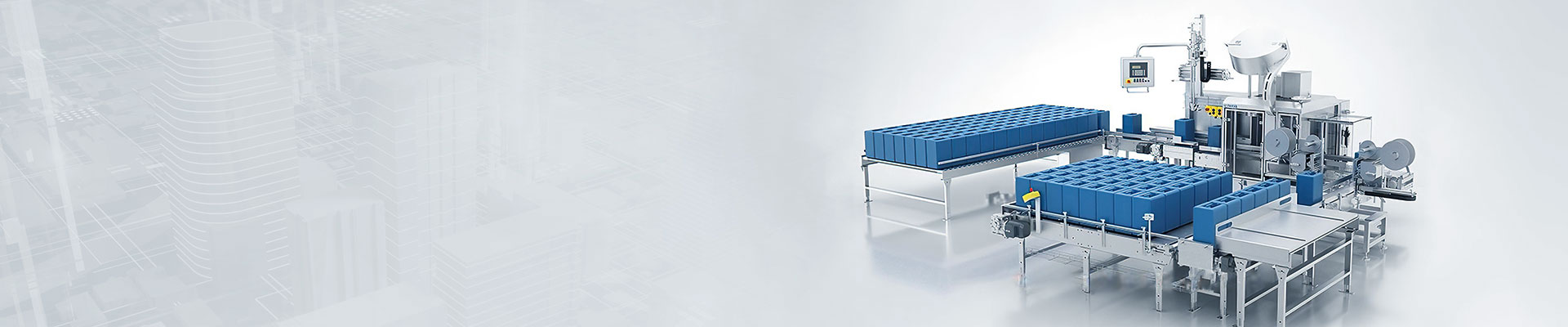
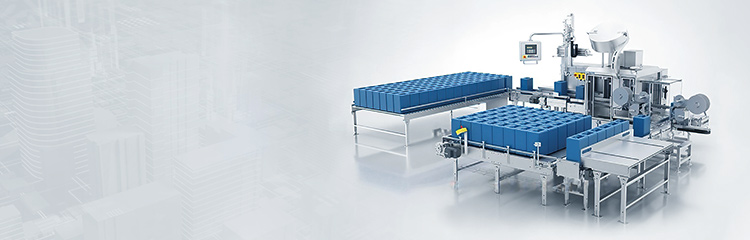
Hydrochloric acid filling machine adopts Siemens PLCS7-300 system, programmable controller design filling scanning, filling management and other process control, in the relevant database information service based on the installation of Kingview software, filling production line monitoring interface, the use of Kingview internal PLC system to achieve the connection with the field control. The intelligent multi-function panel is adopted, the man-machine operation interface is simple and applicable, the configuration is applicable, the modification is convenient, and the complete man-machine dialogue state is realized.

Weighing and Filling machine only needs to put the same specifications of drums neatly in the designated position, using PLC programmable controller, polytetrafluoroethylene manufacturing, two-stage automatic filling of size material, filling head height can be adjusted by hand, suitable for packaging drums of different heights, with automatic identification of empty drum function and empty scale does not fill function, equipped with manual buttons for all actions, For manual operation in case of accident, the dual window displays the special filling control instrument, which can display the information of target quantity, filling quantity, barrel number, time and date.
Automatic filling machine Weighing and filling integration of the ideal weighing equipment, in the filling automatically remove the tare, the material in the container when the first large amount of rapid filling and then slow small dose correction measurement. When the container is sent into the weighing platform, the conveyor runs at the same time, and the photoelectric sensor detects that the signal sent after the arrival of a container controls the motor to stop. The photoelectric sensor detects the signal sent when the container reaches the filling position, the PLC controls the conveyor to stop, the automatic peeling and filling valve is driven down by the stepper motor, and the drop limit is reached by the stroke switch to send a signal, and the PLC controls the filling valve to fully open for filling. When the set value is reached, the solenoid valve moves the filling valve to open half for filling, and at the same time, the stepper motor drives the filling valve to rise through the lead screw at a pre-set speed. When the filling weight requirement is reached, the filling valve is closed, the filling valve reaches the upper limit, the stroke switch stops sending a signal, and the PLC simultaneously controls the motor weighing conveyor to run at the same time until the finished product is output. Then the container is placed on the electronic weighing platform, and the barrel mouth is aligned with the filling mouth. At this time, the program starts, the filling mouth automatically drops, and the filling valve is opened to feed. The filling nozzle rises to complete the filling process.