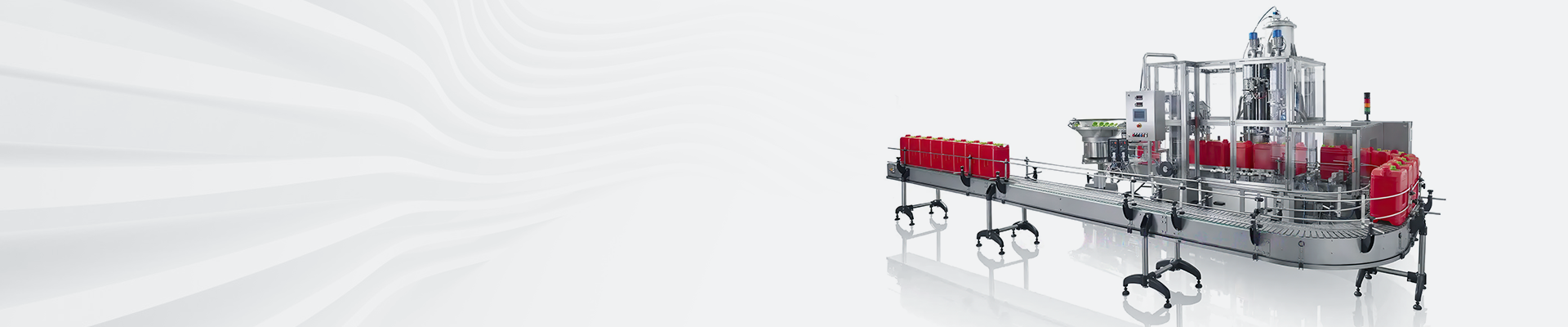
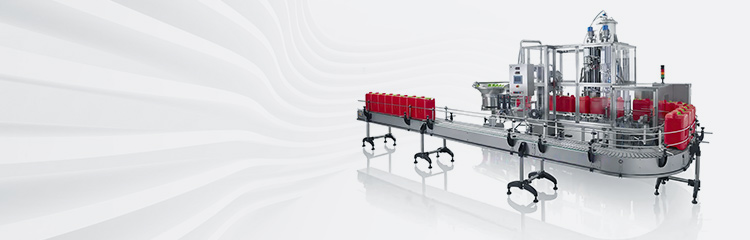

Summary:As a guarantee of consumer interests, the net content of prepackaged food has always been one of the focuses of regulatory authorities. How to reduce the loss as much as possible under the premise of complying with the relevant regulations reflects the management level of the enterprise. This paper introduces the factors that produce measurement errors in the packaging process of edible oil, such as mechanical accuracy, temperature of filling oil and the adjustment of production speed, and puts forward the relevant solutions according to these factors.
1 Introduction
In many industries filling machines are at the heart of automatic control systems in the process. There are many different ways to ensure the correct quantity of products during the packaging process: bulk metering of materials, bottling of liquids. The challenge for all of these processes is the same: a specified number of products must be included. If the filling amount is too low, this violates the EU Pre-packaging Directive 76/211 / EEC and the German Pre-Packaged Products Act (§22FPackV). These specify the percentage of production batches that are likely to fall below the specified minimum fill amount. "Weighing the incorrect filling amount of the filling machine" may result in penalties including suspension of production. Therefore, in the production process, manufacturers often take safe overfilling methods to exceed the minimum filling amount of packaging.
2. Relevant regulations on the packaging of edible fats
The current quantitative packaging measurement management regulations for the People's Republic of China State General Administration of Quality Inspection and Quarantine on January 1, 2006, the implementation of quantitative packaging Commodity measurement Supervision and management Measures.
3 Measurement control of edible oil filling production process
The density method is stipulated in the Measures for the Supervision and Administration of Quantitative Packaging Commodities. However, in the actual production site, the problems of constant temperature, precision measuring instrument (density cup or density instrument), high testing technology and relatively long testing time make the implementation of this method more difficult. Generally in the production site, the weight is used to control, and the actual density measurement and calculation are completed in the laboratory.
In the actual production process of measurement control, in order to ensure that the requirements of the "Quantitative Packaging Commodity measurement supervision and Management Measures" are met, a standard value is generally calculated for the filling production of products, on this basis, according to the performance of the equipment to set a higher than the standard value of the control baseline and deviation range, and according to the density/specific gravity of the test will be converted into a weight range; Operation site, through the electronic weighing, testing the actual weight is in the control range of the method to achieve field control.
Liquid filling machine adopts high speed A/D chip and anti-vibration technology, servo motor drives double screw transmission mechanism, PLC programming control touch screen operation control. The filling method is submersible, which can effectively reduce the generation of foam, and the automatic filling machine can meet the filling of materials with different characteristics. A residual drip collection tank controlled by an independent cylinder is installed under the filling head to ensure that the liquid does not drip out of the bottle mouth after the filling head is closed. Double (single) speed filling method selection, liquid drop automatic correction, always track the target value. The filling result is out of tolerance alarm, the tare value of empty drum is automatically recognized before filling, the filling is rejected beyond the range, and the electronic scale measurement avoids human error. With the adjustable variable speed filling function, it can reduce the foam generation of the foaming material during filling and prevent the bottle mouth pollution caused by the overflow of the material. When the filling of each barrel is completed, the prompt is displayed, and the weight and number of times are accumulated, and the data can be output by an external printer. With control system manual and automatic (micro-switch control) function Quantitative filling machine can be used in dangerous areas of automatic pressing (rotating) capping machine (optional).
4 Measurement errors and solutions
The measurement error in the production process of the edible oil automatic filling machine includes the error in the filling production (hereinafter referred to as the "production error") and the on-site weighing error. The measurement errors in the filling process of edible oil mainly include the errors caused by the mechanical accuracy of the equipment, the temperature change of the filling oil, the errors caused by the adjustment of the production speed and the opening and stopping of the production.
4.1 Accuracy of filling machine
The accuracy of liquid filling machine mainly refers to the repeatability and stability of its filling volume, which can reduce the error of this part by selecting equipment with excellent quality performance. At the same time, the precision of the filling machine is a key factor in setting the control reference line, which determines the difference between the control reference line and the standard value and the size of the deviation range.
4.2 Error caused by temperature change of canned oil
4.2.1 Factors of temperature change
Due to the influence of climate and other related factors, in the actual continuous production, the temperature of the filling oil will have a certain change. This change in temperature is mainly related to two factors.
① Temperature difference of outdoor large oil tank
The temperature difference between the upper and lower layers of the oil tank can reach about 4℃ (the upper layer is higher than the lower layer). In winter, due to the action of geothermal, this phenomenon is just the opposite, and the temperature difference between the upper and lower layers of the oil tank can reach about 2 ° C (the lower layer is higher than the upper layer). This temperature change is relatively gentle for filling production and is not obvious in a relatively short period of time. Generally, it can be controlled by weighing and testing the packaged products within a certain period and adjusting the filling equipment according to the test results.
② Temperature difference of oil pipeline
In the case of a long outdoor pipeline, the temperature of the liquid in the pipeline may rise due to the action of sunlight. In the normal operation of the filling machine, due to the flow of oil in the oil pipeline, this impact will not be very large, and the temperature of the oil entering the canning equipment will not be affected. However, for enterprises that are not continuous production (such as enterprises that have a long lunch break at noon), the oil in the outdoor pipeline may reach a higher temperature due to the exposure of the hot sun. According to the test, this temperature rise can reach up to (10~20)℃. For this temperature situation, it can be solved by increasing insulation or using underground pipelines.
4.2.2 Filling measurement error caused by temperature change
According to relevant reports, if the temperature changes by 1 ° C, the corresponding change of 5L grease is about 3.2ml(or 3g), that is, when filling the weighing filling machine without temperature compensation, if the temperature rises by 1 ° C, the corresponding filling volume is reduced by about 3.2ml(or 3g); Conversely, if the temperature drops by 1 ° C, the corresponding filling volume increases by about 3.2ml(or 3g).
4.3 Errors caused by production speed adjustment
Due to the high viscosity of the oil and the poor fluidity relative to water, 3, therefore, the actual filling operation cycle of the filling machine generally includes two processes of "filling" and "drip drying"; At the same time, in the operation process of "drip drying", taking into account the filling speed of the metering filling machine, "drip drying" is not a complete "drip drying" in the true sense, but "drip" to a degree that can be relatively acceptable and does not affect the operation. At this time, through the measurement control of the product after filling, the net content of the final product can be guaranteed to reach the controlled range; However, when we adjust the speed of the filling machine, the time consumed by the "filling" process during the filling cycle does not change, and the corresponding change is the time consumed by the "drip dry", resulting in a change in the amount of grease that drops into the packaging bottle. This change in the speed adjustment change is not large, the impact will not be great. In order to solve the resulting measurement error, when adjusting the production speed, strengthen the measurement sampling of filling products to ensure that the resulting measurement error is within the control range; When driving after a temporary stop, perform the necessary tests on the first filling of the product.
4.4 On-site weighing error
The on-site weighing error is mainly caused by the accuracy of the electronic scale and the on-site level adjustment of the electronic scale. For example, the general control of the weighing below 5L is best equipped with an electronic scale with a resolution of 1g, and at the same time, pay attention to the adjustment of the level of the electronic scale and other measures to control it. It is necessary to control the measurement error of edible oil filling process in the production process, understand the causes of its formation, and through certain means and measures can be effectively controlled, which is not only in line with relevant laws and regulations, to protect the interests of consumers, but also to ensure the interests of enterprises, reduce losses and improve economic benefits.