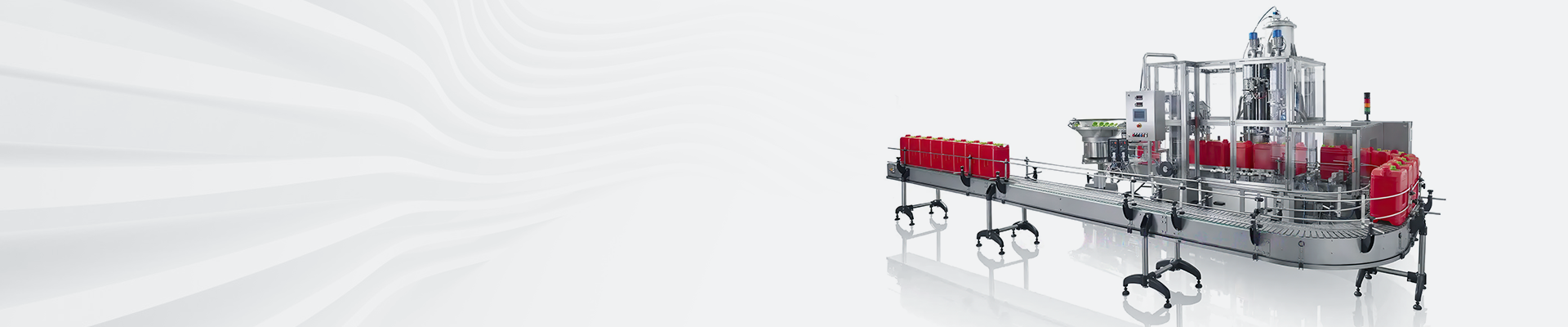
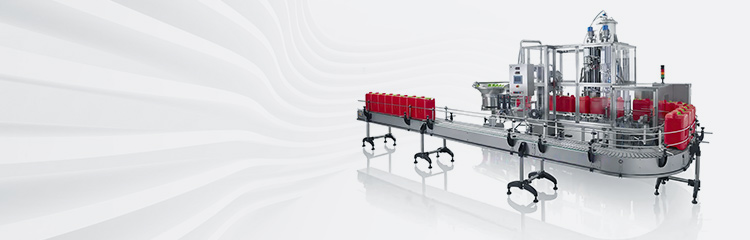

Summary:The batching system detects the weight of the silo, and the actual measurement of the material can be obtained by calculating the reduction in weight of the silo per unit time.By controlling the frequency of the frequency converter, the simulated batching amount at the required speed of the metering spiral (or metering pump) can be obtained by timely adjustment to achieve the purpose of metering batching.
In many industries on solid materials (including some very high concentration is not easy through the ordinary pipeline measurement of liquid materials) of the measurement of the feeding system are used in special measurement of the dosage unit, such dosage unit is generally expensive, not easy to maintain, once the damage to the supply cycle is very long, that may lead to equipment downtime. General purpose weighing unit combined with the powerful functions of PLC to replace the special measuring and dosage system unit, to achieve the purpose of reducing investment, easy maintenance, and can be accurately measured.
Automatic dosage systems for glue, pigments and other additives can be measured and dosed through the structure of the human-computer interface to read and write process parameters, the implementation of the measurement and other process parameters of real-time monitoring. Due to the measurement of solid material dosage, it can not be used in the pipeline as in the case of liquid measurement, but only through the weight calculation of the material silo to get the actual weight. The principle is as follows: the material enters the automatic dosage system through the metering screw (or metering pump), and the weight of the silo will gradually decrease. The dosing system unit detects the weight of the silo and calculates the actual weight of the material by the reduction of the weight of the silo per unit of time. The measured values of the process parameters are sent to the metering and dosage system unit via Modbus. The feeding system unit is specially designed by the supplier to automatically calculate and adjust the analog dosage quantity of the required rotational speed of the metering screw (or the metering pump) under the given metering data, and the analog quantity is sent to the CPU through the remote analog input unit of the PLC, and then the frequency of the frequency converter is controlled through Profibus to achieve the metering and dosage frequency of the metering and dosage system unit. The analog quantity is sent to CPU through PLC remote analog input unit, and then control the frequency of frequency converter through Profibus to achieve the purpose of dosing. The advantage of this structure is simple to use, no need to specialize in the design of the dosage program, because the dosage unit can operate independently according to the given measurement required by the process. The disadvantage is the high cost of metering and dosage unit is not easy to maintain, strong dependence on the supplier, once the damage to the supply cycle is very long, will likely lead to equipment downtime.
The following describes a general-purpose weighing unit combined with the PLC's calculation function constitutes the measurement of the batching system, for reference.
Automatic batching system for flour metering and batching of the structure of the frame, in the weighing and batching system we use the CPU is A-B's SLC-500, and the use of a Profibus-Scanner module under the hanging of a general-purpose weighing unit and frequency converter. The network structure is simple, through the human-machine interface to the process parameters read and write can be real-time monitoring of flour measurement and other process parameters.
The dosage process is as follows: the measured value of the flour required for the process is written from the HMI and sent to the PLC through the DH+, the weight value of the weighing unit of the flour silo is sent to the PLC through the Profibus, and the weight of the silo is gradually reduced when the flour passes through the metering screw and enters into the automatic dosage system, and the PLC calculates the reduction in weight of the flour silo per unit of time to get the actual measurement of the flour. The PLC can get the actual measurement of flour by calculating the weight reduction of the flour bin per unit time. And then use this actual measurement and preset measurement comparison, PLC after certain calculations can get a relatively stable frequency value, (metering screw (or metering pump) rotating one week output volume is relatively stable, dosage control speed on the control of the dosage volume that is the weight of the dosage system), as long as the frequency value through Profibus to the dosage of metering screw speed can form a Closed loop dosage for flour metering.
In this dosage must be noted that with the gradual reduction of flour silo, the silo will have a feeding process, although the feeding process is relatively short, but because in this process the measuring screw in the non-stop out of the material, and the silo at the same time in the material, it is clear that the measurement of the process of feeding is certainly inaccurate, the design of the program must take into account this point. We can feed the process of frequency value can be given in this way: one is the use of silo in the instant before the frequency value as a constant frequency in the process of feeding (because the frequency value is to meet the requirements of the process parameters), until the end of the process of feeding and then re-entered the normal measurement, due to the feeding of a relatively short period of time, generally does not affect the quality of the products of the automatic dosage. However, the disadvantage of this practice is that if the process parameters in the process of adding changes, as this time the use of a constant frequency, the actual measurement of flour will not change with the change of process parameters and changes in product quality may cause fluctuations. Another dosage should be more perfect, that is, in the normal measurement at the same time the PLC can get a frequency and flour measurement of the linear relationship, in short, is the number of Hertz corresponds to the number of kilograms of flour measurement. In the dosing project we can use this linear parameter to dosage system output frequency value, in this way of dosage system is under, even if in the dosage process to change the process parameters, the actual measurement of flour
It can be seen that the use of special dosage unit and ordinary weighing unit in the dosage principle is the same, the difference is that the use of general weighing unit dosage way to reduce the input and output links, more reasonable use of the PLC, giving full play to the PLC powerful calculation function, the structure of a simpler, smaller investment.