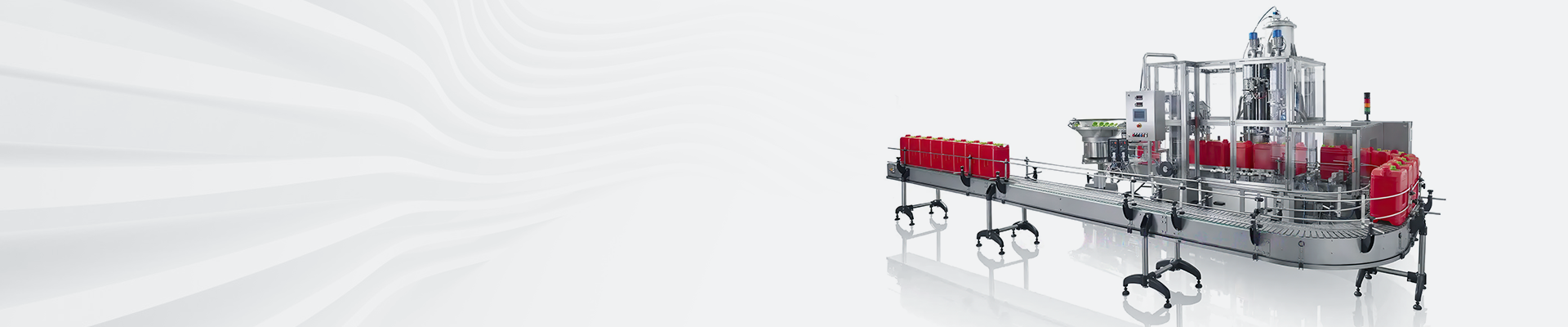
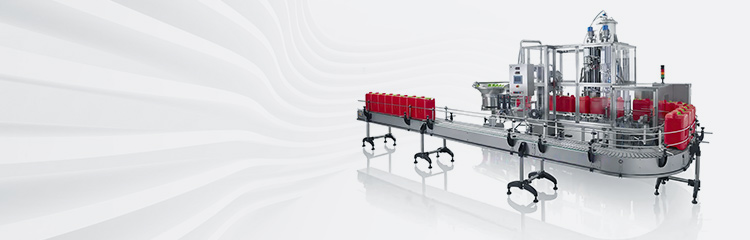

Summary:The batching system uses oil level measurement to directly measure the oil level, and the volumetric meter obtains the net oil volume.Ensure that the temperature, pressure, and viscosity of crude oil during production and operation should be as consistent as possible with the conditions during verification, so as to minimize errors in the crude oil identification process.
1.1 Flow meter dosage error
Now most of the crude oil flow dosage adopts continuous double rotor flowmeter, through the double rotor flowmeter to the flow state of crude oil for continuous dosage. Therefore, the dosage factor error of flow meter is the key to determine the accuracy of dosage. The dosage factor of flowmeter is affected by multiple factors such as temperature, pressure and viscosity of crude oil, among which temperature is the most important factor. For example, in the flow rate of 500 m3 / h, due to different crude oil temperature, the flowmeter factor will have a great change: in the crude oil temperature at 30 ℃, 26 ℃, 18 ℃, 15 ℃ and 10 ℃ under the several different temperatures, the flowmeter factor error were 0.07%, 0.14%, 0.16%, 0.17%, 0.18%. It can be seen that the higher the temperature of the crude oil flowing through the flow meter, the smaller the flow meter factor error, and vice versa. At the same time by the temperature, the pressure and viscosity of crude oil will have differences, which will also directly affect the flowmeter factor error. Crude oil temperature is relatively higher, viscosity and pressure is relatively lower, so the percentage of flowmeter factor error will be reduced. Conversely, if the crude oil temperature is relatively low, the viscosity and pressure will increase, and the percentage of the flowmeter factor error will increase.
1.2 Oil level measurement error
Oil level measurement is suitable for single static dosing. The use of oil level measurement directly measured oil level, check the storage reactor volume table to get the net oil volume. Using this method must also manually measure the density of the oil to get the quality of the net oil. So the oil level measurement is to measure the oil level in the storage reactor is mainly, and the oil quality dosing system is indirectly, affecting the quality of dosing accuracy. In our country, the reaction kettle oil level measurement is generally used to manually check the ruler to determine the height of the oil level when the error, by the checking of the ruler when the random error and the depth of the steel tape measure of the device difference. The resulting oil volume error is 0.03%.
Depth measuring steel tape calibration regulations, the calibration of the oil measuring tape when added to the tape tension for 10 Niu, but in the actual calibration, does not exclude the possibility of overweight or insufficient force. And this calibration itself has produced errors. At the same time a dipstick frequently used, although the ruler is still in the validity of the test, but because the tape is seriously distorted, so that the dosage system is often greater than the actual value of the oil height.
Oil height is one of the important parameters directly reflecting the oil storage capacity in the reaction tank. If the dosage is not accurate, the quantity of oil obtained will produce error. In the dosage of oil height, the larger the inner diameter of the reactor, the greater the error in the quantity of oil. Therefore, the operation and measurement personnel must master the characteristics of different oils and exclude the possible falsehood when dosing. Crude oil loaded reaction tank in the oil surface will often have a layer of foam, so in the presence of a large number of foam dosage reactor oil height, there is bound to be an error exists. Test results show that the foam affected by the kettle loaded oil quantity error in ± 0.1% or so.
Dosing equipment in the manufacturing process, due to a variety of objective factors so that the marked scale line does not meet the accuracy requirements. It must be corrected by using the actual measurement method. Only the correct use of the correction value, in order to eliminate the dosage of their own errors.
2 measures to protect the accuracy of crude oil handover dosage
2.1 Strictly control the flow dosage error
Flow dosage involves many factors and instruments, only to ensure the accuracy of various factors and testing instruments can ensure the accuracy of the dosage system. Therefore, on the one hand, we should strengthen the collaboration, closely cooperate with the staff of each link detection to do a good job of their own normal maintenance and inspection of detection equipment, to ensure that each link detection data is conclusive, monitoring and analysis is reasonable, the detection program is up to standard. On the other hand, it is necessary to maintain the collaboration between the two sides of the dosage handover, in the case of taking into account the common interests of both sides, to ensure that the temperature, pressure, viscosity of crude oil during production and operation should be consistent with the conditions of the calibration as far as possible, to minimize the error in the process of crude oil identification. Especially in the standard metal reaction tank, standard volume tube dosing system engineering, minimize human error, as far as possible to reduce the flow of dosing equipment in the process of dosing equipment data errors on the comprehensive quality of crude oil dosing data.
2.2 Control of oil level error
2.2.1 Measuring instruments
In order to ensure the accuracy of measurement, measuring instruments such as butyl ruler, depth measuring tape must be in the effective verification period, the technical conditions should be in line with GB13236-91 petroleum steel circle ruler and oil measuring tape technical conditions: ruler with no bending, twisting; ruler with the number of figures without falling off or clear scale; there is a calibration table; no damage to the tip of the ruler hammer.
In order to get this data, the first step is to check the scale operation of the reactor to get the height of the oil in the reactor tank. At this time to use the measuring tape, because the results of the measurement to be corrected, so try to use a more average error measuring tape, that is to say, in the conditions allow, try to use a calibration certificate given in a certain range of measurement of different heights when the error is the same measuring tape, so that in the use of interpolation correction can be very simple to calculate the error, so as to simply and accurately derive the actual height. The dosing equipment apparatus and equipment used must meet the conditions of accuracy and be used within the calibration cycle.
2.2.2 Operation process of oil height measurement
For crude oil should check empty ruler. After the oil level is stabilized, stand at the top of the kettle dosage port upwind, hold the ruler in one hand, and carefully lower the ruler along the lower ruler position of the reference point. Do not swing the ruler when lowering the ruler, and slowly lower the ruler when it touches the oil surface to prevent the stationary oil surface from being damaged. Air distance should be measured twice consecutively, the error of the two readings shall not exceed 2mm, if the error of the two readings exceeds 1mm, take the average of the two measurements; if not more than 1mm, take the first measurement.
2.3 Stabilization time of oil level
The oil level height checking must wait until the oil level is stable and the foam is eliminated before checking the scale. If the oil level is not stabilized or foam is not eliminated to check the scale, so that the height of the scale is large.
Crude oil handover dosing equipment in the dosing system personnel must undergo relevant training, licensed to work, and regular business learning, proficient in crude oil dosing methods and operating standards, constantly learning new knowledge, master the new standards.
Although there are more factors affecting the accuracy of crude oil dosage, as long as we continue to innovate working methods, strengthen the management of crude oil weighing and dosage, strictly in accordance with the relevant national standards and regulations for the dosage operation, continue to improve the technical level of crude oil measurement and dosage, and maintain a continuous and fair trade relationship between the two sides, we can crack the many problems in the automatic dosage work, and ensure the accuracy of crude oil dosage.