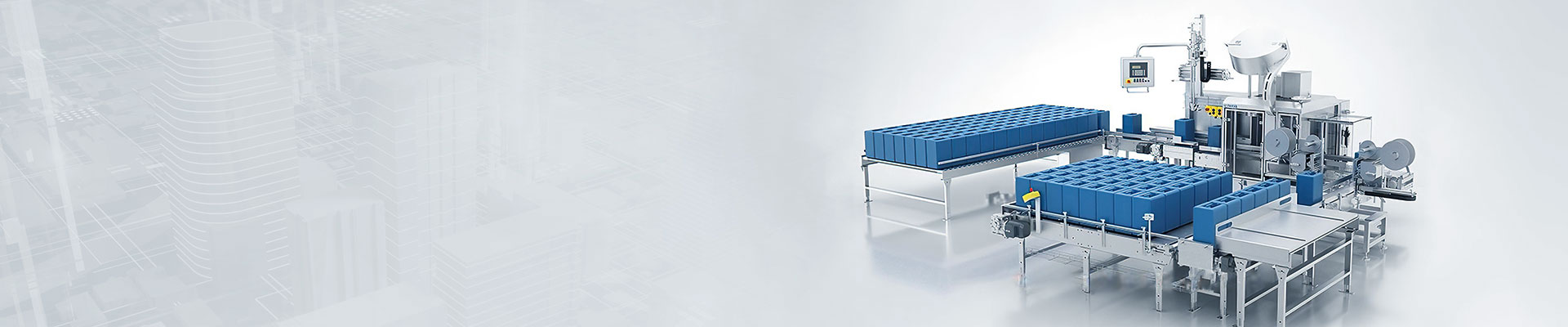
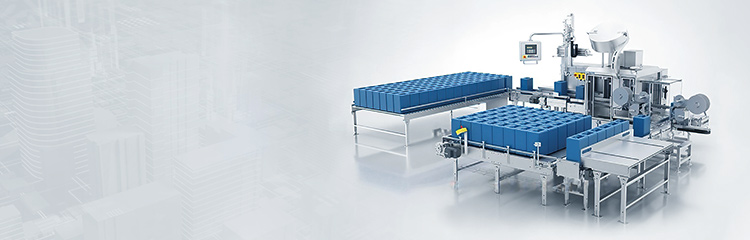
The liquid filling machine is controlled, self-corrected and statistically accomplished by an electronic scale and the filling gun has programmable positioning adapted to the product characteristics. It consists of filling gun, filling barrel, synchronized motor, rodless cylinder and roller arm. The correctness of the execution of the automatic filling machine is ensured by means of checking and confirming the command information of the feeding process, the filling process, and the constraints of material and container code identification.

The automatic Filling machine calculates the control quantity according to the weight deviation by using proportional, integral and differential, and adjusts the feeding quantity by adjusting the motor speed through the frequency converter to make it equal to the set value and complete the automatic filling process. The computer is connected to the weighing instrument through serial communication, which can collect and process the data in real time, input and save the data on the production line.
The metering filling machine completes 9 steps in sequence: barrel filling, barrel feeding, feeding, filling, barrel discharging, capping, sealing, stacking and so on. During normal operation, when the external signals such as interlock switch closure, air pressure condition, liquid level condition and so on are satisfied and normal, it is in the automatic operation mode after pressing the start switch, and each station on the filling line should be scanned cyclically according to the program programmed by the weighing instrument.
Liquid filling machine through the RS485 network can communicate with the control host, the use of multiple modules can be easily composed of RS485 distributed control system network, each network can be connected to a maximum of 255 modules, the network can be connected to the control computer through the RS232/RS485 conversion.
Basic parameters:
Maximum weighing capacity: 300kg
Minimum Sensitivity: 0.1kg
Filling error: ±0.1-0.2kg
Filling speed: about 50-80 barrels/hour
Control mode: 2-speed control
Filling method: Insertion, liquid level up
Gun head line: Teflon gun head, valve + Teflon hose
Structure material: host SUS304 stainless steel, conveying palletizing carbon steel anticorrosion paint.
Weighing platform size: 800 × 800mm (304 stainless steel power raceway)
Empty barrel raceway: 800mm × 2500mm (304 stainless steel power raceway) with another 1200mm slope without power roller
Heavy drum raceway: 800mm×2500mm (304 stainless steel power raceway, 2 sets)
Separate barrel device: for 200L barrels, carbon steel anticorrosive paint structure, 304 stainless steel raceway.
Palletizing equipment: pan-transfer type, suitable for pallets 1200×1200×140mm, including supplying pallets, palletizing, and lower pallet conveying.
Pipe pressure: 0.2-0.6MPa (related to material properties).
Material interface: DN40 flange connector 4, according to the user to provide interface standards
Air Connection: User supplied 12mm air hose connector for quick coupling connection
Power supply: AC220/50Hz (user-supplied to one side of the machine)
Using air source: 0.4-0.8Mpa (provided by the user to the side of the machine)
Use temperature: -10℃-50℃
Base condition: Ammonia solution flat solid concrete floor, concrete thickness should be more than 10cm.
Optional models: standard, explosion-proof filling