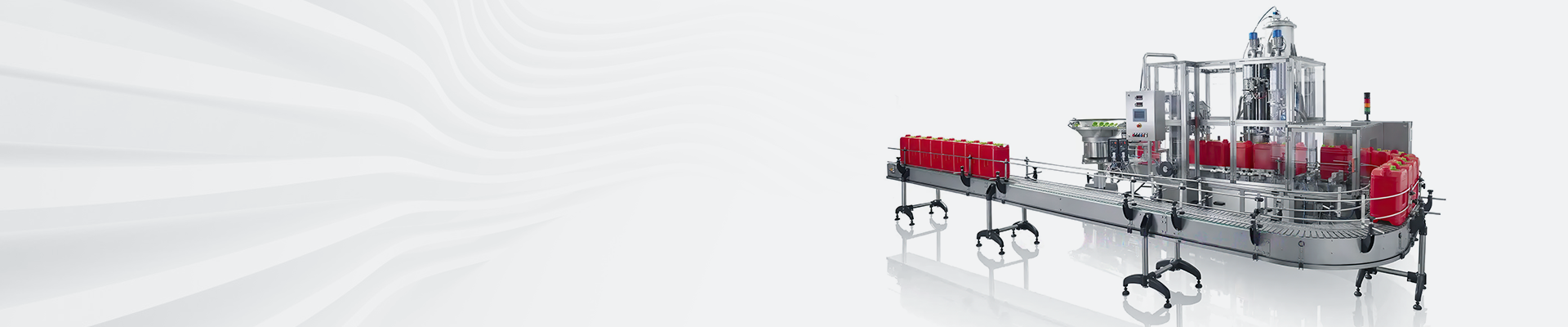
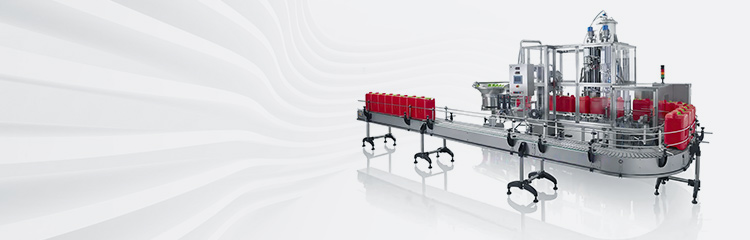

Summary:The batching system mainly consists of a PLC controller, a signal amplification transmitter, a frequency converter, an industrial microcomputer and related circuit electrical appliances.It can automatically and timely process the electrical signals fed back according to the set program to ensure that the flow rate of the powder does not exceed the set deviation value.
From the measurement method, the existing weighing control system for the measurement of raw materials is no more than volumetric measurement and weighing measurement of these two ways. The so-called volumetric measurement, is a kind of material by controlling the volume of material flow per unit of time to achieve the control of material weight flow measurement. The most typical application is the use of speed motors to control the speed of the raw material conveyor belt conveyor to control the delivery of raw materials, this measurement method has been widely used in the measurement of raw materials. Weighing measurement, as the name suggests, is a kind of weighing module according to the weight of the feedback signal on the weight of raw materials to make direct adjustments to control the flow of measurement. Commonly used in the mixing and feeding system on the belt scale, spiral scale and reduction scale in three forms. Weighing measurement and volumetric measurement, compared with more timely, direct weight flow to make adjustments to control the relative accuracy of measurement is also higher, more with the combination of microcomputer control technology, to achieve satisfactory control accuracy requirements.
According to the Ministry of Transportation issued the "mixing and feeding system technical requirements", the measurement accuracy of raw materials required for 3%, the measurement accuracy of powder requirements for 1%, the measurement accuracy of powder requirements than the measurement accuracy of raw materials require a lot higher. And from the analysis of the cost of raw materials composition of stabilized soil materials, in each ton of finished raw materials containing powder is only about 5%, but its value is higher than the other 95% of the total value of raw materials. From the actual use of the point of view, whether using volumetric measurement or weighing measurement, the user has never objected to the measurement accuracy of raw materials, but the measurement accuracy of the powder from time to time complaints, which can be seen in the performance of powder measurement accuracy in the automatic dosage system accounted for the important position. Comprehensive analysis of the above, we can come to the conclusion that: weighing and batching system measurement accuracy is determined by the powder measurement accuracy; powder measurement accuracy in the finished product to ensure stable quality of raw materials under the premise, but also allows the user to get better economic benefits. For example, in a practice, the requirements of the powder gradation between 4.5% and 5.0%, if the powder can be accurately controlled at 4.5%, the finished raw materials are also considered qualified, compared with the intermediate value of 4.75%, can save powder 0.25%. If calculated according to WCB500 batching daily output of 4000t, it can save 10t of powder, about 3500 yuan. Assuming that the pavement project is 200,000t of mixing volume, the cost of saving powder is 175,000 yuan. Therefore, the accuracy of powder metering is the key to evaluate the performance of mixing and batching, and to improve the accuracy of powder metering is not only an effective means to ensure the quality of the user and control the cost, but also one of the goals pursued by the manufacturer of mixing and batching system.
At present, the powder metering system configured for mixing and batching mostly adopts the weighing metering method, and the volumetric metering method is gradually being eliminated. There are two main types of weighing batching system: spiral continuous weighing and reduction scale weighing, but the latter is less used because it takes up more space, and most of them use the traditional spiral continuous powder metering device. The weight signal collected by the weighing module on the spiral scale is fed back to the control system, and through the comparison and processing of the control system sends a command to the impeller to give the raw material to the speed control motor on the material to control the flow of the powder, so as to keep it in a relatively stable range, to achieve the measurement of the powder. Simply from the structure, this measurement method does not have any great defects, but, in actual use the effect is not satisfactory. From the fully automatic dosage, powder measurement is not just a weighing problem, but also involves the supply of powder, the structure of the raw material warehouse, powder raw material level of high and low, the composition of the speed regulating mechanism and weighing the structure of the spiral form and so on, any one of the links on the problem will directly affect the accuracy of the measurement of powder. When the powder tank at the bottom of the powder hitch (almost every powder tank will occur such failures), although the weighing spiral has measured the lack of raw material signals and impellers to the raw materials to accelerate the operation, but still can not guarantee that the powder flow increase, then the finished product in the raw material is bound to be insufficient powder content. In addition, because the weighing spiral is too long, its own weight is heavy, will also affect the powder measurement accuracy; impeller to raw material device blade sticky raw materials will also cause powder measurement deviation; spiral pipe diameter, pitch selection is not appropriate to make the powder for raw materials feedback speed is not timely ...... for the above problems, we need to re-from all aspects of the comprehensive In view of the above problems, we need to reconsider the powder metering accuracy from all aspects.
Weighing and batching system has developed a kind of domestic most advanced powder continuous weighing and measuring device by analyzing a large number of practical application examples and making pioneering experiments on the problems occurring under various working conditions. The device has achieved good results in construction and is well received by users. Here is a brief introduction to the following, I hope to give the majority of counterparts to help and enlightenment. In order to automatically and continuously supply the powder used in the mixing and batching system with uniform raw materials and ensure the accuracy of grading, the industrial microcomputer program is used to control the powder continuous weighing and measuring device to solve the defects of the powder measuring device on the existing mixing and batching system, and the technical means are as follows.
1. Powder bin for raw materials with inclined screws
Powder bin volume of 9m3, in the upper and lower limit position is equipped with a spinning original material level meter; using frequency conversion technology screw motor for stepless speed regulation to control the size of the supply volume; spiral and the horizontal plane into a certain angle of inclination, in the exit to form a section of the buffer zone, which can effectively prevent the self-flow of the powder to ensure that the stability of the powder flow; according to the mixing and dosage system for the powder powder supply of the raw material range, to determine the spiral machine According to the range of powder material supply required by the mixing and batching system, determine the pitch of the screw machine and the diameter of the blade. The above configuration can ensure the continuous and stable supply of raw materials, and can respond to the signals from the control device in time.
2. Adopt single pivot point suspended screw weighing device.
Measuring and batching system to reduce the weight of the spiral and from the point of view of aesthetic considerations, the spiral pipe selection of thin-walled stainless steel pipe, shaft end support selection of cast aluminum raw materials. Weighing module selection of pull-type weighing module, this device can be instantaneous powder flow weight detection, and converted into electrical signals transmitted to the control device.
3.Measuring and control device
Weighing and batching system mainly consists of a PLC controller, a signal amplifier transmitter, a frequency converter, an industrial microcomputer and related circuitry and electrical components. It can automatically and timely feedback back to the electrical signals according to the set program for arithmetic processing, to ensure that the flow of powder does not exceed the set deviation value, while the microcomputer system also has an alarm display, statistical printing and other functions.
According to the above program after the transformation of the mixing and batching system has dozens of units in practice around the country, users generally reflect the powder measurement is more accurate, in improving the quality of finished raw materials, saving construction costs have obvious results.