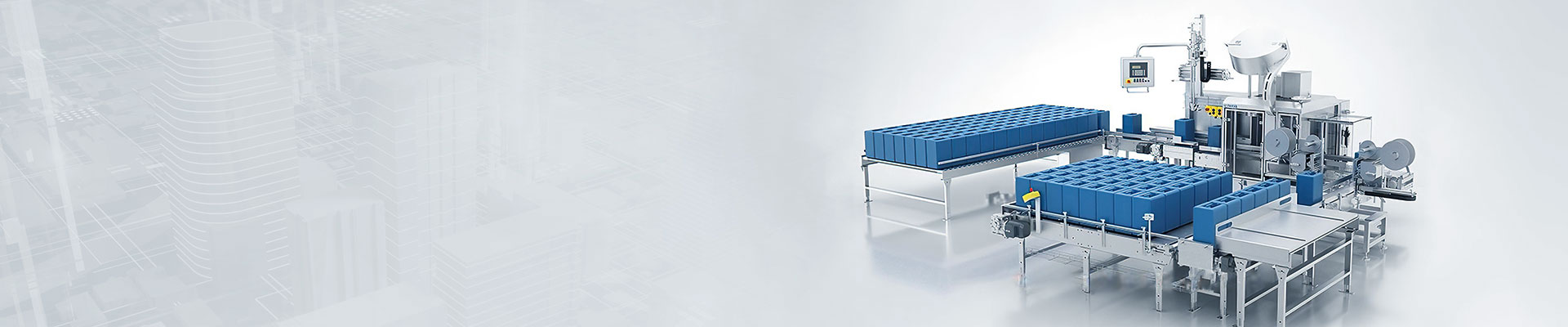
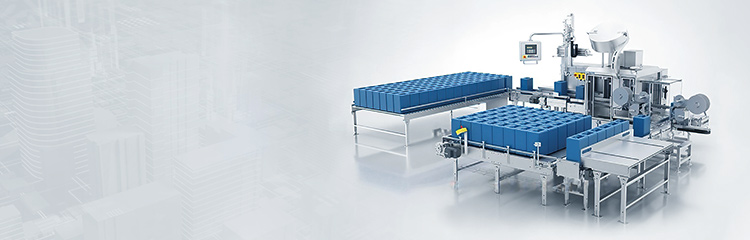
The liquid filling machine is controlled by the inverter controlled by the Profibu bus, and its speed can be set on the control panel touch screen. Every day before and after filling, all pipes of each filling machine are cleaned CIP in place by a PLC control system with hot water of about 85 degrees. After filling every week, the PLC control system will carry out CIP cleaning of all pipes of each filling valve by about 85 degrees of alkali water.

The liquid Filling machine gets the liquid first into the high buffer tank at the valve station, and the role of this high buffer tank is to ensure that the filling machine's ring cylinder and each filling valve are supplied with enough liquid under the condition of high speed filling. Before the empty tank enters the filling machine, it is cleaned with about 80 degrees of hot water through an S-shaped slide to ensure that the empty tank entering the filling machine is clean. There is a weighing module at the lower part of each filling valve of the weighing filling machine. After filling, liquid of equal quantitative value is injected into the empty tank first. The weighing module measures the weight of the packaging container in real time and transmits it to the PLC control system. Then the control system reinjects the quantitative liquid into the filling valve for filling the next tank.
Since the filling must ensure that the liquid temperature when injected into the empty tank should not be lower than 85 degrees, there is a liquid return pump automatically adjust the liquid to the heat exchanger in the feeding part of the circulation heating. Each empty tank is filled with the set value, and the liquid enters the gland machine to achieve the case sealing of the tank. The cover of the capping machine is provided with adequate cover by the automatic Feeding machine. The filling speed is controlled by the inverter controlled by the Profibu bus, and its speed can be set on the control panel touch screen. Every day before and after filling, all pipes of each filling machine are cleaned CIP in place by a PLC control system with hot water of about 85 degrees. After filling every week, the PLC control system will carry out CIP cleaning of all pipes of each filling valve by about 85 degrees of alkali water.