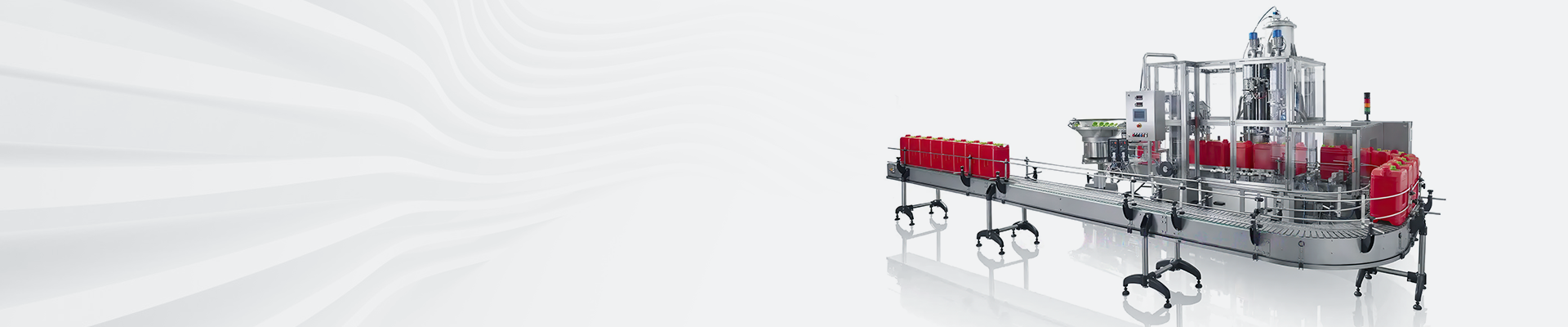
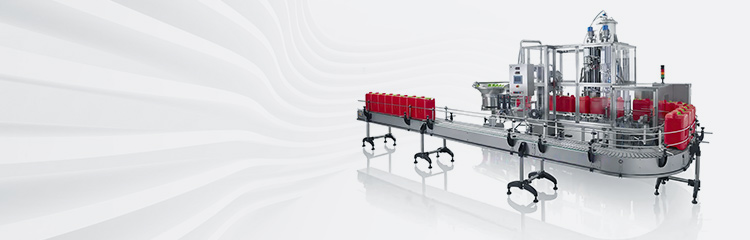

Summary:The automatic batching system provides powder with a stable flow rate. The powder enters through the batching feeder. The speed of the batching feeder is adjusted based on the comparison result between the instantaneous flow measurement value and the set value, so that the instantaneous value always tracks the set value, thereby realizing the feeding control. Quantity measurement and control.
Powder measurement and automatic dosing system must have the functions of accurate measurement, stable feeding amount, adjustable, fast response, etc., and the realization of these functions must first be based on accurate measurement. The batching feeder is the key equipment of the system. It is a powder material metering device developed through independent innovation. The batching feeder is the technical core of this research project.
System principle
The automatic batching system is affected by the batching speed when the powder moves in the uniformly rotating reference system, and is equipped with a measuring disc, on which several measuring blades are arranged radially. The measuring disc rotates at high speed under the drive of the motor spindle. The material to be measured falls to the center of the measuring disc, changes its flow direction through the parting cone, is captured by the blade, and moves radial to the outer edge under the action of centrifugal force. In the process of movement, the material is subjected to radial friction Fr and reverse centrifugal force Fx, as well as the action of tangential Fc, Fc causes a reaction motion torque M, and Fr, Fx will not produce a reaction torque on the drive shaft. The mass flow rate of the material can be obtained by measuring the action torque of the batching speed Fc on the measuring disk.
Research and innovation
The automatic batching system uses the principle of batching rate theory to measure powder materials. Firstly, the radial movement of materials in uniform rotating reference system is taken as the condition. Therefore, in theory, the following two basic conditions must be met:
(1) The speed of the measuring disc must be constant;
(2) The material must move from the center of the measuring disc to the outside diameter. In theory, it is not difficult to meet these conditions, the key is how to reflect in the best structural design. According to the calculation formula M=QωR2, it can be seen that the effective speed range of the measuring disc must be determined, and the ideal speed must be selected from the effective speed range. It is necessary to determine the ideal radius of the measuring disc, and many related technical parameters such as the number and size of the measuring blade Settings. In this study, under the guidance of theory, according to the calculation formula, through a lot of experimental research, the empirical formula is obtained, which can be used to guide the structural design of the balance.
Study on the ideal speed of measuring disc
Batching control system measuring disk speed is related to the flow rate, flow rate, quantity value of the material. The research of measuring disk speed is one of the important contents of this project, and it is an indispensable technical parameter for structural design. According to the vector expression Fc=-2mω×v ', the speed of the measuring disk (or angular velocity ω) is related to the relative velocity v 'of the particle, which determines the amount of Fc received by the particle.
Based on the simulation test and theoretical analysis, the effective speed range of the measuring disc is determined first. However, the study of effective speed only solves the value range of angular velocity ω, which can not provide specific parameters and basis for design. In order to obtain the ideal speed parameters, in the semi-industrial test, the powder, calcium carbonate, titanium dioxide were measured by the experimental prototype, and the ideal speed of the measuring disk was obtained on the basis of sampling analysis.
Study on ideal radius of measuring disc
The relative position of the particle moving on the measuring disk of the feeding system is different, and the quantity value is also different. Therefore, the measuring disk radius is related to the quantity value of Fc. The study of the ideal radius of the measuring disk is related to the reasonable size of the structure, the measuring capacity, the sensor range, the power configuration, the structure optimization, and the series design. The theoretical formula can not provide the ideal radius of the measuring disk, only through experimental research can we establish the empirical formula which is consistent with the optimal design.
As mentioned above, the measuring disc is provided with a radial measuring blade, and the material falling into the center of the measuring disc moves to the blade under the action of the parting cone, is caught by the blade, moves along the blade to the outer diameter, and is affected. Since the material is not affected until it is captured by the blade, the measuring disk should be divided into an effective measuring area and an ineffective measuring area from the point of view of force, and the measuring blade part is an effective measuring area. The material is not affected in the invalid measurement area, which can also be called the measurement blind area. Therefore, the measuring disk radius should be divided into two parts: effective radius and invalid radius, and the effective radius is equal to the blade length. This makes the study of the ideal radius of the measuring disk more complicated, because the ideal radius consists of two parts: reasonable effective radius and invalid radius. On the basis of repeated experiments, the correction coefficient is obtained, and the empirical calculation formula is derived and established to guide the optimal design of different specifications of measuring disks.
Development of batching and feeding device
The stable and adjustable feeding amount is the basic requirement of the feeding system of the new dry batching production line. This project puts the development of the stable feeding technology and device in an important position, abandoning the previous concept of attaching importance to the metering technology and ignoring the feeding device. Firstly, the effects and requirements of material characteristics and process conditions on the performance of the feeder are analyzed. The feeding device is located at the bottom of the powder bin, the change of the material level in the powder bin and the impact force of the feed flow will affect the feeding stability. Powder fineness, low moisture, small volume weight, good fluidity, especially smokeless material mixing process, powder fineness is usually less than 1%, making stable feeding more difficult. The moisture of powder has certain influence on the stability of feed. Excessive moisture will lead to problems such as powder arching, dipping and poor feeding. Especially in the rainy season, or during the heating of the rotary kiln ignition, many powder moisture does not meet the requirements of the process conditions. Therefore, the structural design of automatic batching system should consider the adaptability when the moisture is high. The pressure change of powder mixing system will also indirectly affect the feeding stability of the feeder. When the system working condition is not normal, the pressure of the feed pipeline will sometimes fluctuate, which will lead to poor feeding or unable to run of the weighing batching system.
1. Research on structure and working principle of batching feeder
Through the research and analysis of material characteristics and technological conditions, this project adopts a completely different design scheme from the traditional feeding device, and develops a new structure of the feeding device ----WD horizontal rotary batching system.
The automatic dosing system is composed of powder reducing bin, equalizing bin and distributing bin. The pressure reducing bin is provided with a pressure reducing device so that the material entering the pressure equalizing bin is not affected by the pressure of the bin. The mixer is provided in the equalizing silo to fully activate the material, avoid the arch of the material, stick to the wall, and eliminate the dead zone of the material. Because the material pressure in the equalizing bin is uniform, the conditions are created for the material to enter the rotor cavity under the same bulk weight condition. The batching chamber is provided with a horizontal rotary dividing wheel, which transports the same volume of material every turn. Weighing batching is driven by shaft mounted reducer and motor, and the motor speed is adjusted by frequency converter, which is controlled by PLC. According to the comparison between the instantaneous flow detection value and the flow set value, PLC regulates the speed of the feeder in real time, so that the instantaneous flow always tracks the set flow and realizes the purpose of quantitative feeding.
The inlet and outlet of the decompression bin, equalizing bin and dosing chamber are arranged in 180° dislocation, and the material can only leave the feeder through labyrinth flow inside. In addition, an elastic sealing material is used on the blade of the horizontal rotating grating in the rotor cavity to achieve zero clearance. Therefore, it can effectively solve the problem of material running and punching under the change of material pressure and self-gravity.
Technical performance
Feed uniform and stable, not affected by warehouse pressure, material characteristics;
Strong ability to adapt to pressure changes in process system;
The feed rate is stable and adjustable;
Reasonable structure, reliable performance, simple maintenance.
Development of a new type of screw pump
1, the role of the screw pump in the batching system
The screw pump plays the role of conveying and locking the air in the batching system. Under the premise of effectively overcoming the pressure of the conveying pipeline system, the measured powder is quickly and evenly sent into the conveying pipeline. When the pressure in the pipeline changes or the pressure of the conveying air fluctuates, the screw pump must be able to effectively block the powder backchanneling and the poor discharge performance to provide normal working conditions for the metering equipment.
2, the new screw pump technical characteristics
The new screw pump adopts simple transmission structure, adopts variable pitch screw design, and applies the principle of injector, so that the working atmosphere of the discharge end of the pump is basically negative pressure, which effectively solves the influence of the pressure change of the feeding pipeline system on the discharge of the screw pump; The shaft end seal adopts the technical solution of gas seal, oil seal and mechanical seal, which meets the requirements of oil resistance, high temperature resistance and wear resistance, and the sealing performance is superior. The wear-resistant material technology with independent intellectual property rights is applied to the design and manufacturing process of the pump, so that the service life of the spiral blade is more than 2 times higher than that of the "Fule pump" surfacing technology under the same conveying capacity. The external adjustable counterweight can change the force of the damping valve according to different working conditions, so as to solve the problem of reasonable density of the plug. It is easy to lubricate moving parts with manual yellow oil pump. The new screw pump integrates the traditional screw pump and the reasonable composition of the imported Fule pump, adds a unique innovative technology, reliable performance, novel structure, simple maintenance, low operating costs, and meets the requirements of metering and automatic batching system. According to the comparison between the measured value of instantaneous flow and the set value, the speed of the batching feeder is adjusted by feedback, so that the instantaneous value always tracks the set value, and the measured powder enters the powder conveying pipeline through the new conveying pump. The dosing system adopts PLC control (programmable controller), and the signal collected by the sensor is transmitted to the transmitter, which is processed by the transmitter and converted into the standard signal accepted by the PLC (4 ~ 20mA) to meet the communication requirements with the PLC.