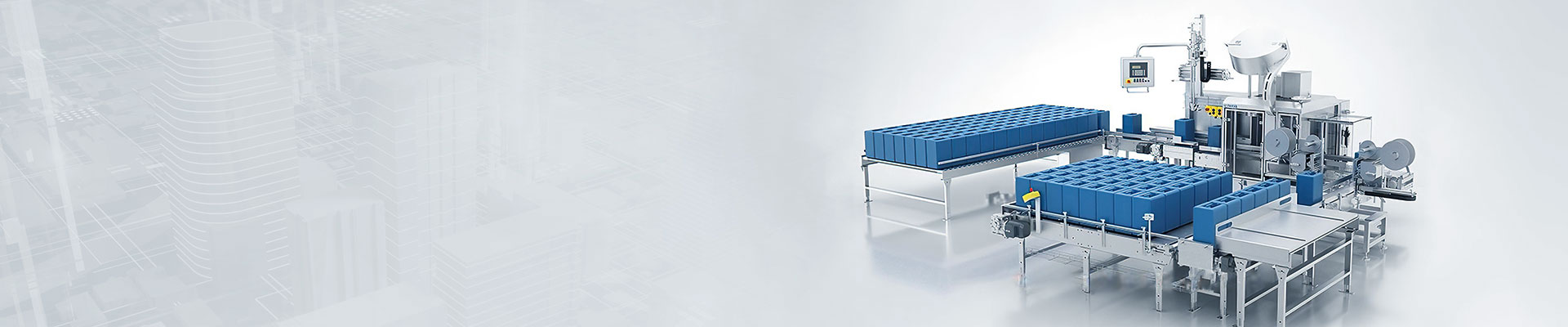
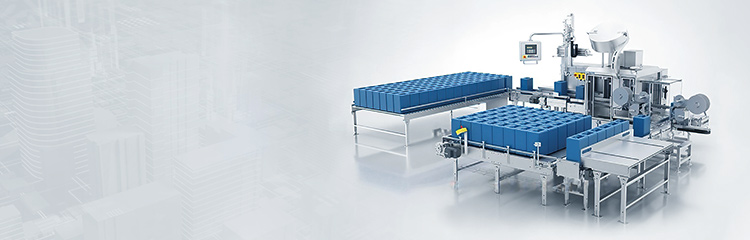
Liquid canning machine adopts configuration software to monitor the interface design, can quickly component and generate the upper computer monitoring system, through the screen real-time display of the current filling quality, filling barrels and other field work status, the upper computer can carry out the corresponding operation, through the interface for the choice of filling mode and start, stop and other buttons operation. It can change the filling quality and number of barrels and manually remove the tare weight (i.e., the quality of the filling barrels) when using different filling barrels.

Automatic Filling machine using Mitsubishi inverter is a high-performance inverter using flux vector control technology, pulse width modulation (PWM) principle and intelligent power module. The main content of the software design is the preparation of PLC programmable controller. In order to ensure that the filling process of the various parts of the device action is accurate and reliable, it is necessary to control the various Weighing modules, relays, switches and solenoid valves through the PLC program.
Liquid filling machine is a kind of automatic filling equipment for automatic packaging of liquid, which is filled into the target container to be packaged by gravity, and then conveyed to the end through the conveyor belt, and then entered into the filling storage container, the first process is to clean the inner wall of the empty bottles, and open the flushing mechanism through the solenoid valve to fill the bottles with water at high pressure, and then after a certain delay; the rotary body motor rotates, and then enters into the next station of drying/disinfection. / disinfection bit, drying motor operation to dry the empty bottle, and the use of high-temperature heaters for disinfection; and then into the next station for automatic weighing, filling, by gravity, the paste filling into the empty bottle; and then into the capping / labeling bit, the action is completed after the rejection of the next line, into the full bottle conveyor line, transported to the end of the carton robots to grab the full bottle of the paste to be boxed, so that a bottle is completed. This completes the processing of a bottle of cream.
Basic parameters:
Maximum weighing capacity: 30kg
Minimum Sensitivity: 0.01kg
Filling error: ±0.1-0.2kg
Filling speed: 20L about 150-180 barrels/hour
Control mode: 2-speed control
Filling method: Insertion, liquid level up
Gun head line: Teflon gun head, valve + Teflon hose
Structure material: host SUS304 stainless steel, conveying palletizing carbon steel anticorrosion paint.
Weighing platform size: 400 × 800mm (304 stainless steel power raceway)
Empty barrel raceway: 400mm × 2500mm (304 stainless steel power raceway) with another 1200mm slope without power roller
Heavy drum raceway: 400mm×2500mm (304 stainless steel power raceway, 2 sets)
Separate barrel device: for 200L barrels, carbon steel anticorrosive paint structure, 304 stainless steel raceway.
Palletizing equipment: pan-transfer type, suitable for pallets 1200×1200×140mm, including supplying pallets, palletizing, and lower pallet conveying.
Pipe pressure: 0.2-0.6MPa (related to material properties).
Material interface: DN40 flange connector 4, according to the user to provide interface standards
Air Connection: User supplied 12mm air hose connector for quick coupling connection
Power supply: AC220/50Hz (user-supplied to one side of the machine)
Using air source: 0.4-0.8Mpa (provided by the user to the side of the machine)
Use temperature: -10℃-50℃
Base condition: Horizontal solid concrete floor, concrete thickness should be more than 10cm.
Optional models: standard, explosion-proof filling scale