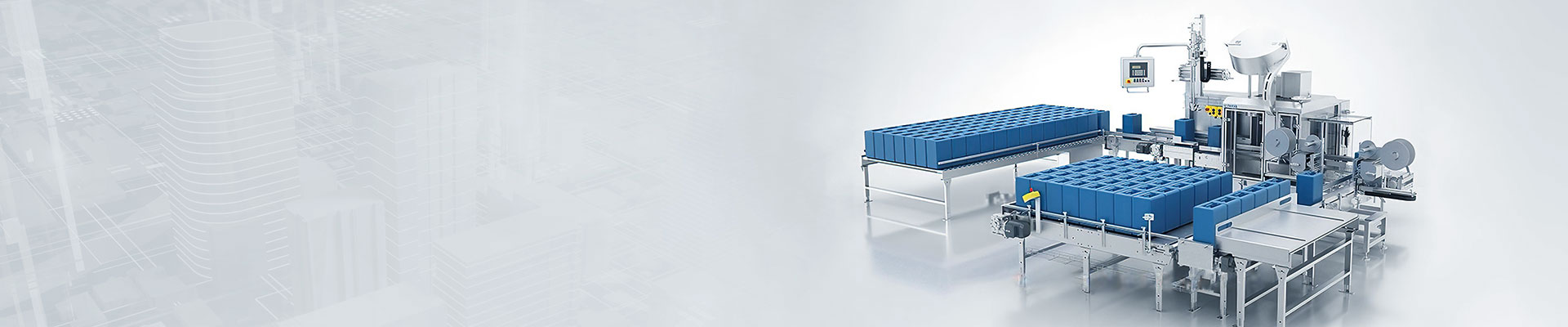
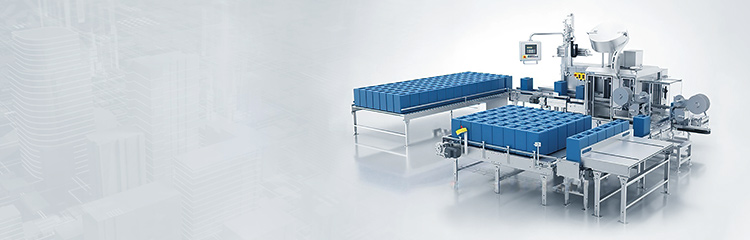
The dosage scale utilizes the analog input template in the PLC to collect the data on site in real time. The actual values are calculated according to the different ranges of the flow rate of each weighing module's measuring tank, and the converted values are averaged to minimize the flow rate fluctuations, which facilitates the application of the weighing values to the PID circuit adjustment and ensures the stability of the weighing adjustment. The display of material level adopts the display mode of one way on site and one way in the main control room, which facilitates the real-time monitoring of the material level of the silo from two aspects, and ensures that when the material level is low, the on-site personnel will take the measure of adding material to prevent the occurrence of material breakage.

Batching weighing hopper material weight reduction rate to control the discharge screw machine or electric vibration machine, in order to achieve the purpose of quantitative feeding, that is, batching scale. When the material in the weighing hopper reaches the lower limit of weighing, the discharging screw machine fixes the discharging amount according to the rotating speed at that time, and at the same time controls the material in the silo to go down to the weighing hopper quickly, and stops loading when the material reaches the upper limit of weighing, so that the quick loading can shorten the feeding time, and improve the accuracy and control precision of weighing.
Weighing control system is based on the structure of bucket scale, it can directly calibrate the weights, calculate the actual discharge volume by testing the weight of each moment of the weighing hopper, and then make closed-loop adjustments, so as to achieve high control accuracy, it is a kind of weighing and batching equipment with intermittent feeding and continuous discharging, because the loss control is carried out in the hopper, and the structure is easy to be sealed, it is a big improvement in the control of powder material compared with that of the spiral weigher. It is a big improvement. A computer can be used to control a number of dosage scales, can enter the relevant parameters, formulas, but also on the output, raw material consumption statistics, not only to ensure the accuracy of the control, but also to improve the management level of the factory, so that the factory can have a greater advantage in the competition.
Automatic Batching system is based on controlled weight loss, when the weight is less than the upper weight limit and greater than the lower weight limit, it is in weightless batching state, the weight loss per unit time is equal to the actual discharging flow rate, comparing the actual discharging flow rate with the set flow rate to get the difference, and then adjusting the amplitude of vibrating discharger in time, so as to make the discharging volume constant. When the measuring hopper material down to the lower limit of weight, the control system in the case of maintaining the discharge rate is unchanged, the discharger will be switched to volumetric discharge state, the controller output signal is a loss-in-weight feeding state of the constant value of the start of the charging equipment, charging equipment, the material into the measuring hopper, when the measuring hopper material reaches a certain weight, that is, to stop charging, at this time, measuring and control instrumentation to weigh accurately, and according to the set flow rate Open the vibrating discharger to discharge the material, and enter the state of loss-in-weight dosage again, and the loss-in-weight dosage and volumetric dosage work alternately.
The feeding system adopts various filtering techniques, with unique digital filtering function and high quality noise filtering function, which can get stable weight value. Programmable switching inputs, switching outputs, user programmable to receive inputs and commands from other devices, such as equipment start/stop, alarm inputs. User programmable output of various switching signals to provide various information or trigger various auxiliary devices, multi-level password protection provides users with different levels of changeable password protection. Super anti-interference ability, the surrounding noise and other sources of interference, in the design of this made full consideration, has a super anti-noise or other interference ability, humanized human-computer interface, the use of high-brightness fluorescent display screen VFD Chinese menu animation prompts, you can choose a variety of weighing interfaces, the use of the operation is more convenient.