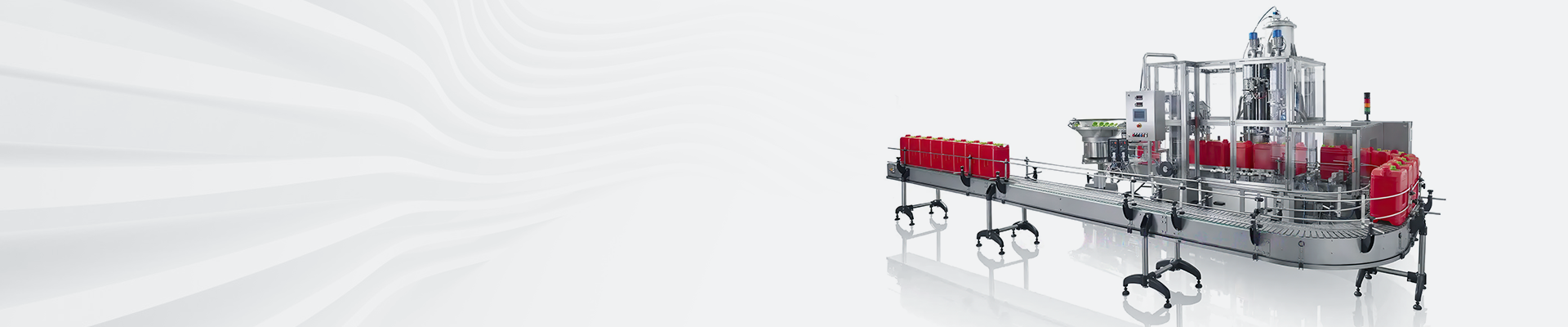
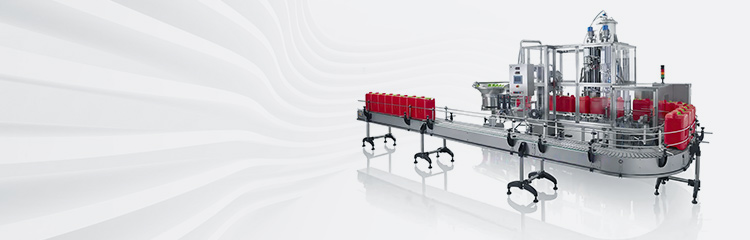

Summary:The dosing system uses the analog data input template in PLC to collect the on-site data in real time. The main collection contents include actual weighing value, belt speed, current parameters, and the running state of each equipment. The actual value is calculated according to the different ranges of the flow of each belt scale, and the average value is calculated to minimize the fluctuation of the flow, which is convenient to apply the value to the PID loop adjustment and ensure the stability of the adjustment.
0 Preface
With the acceleration of the production rhythm of blast furnace, the demand for sintered raw materials is getting higher and higher. As an important link in the source of sintering production, the blending of raw materials directly affects the follow-up process. The original raw material feeding system is basically manually operated by the operator, which has high labor intensity and low batching accuracy. Therefore, the development and operation of intelligent feeding system plays a key role in the stability of sinter quality. This system is composed of Ramzi belt weigher, QuantumPLC and related software to realize the weighing and automatic control functions in the mixed feeding system of the raw material yard. Practice has proved that the intelligent mixing weighing control system can homogenize the raw material composition, reduce the fluctuation of iron-containing raw material composition and particle size, simplify the dosing work in the raw material field, and stabilize the quality of sinter. The system has high reliability, low failure rate and intelligent self-diagnosis function, which can be directly applied to the field and has good popularization value.
1 Main technical scheme
1.1 Control system composition
According to the control requirements of the process, in line with the principle of advanced and reliable, various schemes were compared, and the control system decided to use the Quan.tumPLC automation platform, which is not only conducive to the networking of the entire raw material and sintering control system, but also conducive to the collection of energy control data. The programming software adopts CONCEPT, and the monitoring software adopts IFIX, which can realize the equipment monitoring and remote operation of mixed ingredients.
1.2 System Control functions
IFIX monitoring software to achieve real-time data collection of material flow and material level, through the screen value setting and operation buttons, PLC program data exchange, to achieve voice alarm, belt start early warning, record various historical trends, material head and tail alignment, can be set at any time, flow setting, frequency setting switch, empty warehouse automatic change function. Manual automatic undisturbed switching and production process logic control functions.
2. Specific technology research
2.1 Data collection of belt scale flow and bin level
The data of the field are collected in real time by using the analog data input template in PLC. The main contents are actual weighing value, belt speed, current parameters and the running state of each equipment. The actual value is calculated according to the different ranges of the flow of each belt scale, and the average value is calculated to minimize the fluctuation of the flow, which is convenient to apply the value to the PID loop adjustment and ensure the stability of the adjustment. The display of the material level is one way on site and one way in the main control room, which is convenient for real-time monitoring of the material level of the silo from both sides, and ensures that on-site personnel take charging measures when the material level is low to prevent the occurrence of material cut off.
2.2 Switch between ratio setting, flow setting and frequency setting
The frequency of the feeding disc is controlled in two ways by using PLC output and instrument. It can switch to the instrument output when the PC given system fails, ensuring the continuity of production. The field disk inverter is controlled by setting ratio, flow rate and frequency when PLC is output. The operator selects the proportioning time on the operation screen, and only needs the total flow of the input ingredients and the proportioning ratio of each scale, the feeding amount of each scale can be automatically calculated, and the feeding amount can be tracked and adjusted according to this. This method reduces the work of the operator to calculate the flow rate of each component according to the ratio, and the calculation is accurate. Flow setting is to control the flow of each sub-scale through the flow given area on the screen, and this setting method is required for PID parameter tuning of each scale. The frequency giving rule is to fix the output frequency of the frequency converter of the field disc, which needs to be used in the physical calibration scale. In the case of a given frequency, the feeding amount of each belt scale is compared with the weighing value of the total belt scale, and the flow of the belt scale is corrected according to the difference. This method is both intuitive and convenient, and the accuracy is very high, eliminating the workload of the calibration personnel carrying the weights, saving time, and can be verified with high precision in a very short time.
2.3 Voice Alarm
When there are problems such as card and suspension, the system can be judged to be running according to the running state of the belt scale and the disk feeder. If the flow display of a belt scale is lower than the alarm set value, it can be determined that the warehouse has been cut off, and the voice file can be played in time to warn the operator through the scheduling function of IFIX. At this time, the operator should solve this problem in time to avoid problems with the ratio of the mixed material. When the problem is solved, the alarm is automatically lifted, and it can also be manually lifted by the operator on the operation screen. The alarm will be automatically generated and stored in the alarm log, alarm log can be generated every day - a file, query alarm information only need to be the day of the alarm file can be called out, this file can also be opened in notepad format, easy to copy the alarm information, so as to print.
2.4 Align the head and tail
The purpose of mixing ingredients is to mix a variety of different raw materials together in a certain proportion. When starting or stopping, the blanking time interval of each bin is calculated according to the distance between each belt scale and the speed of the total belt, that is, the last bin is opened first when the boot is started. When the material head runs to the bottom of the previous bin (7"), the 7" bin begins blanking, and so on. Until all belt scales are turned on. Stop the last bin first (when the tail runs under the previous bin, the bin stops feeding, and so on, until all belt scales have stopped. This ensures the mixing accuracy of the mixture when starting and stopping.
2.5 Belt start warning
The function of belt start warning is to reduce personal accident injury. The operator can open the belt after confirming that there are no working personnel on the scene. The bell will ring for 5s before the belt is opened, giving the personnel standing near the belt enough time to stay away from the belt and avoiding the occurrence of safety accidents caused by the belt start. Stop ringing the bell when the belt starts. When the belt does not run after the bell rings 5s or the belt has run but the running signal is faulty, the bell will not stop and will continue to ring for 25s to remind the operator that there is a running fault, which needs to be coordinated quickly to ensure the normal operation of the production system.
2.6 Records of historical trends
The data of belt scale is very important in the production process, and the previous batching situation is often queried. According to this demand, the historical trend of belt scale flow and the historical trend of each warehouse material level are made. And the given flow of each belt and the actual flow do the same historical trend of the screen, according to the rate of change of the two curves to view the stability of the automatic adjustment and the actual change of the material flow. And adjust the PID parameters according to the size of the fluctuation to make the automatic adjustment more stable operation.
2.7 Logical control of the production process
In actual production, the interlocking function of each equipment is very important, and the interlocking start and stop provide great convenience to the operator, and also realize the alignment of the head and the tail. When there is a fault, the fault shutdown system comes into play. During the batching process, if the system is in the interlock state, in order to ensure the accuracy of the batching, any belt will stop running, and the rest of the belt will also stop running at the same time, and the operator will restart the system after the fault is solved. If the equipment fault is difficult to eliminate in a short time, in order to ensure production, the operator only needs to change the status of the equipment to "not selected", then the equipment does not affect the linkage of the system, and its ratio will not be calculated. In the non-linkage state, each device can be controlled independently, which is conducive to the individual debugging of the device. Each belt has a deviation protection function. When the deviation protection function is turned on and the belt deviation is detected, the belt will be stopped immediately to prevent accidents.
2.8 Hands-free automatic switching
When the weighing control system is running, it can be automatically switched according to the need. In order to ensure the stability of the feeding amount, when the ratio or flow setting is switched to the frequency setting, the current PLC output frequency is assigned to the manual frequency setting. When switching from a frequency set to a flow set for PID adjustment, assign the current flow value to the set value of the flow. Ensure that the material flow does not change after switching. The accuracy of the ingredients is guaranteed.
2.9 Unit switching and accumulation maximum
Since the units of common flow are th and kg/m, the habits of different operators are different, so according to the running speed of each belt to calculate the measurement of kg/m, the operator can operate on the screen to change the unit of flow, the program will also automatically calculate the corresponding flow value in accordance with the current unit setting. The increased shift accumulation, work accumulation and total accumulation can allow the operator to see the current total amount of ingredients at any time, which is more convenient to measure the amount of ingredients at each stage, eliminating the complicated calculation process of the operator.
2.10 Automatic exchange system for empty positions
Set the material type of each bin on the main screen, and the system will automatically determine the warehouse number of the same material type. When among them... When a bin is empty or out of material, the system automatically adjusts the ratio of the two bins, adds the ratio to the fault-free bin, and alerts the operator by voice. When the operator handles the on-site fault, the ratio can be adjusted back to the original state, which not only improves the batching accuracy, but also reduces the failure shutdown rate.
3 Conclusion
After the system was put into use, it ran well, greatly improved the precision of mixing ingredients, from the original 8% to 1%~0.5%, reduced the labor intensity of operators, and further improved the quality of mixing materials, which played a great role in stabilizing the quality of sinter. The automation system has not stopped due to the system so far.