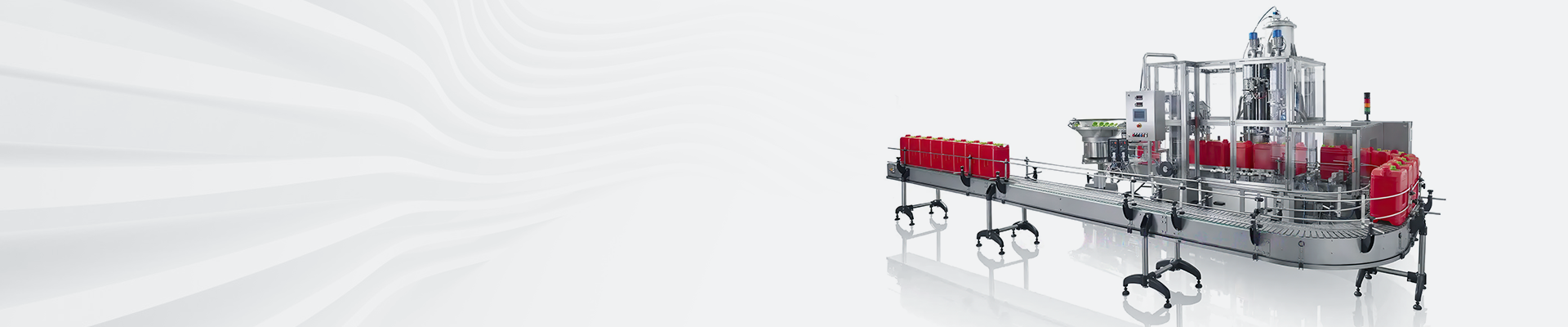
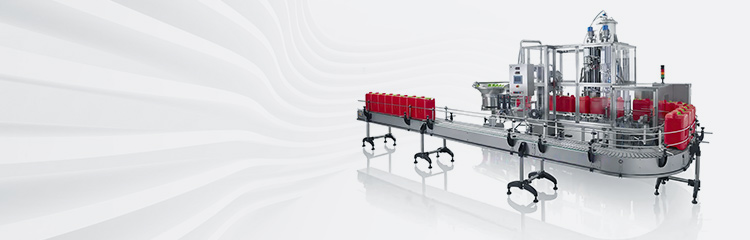

Summary:Pneumatic conveying system transports fly ash in pipeline by means of pressure equipment (positive pressure or negative pressure). The whole pneumatic conveying system is very simple. During operation, only the compressed gas source, the feeding device, the transportation pipeline and the receiver with the function of separating gas from materials are needed, so that automatic control can be realized through the system, and the material conveying capacity can be continuously monitored to monitor the input and output of the factory. The main components are material level gauge and pneumatic actuators, electric air lock, material delivery equipment, dry ash concentration equipment, dust collection equipment, air source equipment, air drying device, ash removal pipeline, storage bottom equipment, etc.
Pneumatic conveying began in 1870, in recent years, pneumatic conveying has become one of the important ways of production automation conveyor, and is widely used in electric power, metallurgy, chemical industry, building materials, food, food and other industries. Pneumatic conveying has many advantages compared with other mechanical conveying methods, such as: high production efficiency, simple equipment structure, easy to manage, high degree of mechanization, continuous work process, labor saving, easy loading and unloading. Based on the high requirements of pneumatic conveying automation, the reliability of the dosing control system hardware and software requirements are increased accordingly, the excellent control characteristics of the automatic control system and the perfection of the control function, to realize the automation of pneumatic conveying and management of intelligent, improve the conveying efficiency, prolong the service life and energy saving, etc., have a direct impact and practical significance. The paper analyzes and researches the automatic control system of pneumatic ash removal in the electric power industry as an example.
1 Overview of pneumatic conveying and control requirements
1.1 Pneumatic conveying basic mode and system composition
Power industry pneumatic ash removal is a kind of air as a carrier, with the help of pressure equipment (positive or negative pressure) in the pipeline transportation of fly ash method. The whole pneumatic conveying has the system is very simple, operation only need compressed gas source, feeding device, transportation pipeline, with the role of separating the gas and material receiver, can be realized through the system to automatically control, and can continue to monitor the amount of material delivery, the implementation of monitoring the plant input and output volume. The main components are material level meter and pneumatic actuator, electric air locker, material sending equipment, dry ash concentration equipment, dust collection equipment, gas source equipment, air drying device, ash removal pipeline, bottom of the reservoir equipment and so on.
1.2 Control requirements of pneumatic conveying system
The design of the ash removal system for a furnace ash removal and conveying system, in the normal operation of the boiler, fly ash deposited in the ash hopper, the ash hopper under the proposed installation of three warehouse pumps, and then through an ash conveying pipeline to the ash warehouse.
The initial state of the silo pumps is that the valves are closed. In the feeding process, the counterbalance valve is opened so that air can be discharged from the pumps, while the discharge valve on the pipeline is closed to prevent air from being sucked into the ash hopper. The inlet valve opens after the counterbalance valve, and the material falls into the bin pump by the natural action of gravity. When the silo pump shows that the pump is full of material (level meter is covered) or reaches the time set by the designer, close the feed valve and balancing valve, in this process need to go through a short time delay, that is, the valve closure action time. After the feed valve and balancing valve are closed, the air inlet valve will be opened to feed and pressurize the silo pump, and when pressurized to the set time or value, the discharge valve will be opened, and the compressed gas will be transported through the pipeline to transport the ash into the ash storage. After the material to the ash warehouse, the warehouse pump conveying link is over, the pressure in the pipeline will fall to a specific lower limit value, the inlet valve is closed, after a period of time delay, the remaining pressure in the pump is discharged, the discharge valve will be closed, ready to wait for the next cycle into the process.
2 System design process
2.1 Hardware system design
2.1.1 PLC selection
(1) The selected PLC must ensure that the controlled object control requirements;
(2) The use of PLC should not only be considered from the current situation, but also should be based on the long-term development needs, while meeting the two premises, and actively improve the cost-effectiveness of the entire system.
In the face of a variety of brands of different series and functions of PLC products, selection should be a comprehensive weighing of pros and cons, a reasonable choice to ensure that the function of the model to meet the system requirements, do not be greedy for the whole, to prevent an increase in the cost of investment and waste of resources. Generally in the selection of models should take into account the input / output points, storage capacity, I / O response time, as well as the characteristics of the output load selection, and the choice of online and offline programming.
According to the control requirements of the design and the actual situation, the programmable controller selected belongs to the small machine. Small programmable controllers are low cost and good performance, while the program capacity is large, easy to program, with fast speed and other advantages. According to the requirements of the pneumatic conveying system on the control, PLC needs to be in the environment of the more severe conditions of continuous operation, reliability. Taking into account the design of the control requirements and the actual situation, I chose the Japanese Mitsubishi Corporation's FX1 model programmable controller products. FX series PLC for the unit type, containing the CPU, power supply and fixed with the input / output. Input and output points within 128 points can be used FX1N series. At present, FX1N series PLC mainly has FX1N-24MR, FX1N-40MR and FX1N-60MR three kinds of CPU. the lowest grade is FX1N-24MR, its digital input points have 14 points, digital output points have 10 points, is the smallest control scale of the PLC, and FX1N-24MR digital input points have 24 points, and FX1N-24MR digital input points have 24 points, is the smallest control scale of the PLC.
2.1.2 Selection of other hardware devices
(1) Selection of buzzer: SFM series piezoelectric buzzer is an active buzzer, driven by the corresponding oscillation circuit to emit a variety of sounds, with light weight, long life, inexpensive and so on.
(2) Relay selection. According to the specific requirements of the system, the selection of JZ7 series of intermediate relays, which is used for AC 50Hz or 60Hz, voltage 500V or less and DC 200V or less in the control circuit, reference to its technical parameters, the various are in line with the design requirements, it is the selection of the JZ7-44 model intermediate relays.
(3) Pressure switch selection.
Pressure switch selection is YZX-150 model electric contact pressure vacuum gauge, accuracy level of 1.5, the maximum operating voltage of 220V DC, AC 380V, contact power of 10VA, Tianjin Instrumentation Factory.
(4) Contactor selection.
The contactor selected is CJ10 series AC contactor, which is suitable for starting and controlling AC motor.
2.2 Design of software system
Normally we have many ways to program the PLC control program, the following gives you a few typical programming methods.
(1) Graphical programming: as the name suggests, it relies on drawing graphics to carry out program design. Commonly, there are mainly ladder diagram method, logic flowchart method, timing flowchart method and step by step control method.
(2) empirical method of programming: the use of their own or other people's experience in programming design, you need to select the process requirements of similar programs, and then combined with their own engineering situation, the experimental program to modify accordingly, so that it is suitable for their work requirements.
(3) computer programming: the use of PLC programming software through computer technology to develop the design, such as offline form, online form programming, or online debugging, offline simulation. For example: Mitsubishi software is based on the Windows platform application software. This software can be used in a convenient way in the process of access or encryption, and finally form the EXE format running file.
3 Conclusion
Using PLC as the core controller of the system, the conveying efficiency is greatly improved to ensure the safe and reliable operation of the system, in the monitorable system, but also through the PLC communication interface, to the control system to transfer information to further realize the automation of the equipment, so that the maintenance and overhaul is convenient, and is welcomed by the users in the actual operation.