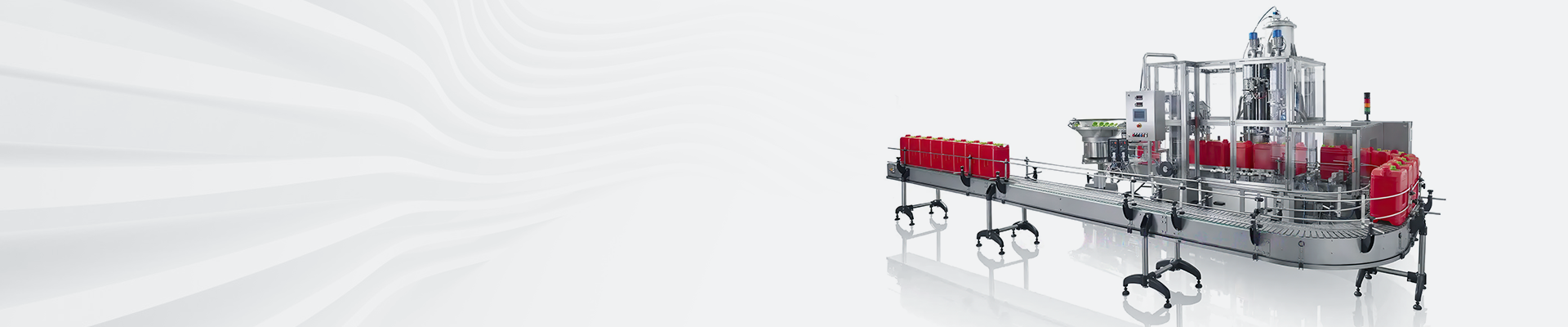
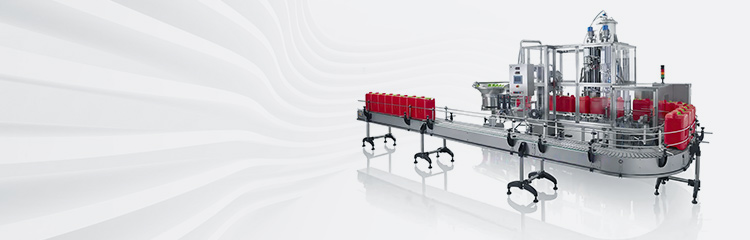

Summary:This paper introduces the principle, advantages and disadvantages of various alumina pneumatic feeding technology, and introduces the application of alumina pneumatic feeding technology in the transformation project of an alumina conveying system of Qinghai Branch of China Aluminum Industry.
1 Alumina pneumatic feeding technology introduction
Alumina pneumatic feeding system refers to the technology of conveying alumina materials by the flow of gas. It has good system sealing performance to prevent materials from moisture and debris entering; Small footprint; Simple operation and maintenance of the equipment. At present, there are four kinds of pneumatic feeding technology commonly used in electrolytic alumina, namely, dilute phase conveying, concentrated phase conveying, ultra-concentrated phase conveying, and air chute conveying.
Dilute phase transport
Thin phase conveying technology belongs to dynamic pressure conveying technology in pneumatic feeding. In the conveying process, the kinetic energy of the compressed air is transferred to the material to be transported, so that the material flows forward in a state of suspension or group suspension. When the particle concentration in the air stream is below 0.05m3 material /㎡ air, the transportation of the gas-solid mixing system becomes dilute phase transportation when the voidage E<0.95. Because it relies on kinetic energy conversion to transfer energy and transport suspended materials, the wind speed is high, and part of the energy will be lost in the energy transfer process, coupled with the friction loss between the suspended particles and the particles and the pipe wall, so the energy consumption is high. At the same time, due to the low ratio of solid gas in the pipeline, the pipeline wear is fast, and the damage of alumina is also relatively serious.
1.2 Dense phase transport
Dense phase transport is also known as dense phase transport. When the particle concentration in the air stream is above 0.2m3 material /m air, the transportation of gas-solid mixing system becomes dense phase transportation when the voidage E<0.80. The concentrated phase conveying system is driven by the static pressure generated by the specially structured system to transport the material. The dense phase conveying pipe is composed of an inner pipe and an outer pipe, and the inner pipe is provided with a small hole along a certain length. The material is transported in the outer pipe, and the material transported in the pipe is in the shape of a material column, which is moved by dynamic pressure in the conveying pipe. The inner tube is the key to dense phase conveying. The opening distance of the inner tube and the air velocity during conveying have great influence on the conveying process. The whole conveying process is carried out according to the principle of minimum resistance. Due to the low wind speed in the transportation process, its energy consumption is lower than that of dilute phase transportation, and the pipe wear and alumina damage rate are relatively low. However, the related equipment of the system is more complicated, and the maintenance workload is larger.
1.3 Air chute transport
Air inclined chute conveying is a fluidization conveying technology in gas conveying. The low pressure air enters the conveying layer from the air chamber of the chute through the partition plate, which makes the material in the chute fluidize and has the property of fluid. Due to the action of gravity, the fluid material produces a sliding force, overcomes the friction resistance of the material flow, and drives the material to flow forward. In the chute conveying, the low-pressure wind only plays the role of fluidizing the material, and is not responsible for promoting the flow of the material, so the wind pressure and wind speed are very low. The disadvantage of this technology is that there must be a slope, and the space requirements of the workshop are higher.
1.4 Ultra-dense phase transport
Ultra-dense phase transport is a widely used technology at present. The technology in the conveying process, first let the low-pressure wind through the distribution plate to flow the material in the chute, so that it has the nature of fluid, while the material column difference along the direction of transmission is established, when the material column difference generated by the driving force is enough to overcome the friction resistance of the fluid flow, the material begins to flow forward. In the ultra-dense phase conveying, in addition to completing the fluidization of the material, the low-pressure wind also promotes the material to establish a material column of different heights, but it is not responsible for directly promoting the material flow. The ultra-dense phase uses the pressure gradient generated by the delay resistance loss to complete the conveying work without additional energy. Therefore, in addition to the advantages of chute transportation, it also overcomes the disadvantages of the increase in civil construction costs caused by the inclined layout of the chute transportation.
2 Practical Application
The original alumina conveying system in an electrolytic branch plant of the company is a trolley loading system. At present, the equipment of the system is aging seriously, spare parts can not be supplied in time, and the maintenance work is difficult. When used, the plant materials fly, which not only causes the waste of raw materials, but also affects the production environment health, so the system has been reformed. The advantages and disadvantages of various pneumatic batching equipment are considered comprehensively in the reconstruction, and the advanced ultra-dense phase conveying technology combined with inclined chute conveying technology is finally selected. Because as a factory that has been used in production, its space structure has been very limited. The ultra-dense phase transportation technology can meet the space requirements, and the transportation efficiency is high and the energy consumption is low. At the same time, according to the company's previous transformation experience and considering the actual production situation, it is necessary to combine the inclined chute transportation technology to meet the production needs and achieve the smooth transportation of alumina. There are two main reasons for this:
(1) The company mainly uses domestic semi-sand granular alumina, which is transported by the two dilute phase conveying systems from the unloading station to the daily storage tank of the branch plant and the daily storage tank of the branch plant to the daily storage tank of the workshop, and then recycled into the purification system, which has been seriously damaged when it becomes fluorine-loaded alumina and becomes powdery alumina.
(2) After the use of carbon roasting flue gas purification, the alumina contains asphalt tar, the viscosity increases, and the fluidity is poor.
Due to the powder state of alumina and the mixture of asphalt tar, the material is not easy to be fluidized, and the alumina flow rate is too slow when it is concentrated into the electrolytic ultra-dense phase conveying system, and the alumina plate containing asphalt tar blocks the chute on the ventilated plate.
In addition, the viscosity of alumina material increases and the characteristics of non-fluidization also cause the transportation mechanism of ultra-dense phase transportation technology to be unable to be realized normally in production. The realization of ultra-dense phase transportation mainly depends on the balance of the material column on the chute to form the pressure difference of the material column to produce a pressure gradient, and then push the material forward. If the alumina material is bonded on the cloth bag of the balance material column due to the viscosity factor, the dense material column is formed, and the poor air permeability can not form the material column and pressure gradient required in theory, which further aggravate the alumina material deposition in the chute can not be smoothly transported. In order to solve the above problems, it is necessary to combine the chute technology with the ultra-dense phase technology. Tilt the chute as far as possible in a limited space, and the slope of the chute adds a gravity factor to the progress of the material. The addition of the gravity factor can effectively slow down the deposition of the material in the chute, reduce the resistance of the material forward, and greatly increase the fluency of the material forward. Secondly, the balance column made of canvas is no longer used on the chute, but replaced with steel pipe. The steel pipe is connected with the electrolytic exhaust pipe to collect dust. By calculating the pressure gradient, a regulating valve is arranged on the steel pipe. The friction resistance between the wall of the steel pipe and the alumina material is low, which reduces the possibility of the material sticking and blocking, and ensures the normal realization of the ultra-dense phase conveying mechanism.
3 Conclusion
The application of many advanced technologies actually requires certain auxiliary conditions to guarantee, and the production site is often not able to provide this ideal state, so it is necessary to take into account the special factors of the actual production in the application of some advanced technology, and comprehensive consideration of the advantages and disadvantages of various technologies can achieve good results.