a stable and reliable operation, simple and practical operation, as well as superior cost-effective, are very important. On the basis of the original system, still Advantech industrial control microcomputer as the host computer, PLC components to increase the configuration of switching and analog input and output modules, as well as manual - automatic control switch, the necessary hand-control buttons and indicators, etc., to minimize the investment in system hardware. The control software is upgraded to improve the alarm and processing, and expand the intelligent control function of the reaction process.
Batching with PLC programmable controller as the core, the upper computer adopts high-performance configuration software, develops reliable operation, easy to learn, practical and stable monitoring program, mixing kettle with full Chinese interface, real-time data display, flow and temperature control curves, alarms and operation records, as well as complete production reports and other management functions, and embedded in the intelligent automatic control module of the batching system.
The upper industrial control computer as the human-machine interface can realize the following functions: real-time dynamic display of the operating status of each device, including real-time changes in the weight of the raw material tank, the feeding flow rate of all kinds of materials, valve action and temperature display. The simulation process graphics are realistic and intuitive. Display the real-time curve and historical curve of each process parameter, compare with the set process curve, and guide the process operation. The historical curve can be saved for one year or more, and the user can check it at any time. Storing various process curves and ratios first, the dosing kettle can send control requirements to PLC at any time according to the process requirements of each product to complete the rapid transformation of production varieties and production processes. Perfect alarm and processing of the main process parameters to ensure the safety of the production process. Printing various production and statistical reports. With strong management function, it can print the actual weight of each batch and the data of temperature and pressure, etc., and carry out costing and process analysis on the stored data. Manual and automatic switching without disturbance. In order to strengthen the reliability of the Dosage system without losing flexibility, the dosage system is set up with computer screen operation, manual, automatic and operation desk button switch, two sets of manual and automatic working mode, and the operation of the reaction tank valve adopts the intelligent control instrumentation hand manipulator, which ensures the non-perturbative switching operation. Adaptive compensation technology is adopted, the weighing error of Electronic scale can be compensated most effectively. The mixing tank adopts intelligent control technology, through the dosage system jacket cooling water backwater and material plus