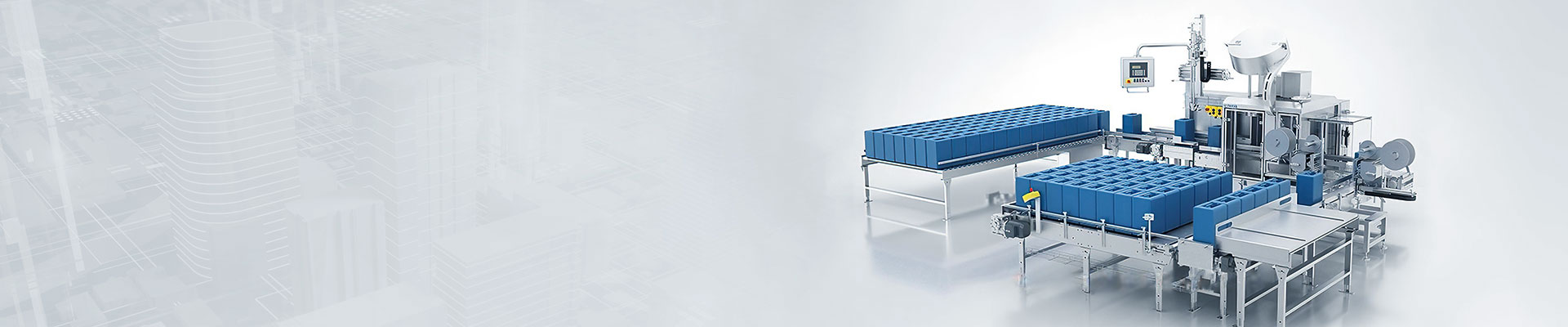
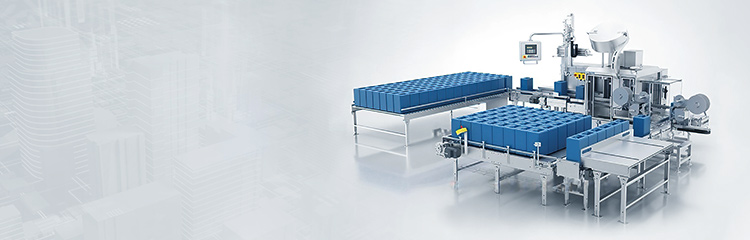
The weighing system of the reaction tank is transmitted to the central control room for centralized monitoring and management through high-speed network, and the host computer of the central control room also transmits control commands to the PLC measurement and control terminal through high-speed network to implement decentralized management of each unit. Integrating computer technology, automatic control, communication technology, weighing technology as a whole, its control function is perfect, display, operation is centralized, data processing is convenient, installation, maintenance is simple, the system is easy to expand.

Reactor Weighing system mixes different materials and portions of powder together, based on computer technology, control technology, communication technology and graphic display technology (i.e., 4C technology), and connects on-site control stations, control and management stations, testing stations, and operation and management stations of operation and control centers (in the vicinity of the industrial site) through communication network, to complete the integrated control system of decentralized control and centralized operation and management together. Comprehensive control system for decentralized control and centralized operation and management.
The dosing production process is that the powder is evenly distributed in the hopper from each silo, the load of the spiral is detected by the weighing module through the weighing and dosing organization, and the speed of the spiral is detected by the speed generator, which is rectified and amplified and then input into the control system, which is subjected to the load signal of the spiral and the speed signal of the spiral, and then processed to obtain the actual feeding speed, and then continuously compares the actual feeding rate with the set feeding rate, and then inputs into the control system, which is subjected to the load signal and speed signal of the spiral, and then processed to obtain the actual feeding speed. The actual feeding rate is compared with the set feeding rate and the screw speed is adjusted so that the material is fed accurately at the set feeding rate, thus realizing quantitative feeding and measuring.
The weight of the material and the speed of transmission are detected and amplified by the weighing module and speed module, and then transformed into digital pulse signals by the weighing instrument and digital-to-analog conversion circuit. A PC bus control computer is used as the central controller to monitor the operation of the production line. The pulse signal of the detected quantity is isolated by the photoelectric isolation board, and then controlled by the industrial control computer to select and pass in batches and send it to the infrared control for counting, and the computer will count the weight and speed signal of the material and process it to get the actual flow rate of the dosage.
In order to improve the control speed of the whole system and make full use of some lines of the original production line controller to reduce the cost of the system, the actual flow rate and the given flow rate obtained by the computer are converted, transformed into analog signals and fed into the control circuit of the original weighing controller, and the control of the transmission speed and the flow rate control of the ingredients are realized through the excitation coil current of the clutch.
According to the requirements of the feeding system, the system software consists of the main program module, the flow information measurement and calculation module, the given value setting module, the output control module, the printing module and the data recording and archiving module, etc. The monitoring program of the system. The main program of the system is mainly responsible for the formation and management of the monitoring interface and the initialization of the counting board, digital I/O board and D/A output board in the system.
The main control interface of the feeding system includes submenus such as daily monitoring, scale transfer, power-on scale transfer, alarm file, data maintenance, print report and system description. In the daily monitoring sub-menu, the given flow rate, actual flow rate, flow rate error and set alarm error of each running production line are displayed. When the system starts to run, it is necessary to select the line number of the production line, the scale number of the Electronic scale and the powder number of the powder to be mixed through the power-on scale selection menu. The whole software adopts modularized structure, which has good inter-callability. Industrial control computer as the central controller of the whole system, the main functions it accomplishes are.
(1) Use to monitor the weight and speed signals of the production line.
(2) Calculate the error of comparing the actual flow signal with the given value; (2) Calculate the error of comparing the actual flow signal with the given value.
(3) Setting of the given value of the flow rate of each production line, setting of the line number, scale number and powder material type, setting of the flow rate alarm error, setting of the operator and the operation password; (4) Outputting the weight and speed signals of the production line.
(4) Output the given flow rate signal and actual flow rate signal to the batching machine PID control.
(5) Record, file and print function of various operation data.