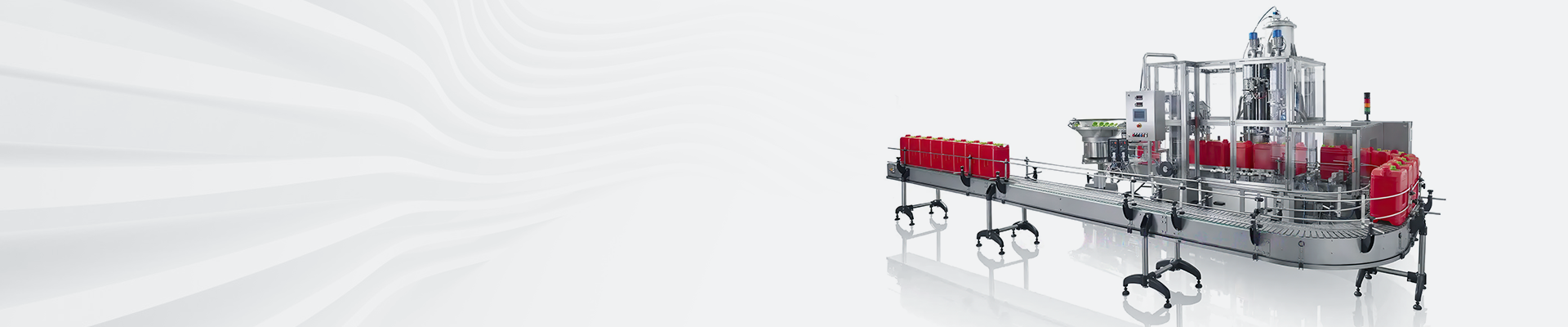
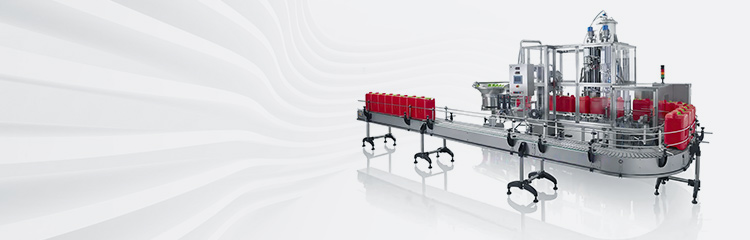
摘要:各种氧化铝气力投料技术的原理和优缺点,并结合实际介绍了氧化铝气力投料技术在中国铝业青海分公司一氧化铝输送系统改造项目中的应用。
1氧化铝气力投料技术介绍
氧化铝气力投料系统是指利用气体的流动对氧化铝物料进行输送的技术。它具有系统封闭性能好,防止物料受潮和杂物进入;占地面积小;设备操作维修简单等优点。目前电解氧化铝气力投料技术常用的有4种,即稀相输送、浓相输送、超浓相输送、空气斜槽输送。
稀相输送
稀相输送技术属于气力投料中的动压输送技术。在输送过程中压缩空气的动能传递给被输送的物料,使物料以悬浮或集团悬浮的状态向前流动。当气流中颗粒浓度在0.05m3料/㎡空气以下,气固混合系统的空隙率E<0.95时的输送成为稀相输送。由于是靠动能转换传递能量,输送悬浮态物料,要求风速较高,在能量传递过程中会损失部分能量,加上悬浮颗粒间及颗粒与管壁间的摩擦损失,因此能耗高。同时由于输送管道中固气比低,管道磨损快,氧化铝破损也比较严重。
1.2浓相输送
浓相输送又称密相输送。当气流中颗粒浓度在0.2m3料/m空气以上,气固混合系统的空隙率E<0.80时的输送成为浓相输送。浓相输送系统就是由特殊结构的系统产生的静压力推动料栓输送物料的。浓相输送管道由内管和外管配合组成,并在内管上沿一定长度开有小孔。外管中走物料,管内输送物料呈料柱型,在输送管道中受动压作用而移动的。采用内管是浓相输送的关键,内管的开口距离和输送过程中的气流速度对输送过程影响极大,整个输送过程依据最小阻力原理进行输送。由于输送过程风速低,其能耗比稀相输送低,管道磨损及氧化铝破损率都相对较低。但该系统的相关配套设备较复杂,维修工作量较大。
1.3空气斜槽输送
空气斜溜槽输送是气体输送中的流态化输送技术。低压风从溜槽风室通过分隔板,进入输送层使溜槽内物料流态化,具有流体的性质。流态化后的物料由于重力作用,产生下滑分力,克服物料流动的摩擦阻力,带动物料向前流动。在溜槽输送中低压风只起到使物料流态化作用,不负责推动物料流动,因此需要风压、风速都很低。该技术的缺点是必须要有斜度,对厂房的空间要求较高。
1.4超浓相输送
超浓相输送是目前应用比较广泛的技术。该技术在输送过程中,首先让低压风通过分配板使溜槽内物料流态化,使其具有流体的性质,同时沿输送方向建立起料柱差,当料柱差产生的推动力足以克服流体流动的摩擦阻力时,则物料开始向前流动。在超浓相输送中低压风除完成物料流态化外,还促使物料建立不同高度的料柱,但不负责直接推动物料流动的工作,超浓相是利用延程阻力损失产生的压力梯度完成输送工作,不额外增加能量。因此,除具有溜槽输送的优点外,它还克服了溜槽输送倾斜布置所带来的土建费用增加的缺点。
2实际应用
公司一电解分厂厂房内原有的氧化铝输送系统为小车上料系统。该系统目前设备老化严重,备品备件无法及时供应,维修工作困难。使用时厂房物料飞扬,既造成原料的浪费,又影响生产环境卫生,所以对该系统进行了设备改造。改造时综合考虑了各种气力配料设备的优缺点,最终选择了目前比较先进的超浓相输送技术并结合斜溜槽输送技术。因为作为已经在生产中使用的厂房,其空间结构已十分有限。而超浓相输送技术能够满足这种空间要求,且输送效率高、能耗低。同时,根据公司曾经的改造经验,考虑生产实际情况,必须结合斜溜槽输送技术才能满足生产需求,实现氧化铝的流畅输送。其主要原因有两点:
(1)公司使用的主要是国产半砂粒状氧化铝,经过卸料站至分厂级日用贮槽以及分厂级日用贮槽至车间日用贮槽的两次稀相输送系统倒运,再次进人净化系统循环,成为载氟氧化铝时已经严重破损,变成粉状氧化铝。
(2)炭素焙烧烟气净化使用过后氧化铝含沥青焦油,粘度增加,流动性差。
由于氧化铝的粉面状态和沥青焦油的混入导致物料不易被流态化,集中进入电解超浓相输送系统时会出现氧化铝流速过慢的现象,严重时含沥青焦油的氧化铝板结在透气板上堵塞溜槽。
此外氧化铝物料黏度增加,不易流态化的特性也造成超浓相输送技术的输送机理无法在生产中正常实现。超浓相输送的实现主要靠溜槽上的平衡料柱形成料柱的压力差产生压力梯度,进而推送物料前进。如果氧化铝物料由于黏度因素粘结在平衡料柱的布袋上,形成密实的物料柱体,极差的透气性能无法形成理论上所要求的料柱和压力梯度,进一步加剧氧化铝物料沉积于溜槽中无法顺畅输送。要解决上述问题必须将斜槽技术和超浓相技术结合起来使用。在有限的空间尽量将溜槽倾斜,溜槽的倾斜使得物料的前进添加了重力因素。重力因素的加入可有效减缓物料在溜槽中的沉积,物料前进的阻力减小,大大增加了物料前进的流畅性。其次,在溜槽上不再采用帆布制作的平衡料柱,而是用钢管替换。钢管与电解排烟道连接,起到收尘作用。通过对压力梯度的计算要求,在钢管上设置调节阀门。钢管的管壁与氧化铝物料的摩擦阻力较低,减小了物料粘结堵塞的可能性,保证超浓相输送机理的正常实现。
3结语
许多先进技术的应用其实需要一定辅助条件作保证,而生产现场往往并不能够提供这种理想状态,所以在应用某种先进技术时务必要考虑到生产实际的特殊因素,综合考虑各种技术的利弊可取得良好的效果。