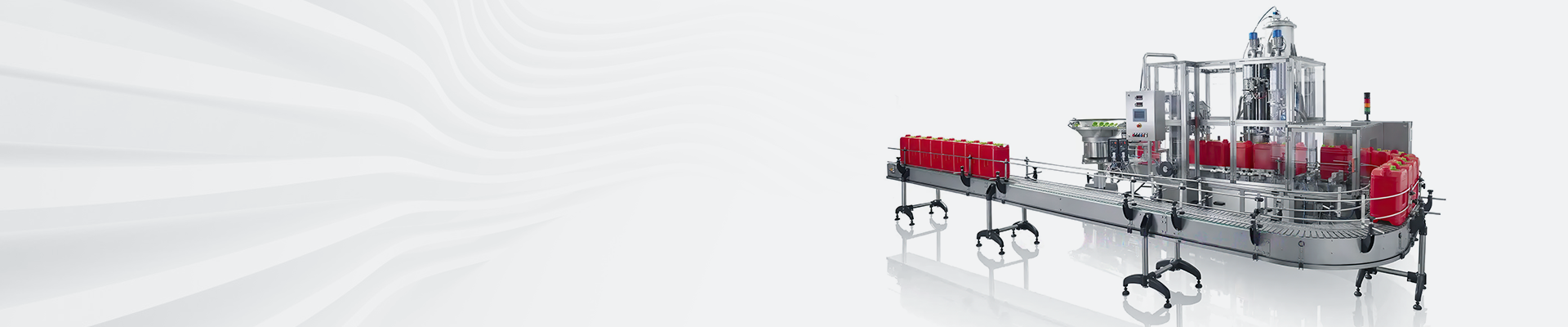
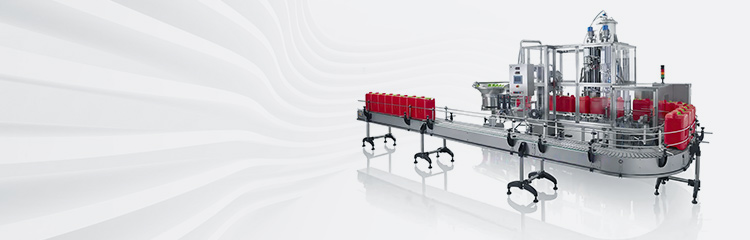

Summary:The automatic filling machine can adjust the filling volume by changing the speed of the frequency converter gear. The pulse signal of the weighing controller distributes liquid to the filling container through the filling valve and controls the switch of the solenoid valve.
Programmed and controlled according to the process requirements, the weighing system and PLC program control the weight and flow of the material loaded into the weighing drum, thus realizing accurate measurement and batching. With strong stability and high cost performance, it can provide accurate measurement data and control means for production control and management in various industrial sites. Filling through the time and unit time flow rate to determine by the programmable controller (PLC) control to determine, through the human-machine interface - touch screen monitoring of the operating state, can be modified online operating parameters. Through the weight transmitter transformed into 4~20mA current as the input signal for system display and control, the current weight of the raw material barrel as the starting weight setting value, and through the display instrument or DCS system set as the target dosing value, when the weighing module detects the weight in the canned barrel rises to a certain value, at this time, the output current and the weight value is basically a linear relationship, in order to ensure the accuracy of each point, the filling In order to ensure the accuracy of each point, the liquid level signal of the filling barrel is used as the control signal of the feeding valve for the automatic adjustment of the liquid level parameter, so that the whole automatic filling machine realizes the automatic adjustment function of the continuous production process. The weighing system integrates weight information collection, amplification, transformation, transmission, processing and display, and controls the sensors, relays, switches and solenoid valves through PLC program. It draws on the advanced technology and techniques, and combines with its own long-accumulated experience to integrate the inventory management, filling management, filling and weighing, process control and product traceability, etc., and adopts the barcode (two-dimensional code / RFID) Identification, wireless transmission, automatic weighing, PLC control, electromechanical, computer interface and other automation technologies, independent development and completion of intelligent filling weighing and inventory management system, to prevent the filling of wrong materials, to ensure the accuracy of the weighing, to ensure the accuracy of the filling process, so that each batch of filling data are recorded and traceable, and in the raw materials out of the warehouse to follow the principle of first-in, first-out, an effective solution to the waste of raw materials.