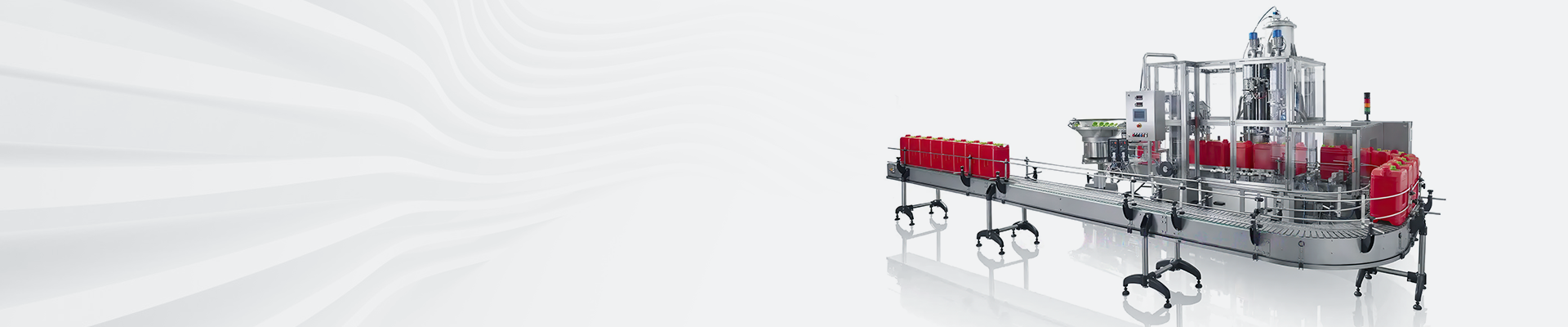
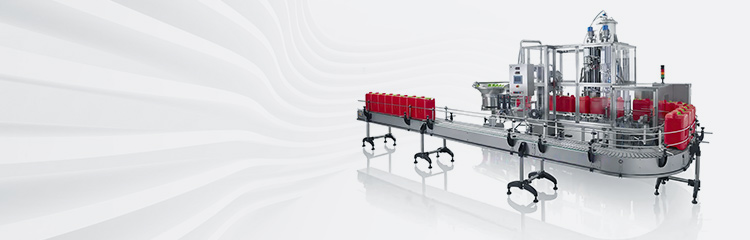

Summary:The automatic batching system uses continuous DC and low-frequency electromagnetic quantities and wireless control to ensure the batching accuracy of various forms of weighing control. It is composed of a computer (computer), weighing instrument, PLC and system software.
In modern industrial production, mixer has a very wide range of applications. Such as feed processing, steelmaking, production of cement, etc., in this production process often need to be different materials according to a certain proportion of heavy scene configuration for mixing and processing, is now designing a charging weight measurement device for batching production weighing control system.
Weighing mixer is the use of full-bridge measurement principle, through the circuit output voltage and the linear relationship between the standard weight, the establishment of a specific mathematical model, the voltage scale V changed to the weight scale g that is an original electronic scale. One of the most important components in the measurement circuit is the resistance should be load cell. The sensor uses a full-bridge measurement circuit, so that the system produces a smaller error, the output data is more accurate. The role of the three amplifier circuit is the sensor output of the weak analog signal for a certain number of times to meet the requirements of the input signal level of the A/D converter, the role of the A/D converter is to convert the analog signal into a digital signal, analog-to-digital conversion, and then the digital signal to the display circuit to go, and finally by the display circuit to display the results of the measurement.
Mixing machine is a kind of process that mixes many kinds of raw materials together in a certain proportion and processes them to produce a certain product. The realization of high-precision and fast dosage belt scale is extremely important to the production of industrial enterprises. Using a microcontroller for simple weighing calculations and PID adjustment, by placing two sets of belt carrying rollers on the lever-type weighing bridge, with the help of the weighing module to detect the weight of the materials on the belt into the totalizer, the speed sensor detects the speed of the belt, and inputs the speed information into the totalizer. The speed sensor detects the speed of the belt and inputs the speed information into the totalizer. The totalizer processes the received speed and weight signals to get the cumulative amount of material and the time flow. The belt conveyor transports the material from the feed bin or other feeding equipment and passes through the weighing module bridge for weight detection, while the speed sensor installed in the tail wheel detects the speed of the belt, and the detected weight and speed signals are sent to the accumulator for calculus processing and displaying the instantaneous flow rate in th and the cumulative volume in tons. The internal regulator compares the measured instantaneous flow rate signal value with the set flow rate value from the industrial control machine through the communication board, and outputs the corresponding signal value according to the deviation size, and changes the speed of the motor through the frequency converter in order to change the feeding volume to be consistent with the set value, thus completing the control of constant feeding flow rate. Accumulated amount of signal is sent to the industrial control machine to realize the set total amount of feed to meet the standard shutdown function of the conveyor metering are carried out in a solid pressure-resistant chamber. In the lower part of the conveyor metering, there is a scraper-type cleaning device, so that the scattered material and fly ash can be cleaned up to the discharge port. The whole system is equipped with belt deflection alarm, material blocking alarm and chain breaking alarm.
The shell of the weighing belt conveyor is made of steel plate welded into a sealed groove body, with well sealed movable doors at both ends and sides, which is convenient for installation and overhauling. Conveying and measuring parts are fixed on the two side walls of the trough body, the overall rigidity is good, which is conducive to measuring. The weighing module bridge is fully suspended with N3B type structure, the measuring module has high precision, good stability performance and good temperature compensation. The scale does not require maintenance. There is no accumulation of material in the weighing frame, so that the possibility of zero point drift no longer exists. The head and tail sections are equipped with a head cleaner and an internal cleaner, which are able to clean off the powder adhering to the belt inside and outside, thus avoiding repeated measurement of the material and belt deflection due to the powder bonding surface. The scraper of the head cleaner is high polymer polyethylene plate, and the scraper of the inner cleaner is rubber plate. There is also a chain-driven scraper sweeping device in the trough of the court section, and the scraper sweeping can be used to clean up fly ash and scattered materials. Belt machine shell around the opening of the observation window, the top is equipped with lighting. You can observe the operation of the belt scale at any time without the need to