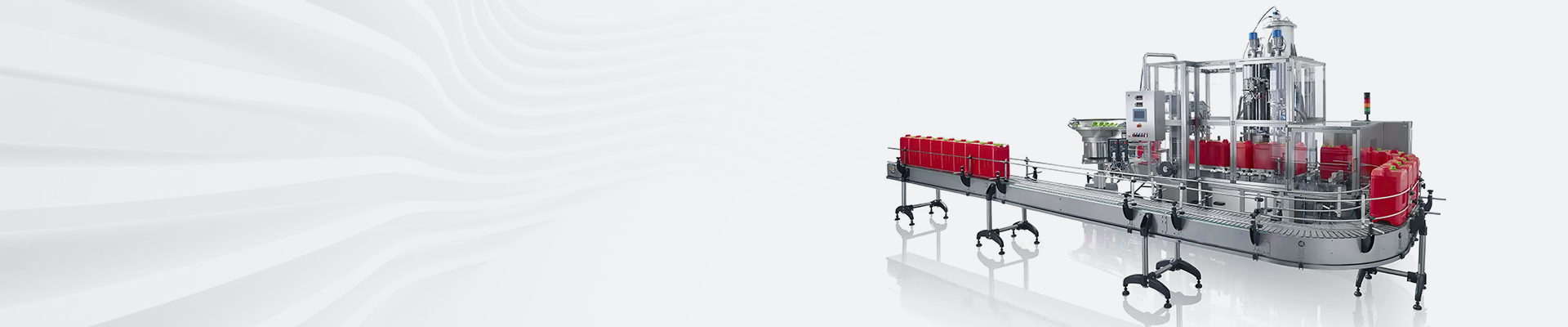
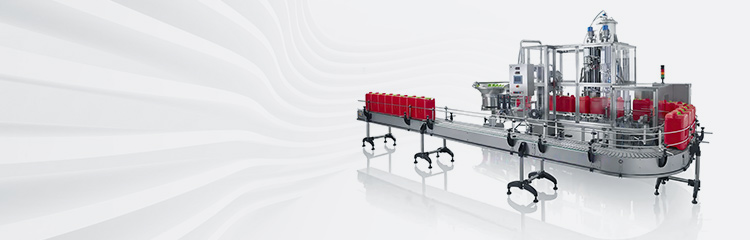

Summary:The automatic batching system is a continuous feeding and dynamic measurement system for continuous weighing and measurement of solid bulk materials (blocks, granules, powders, etc.). It accepts signals from the weighing module and speed sensor on the hopper scale, calculates and displays the output flow signal to the host. machine, and can independently output control current to the frequency converter for speed regulation.
Weighing and batching system is the ideal equipment for continuous weighing and feeding of bulk materials, which is a high-tech product integrating conveying, weighing and measuring and quantitative control, and is famous for its advanced technology, stable and reliable, high cost performance and durability. It can be adapted to various production environments, and can continuously feed and measure all kinds of lumps and granular materials (such as calcium titanate, iron powder, titanium dioxide) and powder materials (such as granules and powder), and provide accurate measurement data for production control and management of various industrial sites. Equipped with RS485 upper computer communication interface, can be composed with the central control machine DCS system. Weighing and feeding system is the ideal choice to replace imported equipment. Feeding capacity 0.05m3/h-1000m3/h, conveying bandwidth 500mm-1800mm, roller center distance 1000mm-8000mm, specific size can be customized according to user requirements.
Feeding Principle
The feeding system transmits the load and speed signals of the conveying belt to the measuring and controlling weighing instrument or I.C.C. The weighing instrument or I.C.C. will calculate the actual feeding quantity by internal arithmetic of the load and speed signals, and constantly compare the actual feeding quantity with the set feeding quantity to control the speed of the conveying belt so that the feeding quantity will be as close as possible to or equal to the set feeding quantity.
Dosing and measuring part
1、Weighing frame
2、Weighing module
3、Speed sensor
4、Weighing controller
Touch screen controller
Ordinary type controller
Batching system software
According to the control of starting and stopping the feeder in the dosage system, it can be divided into the following two kinds:
Controllable feeding system is divided into mixing system controlled by PLC and batching system controlled by PC with I/O board according to different control equipment. The principle of the two ways is more or less the same, only the communication mode of the control part is different.
Principle of dosage system
The program of weighing and batching system communicates with PLC (I/O board), reads the status (operation status, alarm status, etc.), and writes commands to control the starting and stopping of each equipment; at the same time, the program communicates with each weighing instrument, reads the data of each feeder weighing instrument, writes the batching program, and sends the flow of batching of each feeder to each weighing instrument, which makes the batching adjustment.
General functions of batching system
Dynamic display of system operating conditions, set values, instantaneous values and totalized values of materials;
Display the whole system operation status and alarm status;
Display the trend curve of various materials discharging and proportioning;
Automatically set the proportion according to the input parameters;
Historical data query (shift totalization, daily totalization, monthly totalization and yearly totalization);
Sound and light alarm function;
System-wide linkage control;
Online help function, easy to operate;
Functions
Dosage monitoring
The dosage control system reads the main totalization, instantaneous flow, set flow, weighing instrument status and other relevant data from the weighing instrument. The status of the weighing instrument is displayed (zero, interval, running or alarm). The dosage system reads the status of the dosage equipment from the PLC (hopper scale remote, running, deviation, breakage, alarm, etc.), and displays the status of each feeder, so that the monitoring personnel can have a comprehensive understanding and control of the equipment.
Ratio setting
Proportioning total flow
Flow distribution (proportioning)
Calculation of the flow rate of each feeder
Write to the weighing meter (set flow rate) and to the PLC (selected)
After inputting the total flow of the batch and then selecting the feeder to be started, the selected feeder will automatically calculate the flow according to the set ratio, and automatically transmit the set flow of each feeder to each feeder weighing instrument; the selected feeder information will be sent to the PLC to prepare for startup.
Communication Setting
Setting the communication protocol between PC and PLC and related parameters including: serial port, baud rate, parity, word length, stop bit, etc.
Setting of the serial port: the set value of the serial port is the same as the serial port of the PC connected to the weighing instrument.
Communication protocol: the communication parameters in the instrument are the same as those in the software.
Note: the communication port cannot be set the same for both types of communication.
Data query and printing
The program produces daily batch and shift reports based on the data stored in the database, such as batch and shift totals or bin totals, and generates daily and yearly statistical reports. Statistics of each material (or each warehouse) according to the material name (or warehouse number).
Querying of ratio list reports.
These data reports are typed out in a standardized format through a printer.
Raw material field batching system as an example, as shown in the previous figure, the raw material field has a total of ten hoppers, according to the process requirements of different materials.
In the production process, the material in the hopper through the disk feeder to the lower level of weighing belt feeder, and through it to the big belt.
The raw materials in each bin are mixed on the big belt according to a certain proportion and sent to the next process, and the batching is finished.
Each hopper is installed with four bin wall vibrators, disc feeder with fan.
Each feeder is designed with a junction box for relay wiring of the quantity module and speed sensor, a field operation box for starting and stopping the feeder on site, and an anti-bias switch for detecting belt deflection.
The large belt is equipped with an on-site operation box as well as anti-skew and pull-wire switches.
Ten hopper scales share two weighing instrument cabinets, five frequency conversion cabinets, one PLC cabinet, and one power cabinet. There are also a number of operating consoles.
The control of the whole system is completed by an industrial computer and a PLC.
In the upper computer, 10 sets of hopper scales to form a multi-material weighing and batching system, the upper computer can be based on the formula table, automatically set the specified material flow to each scale weighing controller.
The industrial computer communicates asynchronously and serially with the weighing controllers via RS485.
The computer sequentially reads the data in the weighing instrument for processing, and also adjusts the parameters in the weighing instrument, records and manages the data collected in real time from each scale, establishes the data archive and data query, completes various statistical reports and prints them out.
Each belt hopper scale is a self-contained system, where the flow requirements can be set either on the weighing control instrument or on the host computer.
Through communication between the industrial computer and the PLC, data and control commands are transmitted to realize belt interlocking, sequential delayed start, sequential delayed shutdown, fault alarms and so on.
The 10 hopper scales can be started and stopped on site or centrally controlled in the control room for sequential start and stop of each scale, and there are operation and fault indicator lights on the operation desk to indicate the running status of the equipment.
The dosage can be divided into three-layer structure, namely, human-computer interaction layer, relay control layer and field operation layer.
The human-computer interaction layer uses Advantech Industrial Control 610;
The relay control layer adopts the centralized control mode and selects Siemens S7-300;
The field operation layer is composed of program control system with PLC through relays, contactors, anti-deviation switches and so on.
The upper computer and PLC use RS485 communication to realize PLC offline programming, online debugging and upper computer monitoring;
The accumulator accepts signals from the weighing module and speed sensor on the hopper scale to calculate and display the output flow signal to the host computer, and can independently output the control current to the frequency converter to adjust the speed;
The host computer and the frequency converter use RS485 communication to communicate and realize the frequency conversion speed regulation;
The starting and stopping of each hopper scale, disc feeder, disc motor fan and vibrator can be carried out through the operation box on site or controlled by the operation desk installed in the centralized control room.
Characteristics of the dosing system
High resolution weighing modules with a minimum displacement of 0.1 mm guarantee accurate measured values. High resolution digital pulse speed sensor to ensure accurate speed values are obtained. Gravity automatic tensioning device ensures constant belt tension, avoiding belt slippage and excessive tension. Belt automatic deviation correction device avoids affecting production due to belt deflection. Pear-shaped scraper clears the debris on the lower belt to one side, avoiding the debris between the belt and the roller surface to damage the belt. Scrapers on the inside and outside of the belt avoid belt sticking and tare changes. Without assistance, the belt is easy to replace, simplifying maintenance. The master and slave pulleys adopt self-aligning bearings, which is very convenient for installation and adjustment.
Main Technical Parameters
The actual feeding accuracy of various bulk materials is better than ±0.5% of the set feeding rate. Feeding rate is about 50kg/h-180t/h. Conveying bandwidth is 500mm-1800mm. roller center distance is 2000mm-8000mm, adopting plug-in system, the size can be customized according to user requirements. Output interface: various optional, can be connected with DCS system. Ambient temperature: scale body -10℃~+60℃ weighing instrument -10℃~+45℃ working power: weighing instrument AC220V±15%50Hz±2% scale body AC380V±15%50Hz±2%.
Ordering instructions for the correct scientific selection of equipment, the user must provide the following material parameters:
(1) Material name;
(2) Maximum feeding capacity and adjustment range (t/h);
(3) Maximum particle size of material (mm);
(4) Average weight (t/m3);
(5) Material moisture content (%);
(6) Material temperature (℃);
(7) The actual alignment distance from the scale body to the electric control cabinet (m);
(8) Whether the driving mechanism is left or right mounted;
(9) an electronic control cabinet to install a number of weighing and batching system if the old equipment renovation should also provide the site of the horizontal layout of the dimensions and space height dimensions, the center distance between the inlet and outlet, the bottom of the coupling flange dimensions, etc..