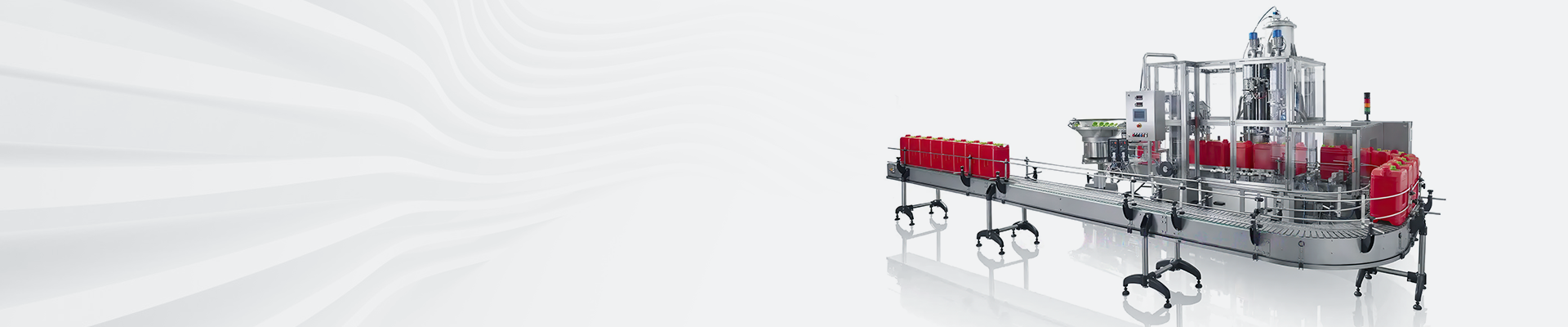
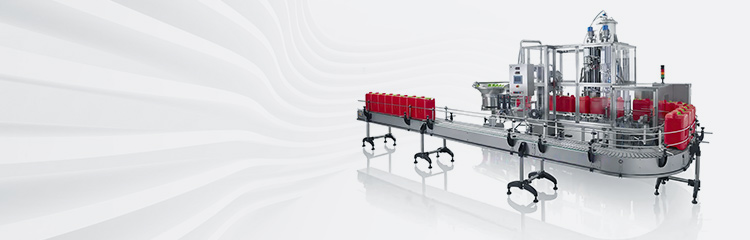

Summary:The automatic filling machine adopts the embedded real-time operating system uCOS-Ⅱ, which has a streamlined core and complete multi-task management functions. It regularly checks whether the content displayed on the LCD of the weighing instrument has been updated. If it is updated, it reads relevant messages, such as the weighing platform. Quality, clock, user buttons, etc. refresh the LCD screen.
The automatic filling machine adopts the embedded real-time operating system uCOS-Ⅱ with its streamlined kernel and perfect multitasking management functions. It regularly inquires whether the content displayed on the LCD of the weighing instrument has been updated, and if it has been updated, it reads the relevant messages, such as the quality of the weighing platform, the clock, and the user's keystrokes, etc., and refreshes the LCD screen. Periodically, it reads the messages generated by the various modules, such as the weighing module, the ZigBee communication module, the keyboard, the power supply module, etc., converts the messages, and distributes the processed messages to the corresponding peripherals. Keyboard scanning is also included in this task. Read the data from the weighing module and convert it into the corresponding quality message. The weighing module sends data every 100ms, this task is in blocking mode and waits for the mailbox message from the weighing module to be interrupted. Realize the function of sending and receiving data from ZigBee communication module, including sending filling information records, analyzing data and commands from base station. This task is executed after waiting for the mailbox message from the interrupt of ZigBee communication serial interface.USB processing task is responsible for reading and parsing the data file of USB storage device and writing the gas cylinder file information into Flash. This task is executed after waiting for the mailbox message from the USB interface interrupt.
The liquid filling machine also adopts CCS high-brightness low-angle LED array ring light source illumination, which can obtain high-contrast images and facilitate image segmentation processing. Automatic filling machine consists of an industrial camera, monochrome image capture card, high brightness low angle LED array ring light source, industrial control computer, driver, three coordinate workbench LabVIEW and IMAQVision development platform. Industrial camera CCD real-time ingestion detection of weighing module weighing platform to be detected on the image of the barrel, transmitted to the image acquisition card. After digital decoding, A/D conversion and other processing, it is transmitted to the computer memory for storage via PCI bus. The image processing program accesses the memory buffer that retains the image. Image signals are degraded during acquisition and transmission due to noise formed by environmental influences, electrical signal interference influences such as sensor parts, and imperfections in the transmission channel. For the noise in the digital image, such as Gaussian noise, pretzel noise, uniformly distributed noise, etc. to have noise reduction preprocessing. Image preprocessing improves the visual effect of the image, improves the clarity of the image, and makes it more conducive to computer arithmetic processing. The system uses a fast median filtering algorithm for signal noise reduction, and then image binarization for image segmentation. Compared with the similar low-pass linear filter, median filtering can filter out the point and coarse line noise in the image, remove the binary noise, impulse noise and particle noise, and attenuate the random noise without blurring the boundary, which is suitable for image processing. The position information of the circular filling port in the image of the barrel lid surface is obtained by calculation, namely, the radius of the filling port, the center of the filling port, and the height of the oil gun. Then, the corresponding position information is transmitted to the stepping motor control system, and the motor control system drives the X-Y-Z axis stepping motor according to the pulse instruction issued by the computer, driving the oil gun to run above the filling port to realize automatic positioning and filling.
Explosion-proof filling machine is equipped with a weighing module operating table, weighing system automatic empty bottle detection and above the filling valve, filling valve inlet connected to the inner cavity of the liquid storage peak through the connecting pipe. The liquid storage tank is located on the upper surface of the operating table, the outlet port of the filling valve is provided with a tie rod gun head, the fixed connection of the electric telescopic rod is connected to the other side of the upper surface of the filling valve structure, and the upper surface of the operating table is provided with a filling system corresponding to the filling structure. The upper surface of the operating table is provided with a PLC control system. Two conveyor wheels are rotationally connected by bearings between two fixed frames on the opposite bottom, and the two conveyor wheels are equipped with a conveyor belt. One end of one of the transfer wheels is fixedly connected to the output shaft of a servo motor fixed on the outside of the fixed frame, and the output end of the servo motor is electrically connected to the output end of the PLC controller. Fixed in the electric telescopic rod expansion and hose bottom connection plate connection plate bottom of the front side is provided with a filling head, the top of the filling head through the connection plate and connected with the bottom of the hose filling head supporting the electric fusion inter, the input end of the electromagnetic inter is electrically connected with the output end of the PLC controller. The base is located on the surface of the operating table. The upper surface of the base is equipped with ultrasonic sensors, ultrasonic sensors are located directly below the belt conveyor structure and correspond to the filling head, ultrasonic sensors and PLC controller bidirectional electrical connection. The empty bottle detection system is equipped with a laser displacement transmitter, and the laser displacement sensor is electrically connected to the PLC controller in both directions. Liquid filling machine can quickly and efficiently carry out automatic filling of liquids, PLC controller detection structure to realize automatic control and adjustment of filling volume. Through the belt conveyor structure and PLC controller can quickly and efficiently carry out the automatic filling of liquid.