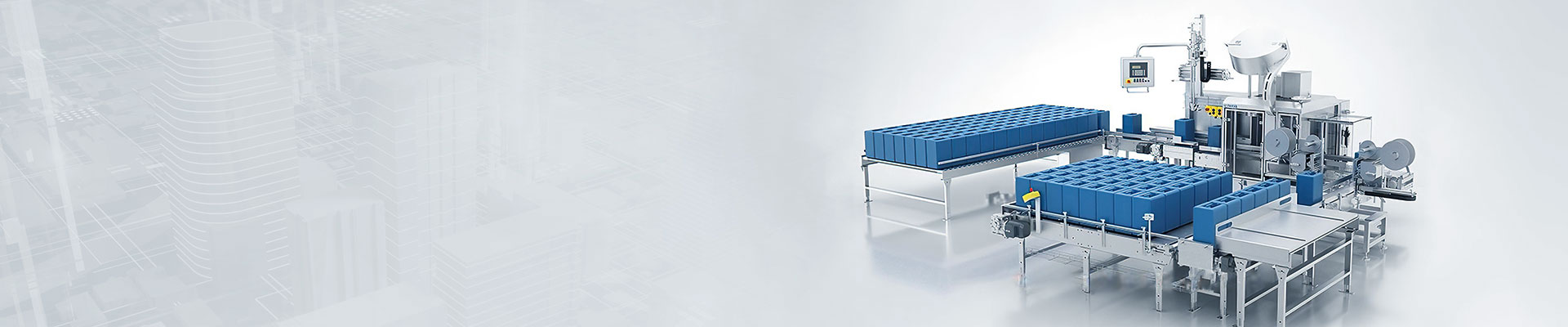
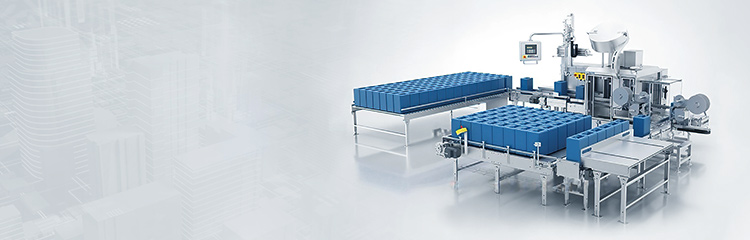
The weighing and filling machine adopts computerized automatic control of weighing, double-speed filling (fast filling at the beginning and slow filling when the electronic scale is close to the target amount) to ensure the filling accuracy, and adopts automatic quantitative filling to control the filling operation of raw materials in barrels. The automatic filling machine is a comprehensive automatic filling control system integrating computerized production process control and data management with weighing and filling, filling control and discharge. Air source interface: User provides 12mm gas pipe connector for quick connector connection

Weighing and Filling machine consists of industrial control machine, cylinder actuator and weighing module, mainly used for monitoring the assembly line process device and related data management and filling to ensure that the equipment to complete the expected operation, its main function is to achieve accurate measurement of the product material, and by the heating mechanism, automatic capping mechanism, transmission mechanism, and other units of the composition of the automatic filling machine is mainly to complete the product packaging, coding and printing, finished product transportation, etc. The PLC control system is the main tool for the coordinated management of the three main components of the full liquid filling scale, and its role depends on the fully automatic Filling system.
Automatic filling machine in the system before the operation of the first to determine whether it is in operation or calibration state, when the system is in the calibration state can be based on the standard of the processed products on the relevant instrumentation for the functional parameters set and the specific more scale, when the system is in operation to complete the self-test and analysis of the working state, self-test is mainly for the Feeder mechanism, gas system, etc., the working state analysis first of all, the system should be restored to the initialization process. Repeat the system to run a new open operation until the cycle of the program heavy metering bucket of material all unloaded, in the metering bucket to achieve the tare weight, the cycle of the program to prepare for the work, in the process pay attention to detect the relevant instrumentation whether there is an error, if there is an error in the instrumentation to be issued in a timely manner to send out an alarm for immediate repairs.
In determining the instrumentation and other filling equipment without problems after the manual and automatic state determination, if in the dry manual state can be directly operated manually, if the judgment outside the automatic state, the use of cyclic procedures to achieve the system of coarse and fine material machine feeding at the same time, in the material weighed to reach the standard set in advance of the coarse feed stops until the weighing to reach the end of the value of the fine feed also stops at this time should pay attention to the instrumentation stabilization of the measurement of the hopper door to allow discharging. Can be allowed to discharge, due to the process of unloading measurement will not be affected by the order of the measuring hopper, so when the packaging machine issued a working signal, any scale can be unloaded directly, and in order to avoid multiple scales in the process of simultaneous unloading of materials affecting the weighing of materials, to implement the "unloading interlock", "that is, one end of the scale unloading, the other end of the scale to stop unloading, when a number of scales to complete the simultaneous filling of the material work to be in accordance with the programmed sequence of unloading. When several scales finish filling at the same time, they should be unloaded one by one according to the programmed order.
Filling system for the realization of instrumentation and PLC and the host computer communication connection, can use the RS485 bus type to achieve the connection with the host computer COMI port, PLC internal settings of RS232 to be connected with the host computer COM2, in order to achieve the instrumentation and PLC and the host computer operation state is consistent with the use of half-duplex point-to-point transmission as a form of communication, when it is far away from the use of the converter to the RS232 and RS485 levels can be converted when the distance is long, and the data register can be utilized to assist in the transmission of the special state of the transmission data.
Basic parameters:
Maximum weighing capacity: 1000kg
Minimum Sensitivity: 0.2kg
Filling error: ±0.2-0.5kg
Filling speed: about 50-80 barrels/hour
Control mode: 2-speed control
Filling method: Insertion, liquid level up
Gun head line: Teflon gun head, valve + Teflon hose
Structure material: host SUS304 stainless steel, conveying palletizing carbon steel anticorrosion paint.
Weighing platform size: 120×1200mm (304 stainless steel power raceway)
Empty barrel raceway: 120mm × 2500mm (304 stainless steel power raceway) with another 1200mm slope without power roller
Heavy drum raceway: 1200mm×2500mm (304 stainless steel power raceway, 2 sets)
Separate barrel device: for 200L barrels, carbon steel anticorrosive paint structure, 304 stainless steel raceway.
Palletizing equipment: pan-transfer type, suitable for pallets 1200×1200×140mm, including supplying pallets, palletizing, and lower pallet conveying.
Pipe pressure: 0.2-0.6MPa (related to material properties).
Material interface: DN40 flange connector 4, according to the user to provide interface standards
Air source interface: User provides 12mm gas pipe connector for quick connector connection
Power supply: AC220/50Hz (user-supplied to one side of the machine)
Using air source: 0.4-0.8Mpa (provided by the user to the side of the machine)
Use temperature: -10℃-50℃
Basic conditions: solid concrete floor, concrete thickness should be more than 10cm.
optional models: standard, explosion-proof filling