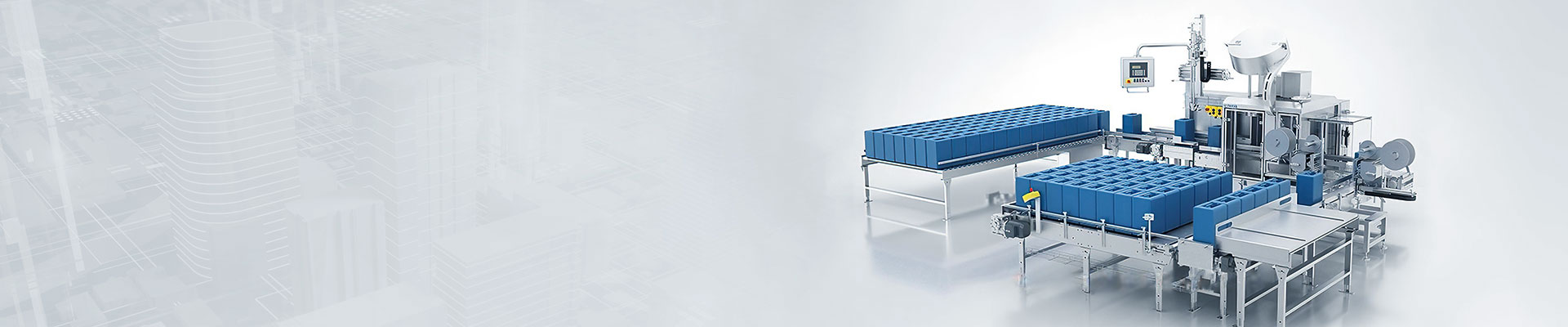
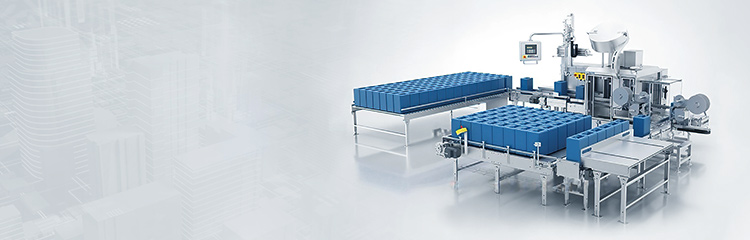
The metering and distribution machine realizes the control of fast, medium and slow valve closure, and the cylinder stroke is controlled by PLC signal to complete the actions of weighing, filling, opening, opening, closing and capping. When the weighing module reaches the given weight value, the opening cylinder returns to the filling valve and closes the opening cylinder to move to the given position, the opening cylinder moves upward, and the valve cover is installed. By driving a piston through the cylinder to draw and pump out the material, the flow direction of the material is controlled by the check valve, the stroke of the cylinder is controlled by the magnetic spring switch to adjust the filling amount, the weighing module is connected with the data line of the weighing instrument, and the pressure signal of the electronic scale is continuously transmitted to the weighing instrument during the measurement process, and the control instrument controls the pump and closes the pneumatic valve when the preset quantitative weight is reached.

Weighing and Filling machine is a kind of automatic filling equipment combining high precision weighing technology and advanced intelligent algorithm, which is composed of load cell control system and actuator. When the product is put onto the conveyor of the weighing machine, the load cell can accurately measure the weight of the product. Through the pre-set standard weight range control system can quickly determine whether the weight of the filling is qualified or not. If the weight of a product is not within the qualified range the control system will immediately trigger the action of the actuator to reject the defective product from the conveyor belt. The actuator can be a pneumatic device, robotic arm or other adaptable device to ensure the accuracy and efficiency of the reject process. The rejected defective product can be separated by another conveyor or other means for further processing or elimination in the filling line for the purpose of accurate filling.
The weighing and distributing machine consists of a programmable controller and Electronic scales to form a two-stage computer control network. The distribution system integrates automatic control technology, electronic scale metering technology, weighing module sensor technology, and computer management technology into an integrated mechatronic control system; it adopts an open control method, high compatibility, and an open database. The filling machine can be accessed to the factory LAN through Ethernet, which can realize the integration of management and control. It has the advantages of digital display of weight value, dynamic display of process screen, formula modification management, fast filling speed, high control accuracy, etc. It adopts the upper computer completely on-screen control system, with the functions of automatic storage of filling data, inquiry of list of filling process, and statistics and printing of class, day, month and year reports.
Basic parameters:
Maximum weighing capacity: 300kg
Minimum Sensitivity: 0.1kg
Filling error: ±0.1-0.2kg
Filling speed: about 50-80 barrels/hour
Control mode: 2-speed control
Filling method: Insertion, liquid level up
Gun head line: Teflon gun head, valve + Teflon hose
Structure material: host SUS304 stainless steel, conveying palletizing carbon steel anticorrosion paint.
Weighing platform size: 800 × 800mm (304 stainless steel power raceway)
Empty barrel raceway: 800mm × 2500mm (304 stainless steel power raceway) with another 1200mm slope without power roller
Heavy drum raceway: 800mm×2500mm (304 stainless steel power raceway, 2 sets)
Separate barrel device: for 200L barrels, carbon steel anticorrosive paint structure, 304 stainless steel raceway.
Palletizing equipment: pan-transfer type, suitable for pallets 1200×1200×140mm, including supplying pallets, palletizing, and lower pallet conveying.
Pipe pressure: 0.2-0.6MPa (related to material properties).
Material interface: DN40 flange connector 4, according to the user to provide interface standards
Air Connection: User supplied 12mm air hose connector for quick coupling connection
Power supply: AC220/50Hz (user-supplied to one side of the machine)
Using air source: 0.4-0.8Mpa (provided by the user to the side of the machine)
Use temperature: -10℃-50℃
Base condition: Ammonia solution flat solid concrete floor, concrete thickness should be more than 10cm.
Optional models: standard, explosion-proof filling