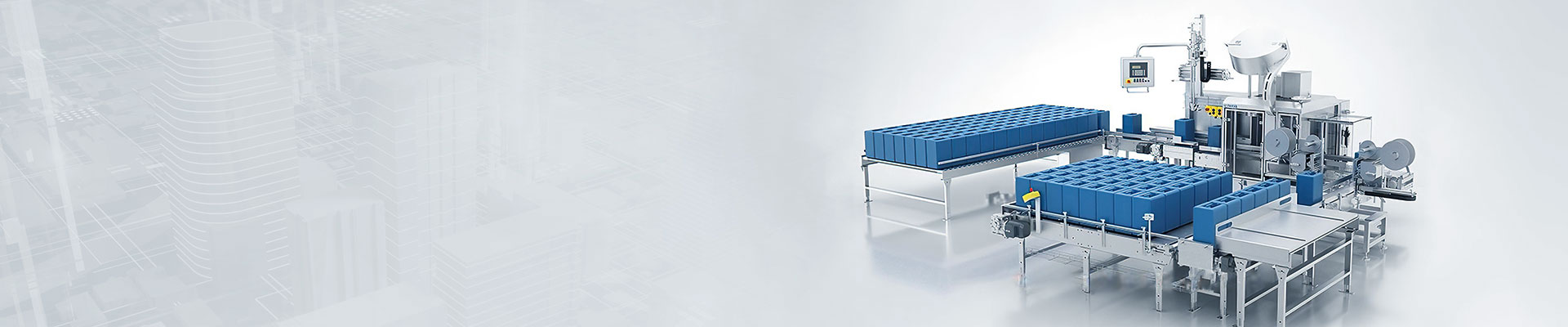
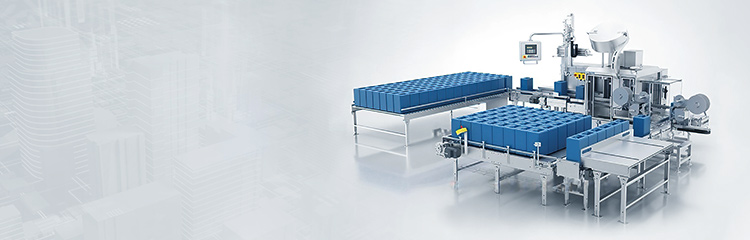
Automatic filling machine adopts new carbon dioxide blowing process, reduce carbon dioxide consumption, reduce oxygen pickup, filling display material amount, operation status, various alarm instructions, each filling amount, according to the process requirements of uniform settings, can be collected and processed by each filling control circuit to weighing signals and switching status, to realize the entire filling system feeding, weighing and detection, material adjustment, selection and switching of containers, such as dosing Automatic control of the process.

Automatic Filling machine adopts high reliability Siemens PLCS7-300 control system as the main automation facilities for on-site data collection loop control, sequential control operation and arithmetic to realize the Filling system operation diagnosis, real-time monitoring, automatic control, etc. to satisfy the requirements of real-time, stability and reliability of the system. The touch screen configuration adopts intelligent multi-function faceplate, man-machine operation interface is simple and suitable for the configuration is applicable and easy to modify, realizing the complete man-machine dialogue state.
Filling system and PLC control system can be through the RS-422/485 interface can be fast communication and setup. The entire control system outsider's input analog signals (AD has various probes of the alarm signal pressure, weight, level, humidity, etc.; there are all the buttons switching volume and cylinder switching volume signals (DIDO) and other signals. Filling weight control indicators are mainly to determine whether the initial weighing and double-checking weighing of the relevant indicators to meet the weighing requirements, the filling process of the storage tank and the intermediate tank level automatic adjustment, peripheral hand-held code scanner control design is also an important part of the control section. Filling machine configuration and external wiring part includes a can expand the analog input and output modules, its programmable controller with networking and communication capabilities of the switching input and switching output, you can use the PLC comes with the basic control unit design of its start and stop.
Basic parameters:
Maximum weighing capacity: 1000kg
Minimum Sensitivity: 0.2kg
Filling error: ±0.2-0.5kg
Filling speed: 1000L about 50-80 barrels/hour
Control mode: 2-speed control
Filling method: Insertion, liquid level up
Gun head line: Teflon gun head, valve + Teflon hose
Structure material: host SUS304 stainless steel, conveying palletizing carbon steel anticorrosion paint.
Weighing platform size: 1200×1200mm (304 stainless steel power raceway)
Empty barrel raceway: 1200mm × 2500mm (304 stainless steel power raceway) with another 1200mm slope without power roller
Heavy drum raceway: 1200mm×2500mm (304 stainless steel power raceway, 2 sets)
Separate drum device: for 1000L drums, carbon steel anticorrosive paint structure, 304 stainless steel raceway.
Palletizing equipment: pan-transfer type, suitable for pallets 1200×1200×140mm, including supplying pallets, palletizing, and lower pallet conveying.
Pipe pressure: 0.2-0.6MPa (related to material properties).
Material interface: DN40 flange connector 4, according to the user to provide interface standards
Air Connection: User supplied 12mm air hose connector for quick coupling connection
Power supply: AC220/50Hz (user-supplied to one side of the machine)
Using air source: 0.4-0.8Mpa (provided by the user to the side of the machine)
Use temperature: -10℃-50℃
Base condition: Coating agent flat solid concrete floor, concrete thickness should be more than 10cm.
Optional models: standard, explosion-proof filling