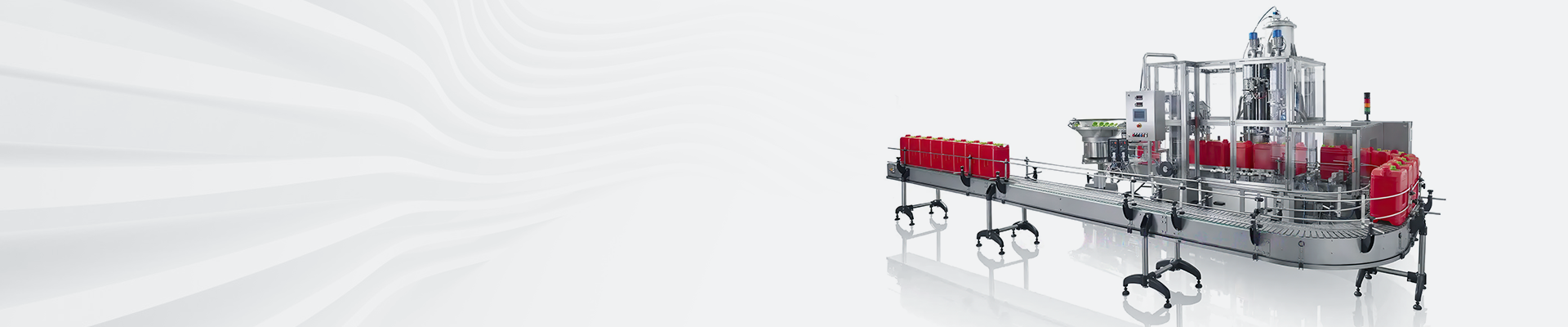
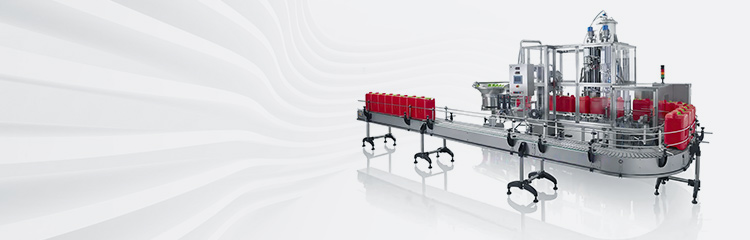

Summary:The automatic batching system consists of a computer (computer), weighing instrument, PLC and system software.Use well-known, high-performance and reliable industrial computers, PLC, weighing instruments and other high-quality components
Weighing batching machine is with the high degree of automation of modern industrial production and process control of the increasing complexity of the development of the integration of automatic control technology, computer technology and communication technology as a whole, with advanced technology, complete functionality, flexible application, reliable operation and other advantages, and with the increase in the degree of measurement instrumentation intelligence, so that the dosage system control is more flexible, more powerful. It is the more ideal control system for enterprise production process.
The feeding machine can form the intelligentization and programming of production management to achieve and improve the dosing accuracy. Strong on-site anti-interference ability, no signal attenuation, high degree of automation, decentralized risk; simple troubleshooting and easy maintenance. It consists of computer (PC), weighing instrument, PLC and system software. Dosing control system by adding a small amount of material to the mainstream material modification, or a variety of materials in a certain proportion of preparation and mixing into a new substance, is the key process of powder material production, and the application is becoming more and more widespread. Such as power plant flue gas to add calcium hydroxide, activated carbon desulfurization, wheat flour plus trace elements nutritional enhancement, water treatment to add powder, extruder, mixer quantitatively add a variety of materials, premix preparation, flux flux dosage production and so on. To accurately add a variety of trace substances to the mainstream materials, you need to choose the appropriate trace dosage system to achieve the desired goal.
Dosing classification and composition
Feeding system is mainly composed of mechanical part and control part. According to the measurement method is divided into two categories, volumetric measurement and gravity measurement. Gravimetric dosage is based on volumetric dosage by adding weighing module and weighing instrument.
Control part
Divided into volume type measurement control and gravity type measurement control two kinds.
(1) Volumetric metering control
By changing the rotating speed of feeding screw, to adjust the feeding flow, commonly used: frequency converter + gear motor, stepping motor + stepping
drive + stepping weight indicator, electromagnetic speed motor + electromagnetic speed indicator to realize.
(2) Gravimetric measurement control
Through the change of material weight in the machine, to adjust the feeding flow. It is realized by adding weighing module and weighing instrument on the basis of volumetric metering.
Mechanical part
The dosing machine is mainly composed of transmission, shaft seal, feeding screw, turning mechanism and hopper.
(1)The transmission is composed of asynchronous motor, inverter motor, stepping motor, electromagnetic speed motor, capacitor speed motor and so on, which can be selected according to the requirements.
(2) Shaft seal has the form of skeleton oil seal, copper sleeve seal, mechanical seal, etc., which should be designed and selected according to the material properties. For very fine particle size of micro-powder, such as shaft seal selection is not appropriate, it is easy to enter the reducer and make gear wear, or even failure. Used in pneumatic conveying dosage system of the shaft seal is more demanding. Conveying pressure is too high, but also need to use back pressure to prevent air leakage.
(3) The feeding screw has full face type, spring type, paddle type and screw belt type, which have their scope of use respectively. Different traits of materials need to be based on experience or experiments to determine the appropriate type of screw.
Composition and working principle of dosing
The frequency conversion system consists of a set of industrial PC management system, a set of PLC electrical control system, and N sets of single-loop closed-loop control circuits; each closed-loop control circuit consists of screw conveyor, automatic dosing system (including weighing control display, load cell, etc.), frequency converter and on-site control box. And leave the communication interface with the upper computer.
The material is conveyed into the hopper scale. The weight signal is sent to the weighing instrument. Weighing instrument will load the weight signal after arithmetic and processing to derive the weight of the material, respectively, in the weighing indicator display.
The configured weighing instrument is a high performance intelligent weighing instrument, the instrument and the frequency conversion governor control the screw conveyor speed to form a closed loop control. The built-in intelligent software regulator of the weighing instrument can set high, middle and low feeding speeds to ensure the accuracy of the dosage. The output of three sets of signals is used to control the frequency converter, which in turn controls the feeding speed of the screw feeder, so as to achieve the purpose of accurate dosage. Intelligent weighing instrument can set the feeding quantity manually, or set the proportion through the two-way communication between computer and instrument.
The industrial computer communicates with the PLC through the serial port. According to the actual process of dosage process, the ICC can reflect the operation status of feeding, dosage, delivery and related equipment in the form of dynamic screen. When there is over-limit failure during operation, there will be Chinese character alarm prompts and alarms (sound and light) will be activated to alarm, or shutdown, or change the warehouse, and the control status analysis can be made according to the operation data, and the dynamic dosage process of the system will be reflected in bar charts with different colors. According to the operation data, the industrial control machine can give the ratio or feeding quantity, and truly reflect the dosage status. In addition, the industrial control machine is installed with the dosage system developed by YUKE. The dosage system also has other functions, such as shift report, daily report, monthly report, annual report and other functions. It provides convenient management.